Расточка коленвала: Расточка блока, ремонт коленвала, гбц, шатуна, кпп в Казани | Услуги
Расточка блока, ремонт коленвала, гбц, шатуна, кпп в Казани | Услуги
РЕМОНТ БЛОКА ЦИЛИНДРОВ
Восстановление пастели распределительного вала.
Опрессовка блока (проверка на микротрещины).
Восстановление посадочных мест под водяной насос.
Восстановление посадочных мест под гильзы.
Восстановление коренных пастелей блока.
Расточка блока цилиндров.
Расточка цилиндров.
Гильзовка блока цилиндров.
Расточка коренных пастелей блока.
Хонингование блока цилиндров.
Фрезерование поверхности блока.
РЕМОНТ КОЛЕНЧАТЫХ ВАЛОВ
Восстановление
Правка
Проверка на микротрещины
Проверка на твердость
Полировка
Шлифовка
РЕМОНТ ГОЛОВОК БЛОКА ЦИЛИНДРОВ
Мойка ГБЦ
Дефектовка ГБЦ
Замена седла
Притирка клапана
Замена втулки направляющей
Замена стакана форсунки
Замена маслосъемных колпачков
Фрезеровка ГБЦ
Опрессовка (проверка на трещины)
Восстановление пастели распредвала в ГБЦ
Замена втулок распредвала
Ремонт трещин, устранение прогаров, сколов, раковин в теле ГБЦ.
РЕМОНТ ШАТУНОВ
Контрольные замеры шатунов
Расточка втулок шатуна
Замена втулок шатуна
РЕМОНТ РАСПРЕДЕЛИТЕЛЬНЫХ ВАЛОВ
Восстановление кулачков
Правка
Проверка на микротрещины
Проверка на твердость
Полировка
Шлифовка
КАПИТАЛЬНЫЙ и ЧАСТИЧНОЙ РЕМОНТ ДВС.
РЕМОНТ РЕДУКТОРОВ.
РЕМОНТ КПП.
РЕМОНТ РАЗДАТОЧНОЙ КОРОБКИ.
РЕМОНТ КОМ.
РЕМОНТ МОД.
РЕМОНТ ГУРа.
РЕМОНТ ЭНЕРГОАККУМУЛЯТОРОВ.
РЕМОНТ ТУРБОКОМПРЕССОРОВ.
РЕМОНТ КОМПРЕССОРОВ.
РЕМОНТ СТАРТЕРОВ.
ДИАГНОСТИКА и РЕМОНТ ТНВД.
ДИАГНОСТИКА и РЕМОНТ ФОРСУНОК.
ВОССТАНОВЛЕНИЕ КОРПУСОВ КПП, РЕДУКТОРОВ, РАЗДАТОЧНЫХ КОРОБОК.
ТЕКУЩИЙ РЕМОНТ ТРАНСМИССИИ ГРУЗОВОГО А/М.
КУЗОВНОЙ РЕМОНТ ГРУЗОВОЙ И АВТОБУСНОЙ ТЕХНИКИ.
Кузовной ремонт кабин, фургонов, автобусов с применением специализированных стапелей.
Восстановление геометрии деформированных рам грузовых автомобилей.
ДОПОЛНИТЕЛЬНЫЕ УСЛУГИ
Аргонная сварка
Сварочные работы
Мойка деталей
Токарные работы
Доставка
как и для чего ее проводят
Коленчатый вал двигателя внутреннего сгорания представляет собой один из основных элементов кривошипно-шатунного механизма, являясь деталью достаточно сложной формы. К коленчатому валу (в области шеек коленвала) реализовано крепление шатунов. Через шатун от поршня на коленвал передается усилие, что позволяет преобразовать возвратно поступательное движение поршней в цилиндрах во вращательное движение коленчатого вала.
Необходимо отметить, что коленвал в процессе работы двигателя испытывает значительные нагрузки, так как давление газов в результате сгорания топливно-воздушной смеси воздействует на весь КШМ, параллельно на него воздействует инерционная нагрузка и т.д. В совокупности все силы, оказывающие воздействие на элемент, переменные по своей величине и направлению. По этой причине к детали выдвигаются особые требования касательно прочности и материалов изготовления, что необходимо для способности успешно противостоять таким нагрузкам. При этом деталь, как и любой другой нагруженный элемент, рано или поздно выходит из строя. В этой статье мы поговорим о том, что такое расточка коленвала, когда нужна данная ремонтная процедура, а также как проводится расточка и шлифовка коленвалов.
Содержание статьи
Почему и в каких случаях нужна расточка коленчатого вала
Так как коленвал является нагруженной деталью, о его неисправностях водитель может узнать по появлению стука в двигателе. Если коленвал начал стучать, силовой агрегат нуждается в неотложном ремонте. В блоке цилиндров сам коленвал лежит в так называемой постели, закреплен посредством коренных подшипников скольжения (коренные вкладыши). Также в месте крепления шатунов к валу имеются шатунные подшипники (шатунные вкладыши). Материалы для изготовления вкладышей используются такие, чтобы элемент был прочным и имел гладкую поверхность. Это необходимо для минимизации трения в месте контакта вала и вкладыша, а еще позволяет валу свободно вращаться. На вкладыши в обязательном порядке дополнительно подается моторное масло из системы смазки, что и обеспечивает бесперебойную работу механизма.
Становится понятно, что идеальные поверхности вкладышей и шеек коленвала, полученные при изготовлении деталей благодаря тщательной полировке, подвержены износу в процессе эксплуатации двигателя.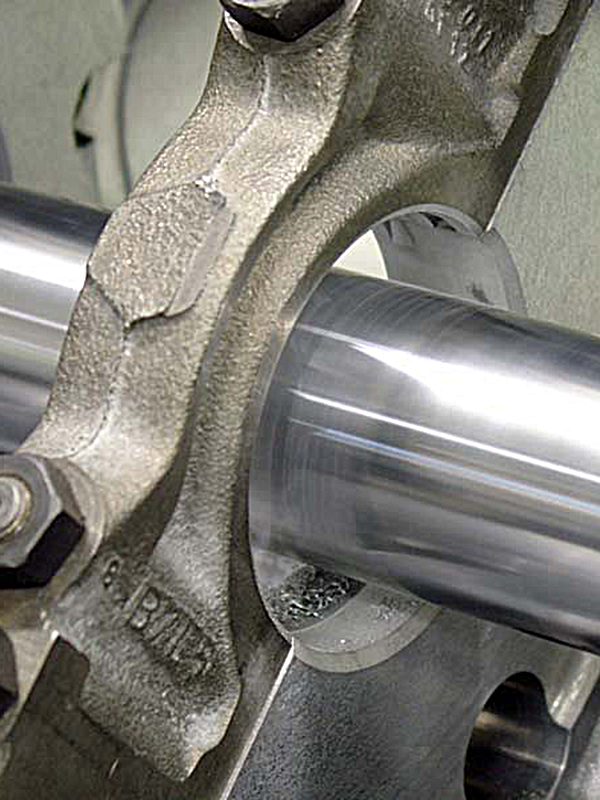

Необходимость ремонта вала возникает и в том случае, если вкладыши рабочие, но на самом валу имеются производственные дефекты (брак). Эта ситуация возникает естественным образом, проявляясь в процессе эксплуатации. Другими словами, расточку проводят тогда, когда пострадали шейки коленчатого вала. Возникновение задиров, канавок, износ шеек коленвала более 0.03 мм. уже принято считать основанием для расточки, так как полное восстановление гладкой поверхности шеек попросту невозможно без этой процедуры. Вкладыши после расточки также нужно будет менять.
Если суммировать полученную информацию, общее состояние поверхности шеек коленчатого вала сильно зависит от того, в каком состоянии находятся вкладыши коленвала. Указанные элементы должны быть подогнаны друг к другу с филигранной точностью, чтобы сопряженная пара (шейка-вкладыш) могла нормально работать при условии значительных и постоянно меняющихся нагрузок. Добавим, что частой проблемой многих ДВС является проворачивание вкладышей коленвала. Нужно помнить, что если вкладыш провернуло, заменить один или все вкладыши без расточки коленвала будет недостаточно. По этой причине для проведения квалифицированного ремонта двигателя необходимо:
- определить износ вкладышей коленчатого вала;
- выявить дефекты коленвала;
- реализовать предварительную расточку коленвала;
- осуществить установку вкладышей соответствующего ремонтного размера;
Другими словами, во время капремонта мотор полностью разбирается, после чего двигатель дефектуют, проводятся различные замеры при помощи нутромера, микрометра и другого оборудования. Затем на основании полученных результатов при необходимости проводится расточка блока цилиндров, коленвала, фрезеруется и шлифуется ГБЦ, осуществляется расточка постели коленвала и т.д. Только после выполнения всех этих операций подбираются ремонтные поршни и кольца, а также вкладыши коленвала и другие детали. Отметим, что заранее приобретать ремонтные запчасти не рекомендуется, так как во многих случаях расточка может производиться специалистами не в следующий, а сразу через один ремонтный размер или даже более. Это зависит от характерных особенностей имеющейся выработки, глубины повреждений и т.п.
Как растачивается коленвал
Начнем с того, что расточка и шлифовка коленвала своими руками в гаражных условиях под силу только опытным специалистам, которые имеют соответствующий набор специального оборудования. Прежде всего, в наличии должен быть станок для расточек коленвала, так как вся процедура должна выполняться с высокой точностью. Нужно учитывать и то, что от качества работ с коленвалом будет напрямую зависеть и сложность дальнейшей подгонки ремонтных вкладышей.
Также некоторые автолюбители в целях максимальной экономии умудряются шлифовать коленвал в гараже подручными средствами, но выполнять данную процедуру настоятельно не рекомендуется, так как результат может быть абсолютно непредсказуемым.
Добавим, что перед началом работ специалист должен обязательно проверять коленвал на предмет осевого смещения шатунных шеек, искривления коленчатого вала и т.д. При этом все равно получается, что хотя ремонт вала представляет собой сложную токарную операцию, купить новую деталь все равно получится в среднем на 50-60% дороже сравнительно с тем, сколько стоит расточка коленвала опытным мастером.
Подведем итоги
Для экономии денежных средств во время проведения капитального ремонта двигателя владелец автомобиля при желании всегда может взять разборку агрегата на себя. Самостоятельное снятие навесного оборудования, демонтаж ДВС и его извлечение из подкапотного пространства, а также мойка мотора позволит ощутимо уменьшить общую стоимость затрат. Если имеются навыки и инструменты, сам двигатель также можно разобрать у себя в гараже, доставив для дефектовки и расточки только отдельные элементы (например, ГБЦ, БЦ или коленвал). Последующую сборку мотора также можно провести самостоятельно.
При этом следует помнить, что замена вкладышей и расточка коленчатого вала является сложной процедурой. Если вы не уверены в своих силах, лучше полностью доверить весь процесс разборки, ремонта и сборки двигателя специалистам. Дело в том, что в автосервисе с хорошей репутацией имеется нужное оборудование, стенд для ремонта двигателя и т.д. В таких условиях мотор тщательно промывается изнутри, очищаются масляные каналы, труднодоступные полости. После ремонта на двигатель обязательно должны дать гарантию, так как в процессе сборки все детали перед установкой проверяются мастером и подгоняются при необходимости прямо на месте. Это позволяет упростить процесс сборки и экономит время, возможные дефекты обнаруживаются и устраняются до того момента, когда мотор уже стоит на автомобиле.
Не следует забывать и о том, что от качества моторного масла и своевременной замены смазочного материала и фильтров напрямую будет зависеть ресурс отремонтированного ДВС. Обратите внимание, шатунные и коренные вкладыши являются теми деталями, которые первыми выходят из строя в случае проблем с системой смазки двигателя. По этой причине следует следить за уровнем масла, использовать соответствующие данному типу силовой установки ГСМ, избегать активной езды на холодном моторе и т. д.
Читайте также
Работы по блоку цилиндров | Цена | ||
---|---|---|---|
Расточка и хонингование | ВАЗ 2101 -2112 | 3500 | |
ГАЗ 406, ГАЗ-405, ГАЗ-409 | 3500 | ||
иномарка, в том числе через ремонт | (за цилиндр) | 1250 | |
иномарка (алюсил) | (за цилиндр) | 6500 | |
мото | (за цилиндр) | 2000 | |
Дохонинговка (восстановление сетки хона) | 50% | ||
Гильзовка и хонингование блока цилиндров (со стоимостью гильзы) | ВАЗ, Таврия, «Ока» | 2500 | |
ГАЗ 406, ГАЗ-405, ГАЗ-409 | 2500 | ||
УАЗ (в 100мм) | 4500 | ||
иномарка (чугун) гильза чугун | (за цилиндр) | 5000 | |
иномарка (алюминий} гильза чугун | (за цилиндр) | 5000 | |
иномарка V-образный (чугун) гильза чугун | (за цилиндр) | 6000 | |
иномарка V-образный (алюминий) гильза чугун | (за цилиндр) | 6000 | |
Гильзовка cummins Газель 4 цилиндра (под ключ) | за блок | 16000 | |
Ра6ота по 1 цилиндру или съем более 1 мм | +20% | ||
Дополнительные у слуги по блоку цилиндров | |||
Замена вкладышей ВПМН | ВАЗ 2101 -2107/ ГАЗ 406 (без стоимости материала) | 1000/2000 | |
Иномарка | (за опору) | 1500 | |
Перепрессовка поршней | ВАЗ, ОКА | (за единицу) | 250 |
Иномарка | (за единицу) | 600 | |
Шлифовка ВПМН в ремонтный размер | ВАЗ 2101-2107 | 600 | |
в ремонтный размер | ГАЗ-406 | 1200 | |
Шлифовка коленвалов | |||
Шлифовка коленвала | Отечественные | 3500 | |
ГАЗ | 3500 | ||
«Ока» | 1750 | ||
иномарка (3 -4 цилиндра) | 5300 | ||
иномарка (5-6 цилиндров) | 7300 | ||
иномарка (8 цилиндров) | 8ЗОО | ||
Шлифовка только (шатунных или коренных) шеек | -40% | ||
Шлифовка коленвала с сохранением галтелей | +50% | ||
Шлифовка коленвала с узкими шейками (менее 20 мм) | +50% | ||
Дополнительные у слуги по коленвалу | |||
Полировка коленвала | отечественные | (за вал) | 1000 |
иномарка | (за шейку) | 200 | |
Рихтовка коленвала | отечественного | 600 | |
прогиб до 0,4 мм | иномарка | 1300 | |
прогиб более 0,4 мм (без гарантии) | иномарка | 1300 | |
Обработка поверхности под упорные полукольца | 1200 | ||
Снятие и установка заглушек, чистка каналов | ВАЗ, ГАЗ | 1000 | |
Балансировка коленвалов в сборе | ВАЗ | 1ВОО | |
ГАЗ | 1300 | ||
Иномарка | 2300 | ||
Восстановление маслосгонной накатки | ГАЗ | 700 | |
иномарка | 1000 | ||
Работа по ГБЦ | |||
Головки блока цилиндров | ВАЗ, Москвич, ГАЗ, Таврия, Ока | (за деталь) | 1000 500 |
ВАЗ, Москвич, ГАЗ, Таврия, Ока (шлифовка) | (за деталь) | 1000 | |
иномарка (фрезеровка) | (за цилиндр) | 500 | |
иномарка (шлифовка) | (за цилиндр) | 500 | |
не параллельные плоскости | 650 | ||
Блока цилиндров | отечественные / Ока | (за деталь) | 1500/800 |
иномарка | (за цилиндр) | 750 | |
ВАЗ 2101-21033.![]() | (за деталь) | ||
Ока | (за деталь) | ||
ГА3-402, АЗЛК | (за деталь) | ||
ГАЗ-406, ВАЗ 2112 | (за деталь) | ||
Сборка ГБЦ, регулировка зазоров | ВАЗ 2108-21083 | (за деталь) | 2500 |
Рассухарить клапана | ВАЗ, ГАЗ-402, ГАЗ-406, АЗЛК, Ока, Таврил | (за единицу) | 50 |
Иномарка, Мото | (за единицу) | 50 | |
Засухарить клапана | ВАЗ, ГАЗ-402, ГАЗ-406, АЗЛК, Ока, Таврил | (за единицу) | 50 |
Иномарка, Мото | (за единицу) | 50 | |
Замена маслосъемных колпачков | ВАЗ, ГАЗ-402, ГАЗ-406, АЗЛК, Ока, Таврил | (за единицу) | 100 |
Иномарка, Мото | (за единицу) | 100 | |
Замена направляющих втулок клапанов | В АЗ 21 01-21083, Ока, Таврил | (за единицу) | 100 |
ВАЗ 2112; ГАЗ-402, ГАЗ-406, АЗЛК | (за единицу) | 100 | |
Иномарка и Мото (в том числе разворачивание отверстий под ремонтные клапана) | (за единицу) | 250 | |
Правка седел | ВАЗ.![]() | (за единицу) | 100 |
ГАЗ 402, АЗЛК | (за единицу) | 100 | |
Иномарка, Мото | (за единицу) | 250 | |
Работа по одному клапану | (за единицу) | + 50% | |
Правка рабочей фаски старого клапана, чистка | ВАЗ. ГАЗ-402, ГАЗ-406, АЗЛК, Ока, Таврил | (за единицу) | 200 |
Иномарка. Мото | (за единицу) | 200 | |
Притирка клапана | ВАЗ, ГАЗ-402, ГА3-406, АЗЛК, Ока, Таврил | (за единицу) | 100 |
Иномарка и Мото. Правка старого клапана перед притиркой обязательна!!! | (за единицу) | 100 | |
Замена седла с изготовлением седла | Отечественные автомобили | (за единицу) | 1500 |
Иномарка, Мото | (за единицу) | 2000 | |
Замер клапанного механизма (Отечественные автомобили) | (за единицу) | 50 | |
Замер клапанного механизма (Иномарка) | 75 | ||
Расточка постели коленвала | |||
Отечественные автомобили | (за единицу) | 6000 | |
Иномарки | (за единицу) | 3000 | |
Ремонт постели распредвала | |||
ГА3-402 мотор | (за цилиндр) | 7000 | |
Иномарка | (за единицу) | 3000 | |
Длина вала более 600 мм | +25% | ||
Ремонт шатунов | |||
Ремонт НГШ | Иномарка | (за шатун) | 2500 |
Ремонт ВГШ (без стоимости материалов) | Иномарка | (за шатун) | 2500 |
Работа по одному шатуну | +20% | ||
Опрессовка | |||
Блок цилиндров | Отечественные автомобили | (за блок) | 2000 |
Иномарки, в том числе V-образные | (за цилиндр) | 900 | |
Головка блока цилиндров | Отечественные автомобили | (за головку) | 1000 |
Иномарки / не параллельные плоскости | (за цилиндр) | 500/650 |
Коленчатый вал | Шлифовка Расточка коленвала
Существует мнение, что нет необходимости шлифовать коленчатый вал, если отсутствует визуальный износ. Заменили вкладыши на новые и поехали дальше. Возможно, и не стоит шлифовать, но перед установкой в двигатель вал необходимо проверить тем более, если мотор разобран.
Изначально проверяем радиальное биение коренных шеек, хвостовика и сальниковой шейки. Первую и последнюю коренную шейку устанавливаем на призмы, а на средней промеряем биение при помощи индикаторной стойки. Аналогичным способом промеряется биение хвостовика и поверхности под сальник. Затем проводим измерение диаметра коренных и шатунных шеек. Измерения каждой шейки выполняем в нескольких плоскостях, т.к. износ может быть в виде эллипса. Особое внимание обращаем на износ поверхности под упорные полукольца (упорный вкладыш). После таких измерений можно точно выяснить степень износа коленчатого вала и принять последующее решение.
Для шлифовки коленчатых валов используются специальные кругло шлифовальные станки. Безусловно точность оборудования влияет на конечный результат, но все же основную роль играет сам шлифовщик. Можем заверить вас что это тонкий процесс, который требует аккуратности и знания от специалиста выполняющего данную операцию.
В первую очередь приступаем к шлифовке шатунных шеек. Все правильно, именно с шатунных т.к. это самое слабое место коленвала. Дело в том, что у коленчатого вала имеется внутреннее напряжение и если шлифовку начать с коренных, а затем приступить к шатунным, то ось коленвала может деформироваться (напряжение в поверхностном слое изменит свое значение). Если это произойдет, то в лучшем случае коренные шайки придется перешлифовывать заново в следующий ремонтный размер иначе вал не будет крутиться в постели.
Коленчатый вал устанавливаем в патроны станка. Смещаем планшайбы таким образом, чтобы ось вращения совпала с осью обрабатываемой шейки. У многих коленчатых валов шейки расположены в одной оси (например, у четырех или шести цилиндрового мотора). Безусловно шлифовку таких валов стоит производить с соблюдением условия совпадения парных осей. В этом случае ход поршня и угол опережения зажигания будет совпадать во всех цилиндрах, а это и есть наивысшее качество ремонта.
Однако на практике не всегда возможно обеспечить условие совпадение парных осей. Это связано со “скручиванием” вала в результате длительной эксплуатации. Шейки вала получают слишком большое смещение.
Во время шлифовки круг подаем с величиной от 0,03 мм до 0,05 мм. Ширина шлифовального круга всегда меньше шейки, поэтому после подачи круг смещаем вдоль ширины всей шейки. Разумеется, следует делать промежуточные остановки и контролировать получающийся размер вала и эллипсность.
Коренные шейки в отличие от шатунных шлифуем в центрах. Разумеется, перед установкой вала следует почистить центровочное отверстие на коленчатом валу, затем вал фиксируем в станке и контролируем биение поверхностей хвостовика, шеек, заднего сальника и приступаем к шлифовке.
Однако после шлифовки микропрофиль поверхности совсем не идеален. Все дело в острых выступах (микронеровностях ) которые способны износить новые вкладыши. Убрать микронеровности после шлифовки поможет без абразивная полировка.
Существует мнение, что шейки вала нельзя шлифовать в ремонтный размер, якобы во время обработки снимается твердый слой металла и шлифованный вал долго не прослужит. Сможем вас смело заверить, что если на вашу модель мотора продаются ремонтные вкладыши, то его можно шлифовать в ремонтный размер. Что касается закалки токами высокой частоты, то как правило глубина упрочненного слоя составляет около 1 мм, а обработка даже под вкладыши 4-го размера (1 мм с диаметра) подразумевает снятие поверхностного слоя в размере 0,5 мм.
Расточка коленчатого вала в Москве. Цена от 2700р.
К одним из распространенных видов ремонта относится расточка коленвала. Она применяется в тех случаях, когда поверхность шеек вала имеет повышенный износ или задиры. При этом нужно отдавать себе отчет, что качественный ремонт, хотя и будет дешевле покупки нового вала, будет стоить уж точно не копейки (хотя и относительно недорого). Поэтому когда речь заходит о таком ремонте, как расточка коленвала, цена на нее в мастерской высоого уровня может быть не такой уж и низкой. Для качественного проведения ремонта требуется не только высокая квалификация персонала, но и высококлассное оборудование, а также возможность проконтролировать результаты ремонта. Коленвал не должен иметь биений, структура металла также не должна быть нарушена.
Не следует считать, что для такой операции как ремонт коленвала, расточка является единственным способом улучшить положение. Это не так. В некоторых случаях, когда, так сказать, требуется «легкий ремонт», можно ограничиться шлифовкой шеек вала. По сравнению с приобретением нового вала такой ремонт обойдется дешево. Но и тут важны возможности ремонтнков по контролю качества. Конечно, в Москве и других крупных городах вероятность найти хорошую автомастерскую выше, чем в провинции, так как серьезные инвестиции не может себе позволить маленькая мастерская — а вот расточка коленвала в Москве большой проблемы не составит, многие автосервис предлагают такие услуги.
Кроме вышеперечисленных операций, иногда возникает необходимость выправления вала, если он приходит некачественным с завода (такое в нашем автопроме не редкость). Обычно после выправления не требуется ни шлифовка, ни расточка, так как дефект тут не в поверхности, а в самой форме вала. Замена переднего сальника коленвала при этом может быть сопутствующей правке — ведь в результате биений этот узел также подвергается нештатным нагрузкам и в результате — разрушению. Те же причины приводят и к тому, что замена заднего сальника коленвала также может оказаться необходима.
Расточка коленвала своими руками
Коленчатый вал — это специальная деталь, выполненная из высокопрочной стали и чугуна. С его помощью создаётся крутящий момент методом передачи усилий от поршней через шатуны. Конструкция данного механизма предусматривает несколько штучных и коренных шеек. Соединяются они щеками, которые создают противовес. В данной статье мы поговорим о том, как расточить коленвал, и зачем необходима эта процедура.
Зачем нужна расточка коленчатого вала
Расточка выполняется в процессе капитального ремонта двигателя. При полной реставрации силового агрегата разбираются абсолютно все узлы, и проводится тщательная проверка всех деталей. Сегменты с выработкой более 50% выбрасываются. Так как их реставрация в большинстве случаем невозможна или слишком затратная. Коленчатый вал — это дорогостоящая деталь. В отличие от большинства узлов, её реставрация обходится значительно дешевле покупки новой.
Расточка коленвала выполняется при обнаружении отклонений в форме, размере или при наличии отложений на поверхности шеек. Из-за высокой нагрузки данного сегмента в конструкции автомобиля, его выработка является неизбежной. Вопрос о целесообразности этой операции возникает в любом случае при обнаружении даже незначительных вышеописанных дефектов, так как от этого зависит качество проведения ремонтных работ в целом. Технические требования к рабочей поверхности очень велики, поэтому данная процедура должна проводиться только при наличии соответствующего инструмента, оборудования и знаний.
Расточка коленвала своими руками
Расточка коленвала представляет собой сложную процедуру, выполнить которую в условиях даже хорошо оборудованного гаража практически невозможно. Так как она требует высокой точности, и может проводиться только на профессиональном токарном оборудовании. К тому же, чтобы получить качественный результат, нужен большой опыт и соответствующая квалификация. Самостоятельно можно выполнить следующие процедуры:
Демонтировать двигатель и все дополнительные навесные узлы, в число которых входит КПП, сцепление и маховик.
Вскрыть поддон силового агрегата, отвинтить крышку коренных и шатунных подшипников. Затем снять её с вкладышем и извлечь коленчатый вал.
Выполнить очистку коленвала. Для этой процедуры можно воспользоваться специальными смесями, их изобилия на рынке позволяет подобрать оптимальную жидкость в любой ценовой категории.
Для выполнения расточки требуется специальное оборудование. Обработка детали начинается с шатунных шеек или из самых изношенных коренных сегментов.
Плюсы от расточки коленвала
В процессе эксплуатации коленчатый вал подвергается большой нагрузке, что приводит к возникновению самых различных дефектов. Постоянное снижение уровня чистоты и образование на поверхности неровностей приводят к ухудшению работоспособности системы. Избавиться от них можно только методом расточки. Помимо того, что вам не придётся покупать полностью новый коленвал, к числу преимуществ данной процедуры входят следующие моменты:
Обеспечивается идеальная чистота рабочих поверхностей. Использование специальных растворов и инструментов позволяет избавить деталь от инородных отложений.
Исправление дефектов (бочкообразности), которые возникают из-за неравномерных усилий при работе механизмов. Это приводит к возникновению зазоров в сопрягающихся деталях.
Устраняется овальность шеек, которая образуется из-за одностороннего усилия от шатуна и является побочным эффектом конструктивной особенности коленвала. Овальность возникает по истечении длительного эксплуатационного периода.
Восстанавливается диаметр шеек. Уменьшение диаметра шеек происходит неравномерно и зависит от режима работы цилиндров.
Как увеличить срок эксплуатации коленчатого вала
Не секрет, что расточка коленвала является дорогостоящей процедурой. Помимо самого рабочего процесса, нужно разбирать силовой агрегат, что также требует немало времени и финансовых затрат при условии обращения в сервис. Самый минимальный срок выполнения данной ремонтной работы выведет из строя автомобиль на несколько дней. В связи с этим советы опытных профессионалов о том, как продлить жизнь коленчатого вала, являются актуальными в любом случае.
Чтобы проводить столько сложные и затратные операции как можно реже нужно соблюдать некоторые правила при эксплуатации машины, так как срок службы коленвала во многом зависит от водителя и его характера езды.
Не допускайте перегревов силового агрегата и не эксплуатируйте машину на повышенных нагрузках.
Своевременно заменяйте расходные материалы: фильтры и моторное масло. Используйте только качественные детали и материалы, рекомендованные производителем.
Любые ремонтные работы, связанные с силовым агрегатом, выполняйте максимально аккуратно с привлечением опытных специалистов, при условии отсутствия личных навыков и знаний.
Регулярно отслеживайте состояние коленчатого вала по давлению в системе смазки и качеству масла.
Шлифовка коленвала в Челябинске
Потребность в этом виде работ возникает, когда износ шеек коленчатого вала (КВ) превышает допустимую норму. Другим поводом служит образование задиров на одной или (значительно реже) нескольких шейках. Подобное происходит в результате проворачивания вкладыша в постели. К задирам может привести и длительное применение крайне некачественного моторного масла или грубое нарушение сроков его замены.
Верным признаком сильного износа шеек является падение давления в масляной магистрали. Если на полностью прогретом двигателе оно не поднимается выше 0,5 кГ/см2, следует задуматься о необходимости ремонта двигателя.
Коленчатый вал
При не слишком серьезных повреждениях разумнее будет выбрать ремонт.
Выбор способа ремонта
Выбор невелик: либо замена КВ на новый, либо шлифовка «родного». Если, конечно, величина износа не превышает допустимую.
Профессионально отшлифованный на хорошем оборудовании КВ почти ничем не уступает заводскому, а стоимость этой операции значительно ниже, нежели цена новой детали. Что касается трудоёмкости работ по замене, она абсолютно одинакова в обоих случаях. Соответственно, одинакова и их стоимость. В силу этого, предпочтя шлифовку приобретению нового вала, вы значительно сэкономите.
Безальтернативная ситуация возникает лишь тогда, когда задиры или износ шеек настолько велики, что не позволяют произвести качественную шлифовку даже под последний ремонтный размер. Замена КВ необходима, также, в случае его серьёзной деформации, что, впрочем, случается весьма редко.
Диагностика состояния
Инструментальная диагностика осуществляется на индикационном стенде, входящим в комплект оборудования нашего технического центра. В отличие от ручных замеров при помощи обычных инструментов, этот метод не только даёт гораздо более точные результаты, но и позволяет определить величину биения. Таким же образом осуществляется проверка результата после шлифовки.
Шлифовка коленвала
Если обработку коренных шеек ещё как-то можно произвести в условиях, близких к «полевым» (на обычном шлифовальном станке деревенской механической мастерской), то шлифовка шатунных требует специального оснащения. Это, отвечающее всем современным требованиям, оборудование имеется в моторном цехе нашего технического центра.
Независимо от состояния каждой из шеек КВ, выбор ремонтного размера осуществляется по наиболее изношенной. В ряде случаев не требуется шлифовка шатунных шеек одновременно с коренными, испытывающими в процессе эксплуатации значительно большие нагрузки. Однако, сделать это, всё-таки, следует, чтобы через полгода-год вновь не оказаться перед проблемой низкого давления масла.
Существует несколько ремонтных размеров, под которые изготавливаются ремонтные вкладыши. У различных производителей моторов они могут различаться, но, достаточно часто устанавливается шаг в 0,25 мм. Последний составляет 1,0 мм. Таким образом, при правильной эксплуатации и своевременном обращении в технический центр можно осуществлять шлифовку КВ до 4х раз.
Расточка и шлифовка коленчатого вала в Челябинске от компании «Железка»
Мы выполняем расточку, шлифование и ремонт коленвалов,
устанавливаемых на любые автомобили.
Прежде чем приступить к выполнению необходимых работ, специалисты нашего центра технического обслуживания проведут оценку объемов и смогут вас сориентировать в том, сколько стоит кап ремонт двигателя именно в вашем случае.
Цены на шлифовку коленвала
Диаметр цилиндра и ход поршня
Диаметр цилиндра и ход поршня | ГленнИсследовательский центр Центр |
На этой странице мы представляем некоторые технические определения, которые используются описать двигатель внутреннего сгорания. На рисунке показана компьютерная анимация одного цилиндра братьев Райт. Авиадвигатель 1903 года.Небольшой раздел коленчатый вал показан красным, поршень и шток показаны серым, а цилиндр, в котором находится поршень, показан синим цветом. Мы сократили цилиндр, чтобы мы могли заметить движение поршня.
Коленчатый вал делает один оборот при движении поршня. сверху цилиндра (внизу слева на рисунке) вниз (вверху справа) и обратно вверх. Поскольку поршень соединен с коленчатым валом, можно отметить движение поршня по углу поворота коленчатого вала.
Нулевые градусы возникают, когда поршень находится в верхней части цилиндра. С тех пор 360 градусов за один оборот, поршень находится внизу, когда угол поворота коленвала составляет 180 градусов. Расстояние, пройденное поршнем от нуля градусов до 180 градусов называется ходом — S поршня. Это объясняет, почему двигатель Райта и современные автомобильные двигатели называют четырехтактные двигатели. Поршень совершает четыре хода, а коленчатый вал делает два оборота между сжигание.2/4
Этот объем называется рабочим объемом , потому что Работа выполняется движущимся газом под давлением, равным давлению газа, умноженному на объем перемещаемого газа. Для своего двигателя 1903 года братья Райт выбрали диаметр цилиндра 4 дюйма и диаметр цилиндра. ход 4 дюйма. Тогда объем рабочей жидкости на один поршень составляет 50,26 куб. дюймы. Братья использовали четыре поршня, так что сумма всех рабочих объем 201 куб. дюйм. Для любого двигателя внутреннего сгорания сумма все рабочие объемы всех цилиндров называется полным рабочим объемом двигателя.
Действия:
Экскурсии
Навигация ..
- Руководство для начинающих Домашняя страница
Провернуть отверстие | Производство режущего инструмента
Существует несколько способов точной обработки отверстия под шатун с несколькими шейками в блоке цилиндров. По словам Маркуса Пола, глобального менеджера по производству отверстий в Kennametal Shared Services GmbH, Фюрт, Германия, лучшим решением с точки зрения надежности и результатов является обычная расточная оправка.Готовое отверстие имеет высокое геометрическое качество, поскольку инструмент опирается на оба конца, но для процесса растачивания требуется специальный станок для подъема блока, чтобы инструмент мог входить и выходить из отверстия, а также входить и выходить из прилавка. -подшипник на приспособлении. Это ограничивает гибкость.
Другой вариант — многолезвийная развертка с направляющими пластинами, которую можно использовать на стандартном обрабатывающем центре, но направляющие пластины развертки постоянно контактируют с заготовкой, поэтому время цикла или процесс обработки увеличивается, а стружка может создавать проблемы с качеством, если они протискиваются между подушечками и заготовкой.«Это не такое надежное решение, как линейно-расточная оправка, — сказал Майкл Хакер, менеджер технической программы Kennametal.
Автопроизводитель BMW поставил перед производителем инструментов задачу разработать инструмент, который подчеркивает преимущества развертывания и растачивания линий, при этом практически устраняя недостатки. По словам Хакера, Kennametal приняла эту задачу и разработала свою расточную оправку с асимметричной линией.
Пауль отметил, что две направляющие пластины асимметричного инструмента расположены так, что они контактируют только с последней цапфой, что позволяет расточной оправке быстро входить и выходить из многоствольного отверстия, не касаясь заготовки.Такая геометрия позволяет подавать пруток через необработанные или незавершенные отверстия по эксцентрической траектории. «Это наша уловка», — сказал он, добавив, что последний журнал действует как опора.
Kennametal сообщил, что расточная оправка с асимметричной линией обеспечивает скорость резания до 100 м / мин. (328,1 sfm) и подача на зуб 0,2 мм / об. (0,008 ipr) при полуобработке и 0,16 мм / об. (0,006 дюйма на дюйм) при чистовой обработке и обеспечивает концентричность 0,005 мм (0,0002 дюйма). Согласно Хакеру, время цикла для расточной оправки с асимметричной линией на 20-40 процентов меньше по сравнению с развертыванием.По сравнению с растачиванием расточной оправки «старого образца» время цикла расточной оправки с асимметричной расточной оправкой на 10% меньше.
Кроме того, инструмент принимает восьмисторонние пластины с четырьмя полуобработанными режущими кромками и четырьмя чистовыми кромками.
Для получения дополнительной информации о Kennametal Inc., Латроб, Пенсильвания, позвоните по телефону (800) 835-3668 или посетите сайт www.kennametal.com.
Как проверить зазоры подшипников
Проверка и регулировка зазоров подшипников — один из наиболее важных аспектов конструкции двигателя.В этом сегменте мы погрузимся в механику измерения вашей кривошипа, шатунов и подшипников.
Простой факт заключается в том, что установка зазора подшипника для высокопроизводительного двигателя — это то, что нельзя сократить. Не существует быстрых и простых способов установить этот критический зазор, независимо от того, является ли двигатель круизным двигателем или беговым животным, которое выдержит сотни миль жестокого обращения.Мы рассмотрим основы измерения зазора подшипника и покажем, как избежать ошибок.Для этого также потребуются некоторые важные измерительные инструменты. Скажем прямо: измерить зазор в подшипнике мощного двигателя невозможно с помощью Plastigage. Эти маленькие кусочки восковой нити не являются прецизионными измерительными приборами и не должны использоваться для определения зазора подшипника. Это может задеть чувства некоторых людей, но установка зазоров подшипников — процесс, который слишком важен, чтобы позволить что-либо, кроме ваших усилий.
Измерение зазора подшипника — один из тех шагов, которые предпринимают все хорошие производители двигателей для создания прочного и надежного основания вращающегося узла.Может быть утомительно пробовать разные ориентиры, чтобы поставить числа там, где вы хотите, но также полезно, когда вы все делаете правильно.Для начала потребуются несколько инструментов и точных измерительных устройств. Это начинается с точного внешнего микрометра в диапазоне журналов, которые вы будете измерять. Существуют дешевые микрометры, которых следует избегать. Настаивайте на использовании микрометра, который будет измерять с точностью до 0,0001 дюйма. Это абсолютная необходимость.
Для измерения внутреннего диаметра коренного или стержневого подшипника потребуется индикатор внутреннего диаметра.Лучшие из них имеют точность до 0,0001 дюйма. С помощью этих двух инструментов вы можете быстро определить зазоры в любом двигателе.
Измерение зазора подшипника имеет смысл только в том случае, если числа точны, поэтому используйте качественные инструменты. Микрометр должен показывать показания с точностью до четвертого знака после запятой, а калибратор с круглой шкалой необходим.Процесс несложный, но требует определенных навыков обращения с микрометром и снятия показаний. Также важно всегда обнулять микрометр перед его использованием.Стандарты обычно поставляются с микрометром вместе с инструментом для точной настройки микрофона. Все стандарты также откалиброваны для использования при 68 градусах F.
Прежде чем мы перейдем к собственно процессу, было бы неплохо поговорить об общих допусках. Общепринятое правило, которое большинство производителей коленчатых валов предпочитают для уличных и высокопроизводительных двигателей, составляет 0,0010 дюйма на каждый 1 дюйм диаметра шейки шейки. Таким образом, для основной шейки малого блока 2,45 дюйма зазор подшипника будет равен 0.0024 дюйма. Для шейки стержня меньшего размера 2,100 дюйма приемлемый зазор будет 0,0021 дюйма. Допустимые заводские допуски на стандартном малоблочном Chevy намного шире, чем это.
Начните с измерения диаметра стержня и коренной шейки коленчатого вала. Это означает использование качественного микрометра, способного измерять до 0,0001 дюйма. Это единственный способ убедиться, что ваши числа будут точными.Начнем с измерения коренной шейки подшипника. Лучше всего измерять цапфу как минимум в двух разных плоскостях, чтобы определить диаметр и округлость.В идеале овальность должна быть равна нулю, но можно увидеть отклонение от 0,0001 дюйма, которое может зависеть или не зависеть от точности измерения. В зависимости от области применения новые спецификации коленчатого вала требуют биения и конуса не более 0,0002 дюйма как для шатунов, так и для сети.
Измерьте шейку коленчатого вала и запишите диаметр всех шейек на листе. Для нового коленчатого вала вы должны обнаружить, что шатуны и сеть, вероятно, будут отличаться не более чем на +/- 0,0001 дюйма. Мы измерили наш коленчатый вал с малым блоком K1, и разница между шейками шатуна была меньше 0.0002 дюйма. Например, большинство наших цапф стержней имели размер 2,09951 дюйма.
После измерения шейки пора установить прибор для измерения внутреннего диаметра стержневых подшипников. Для начала мы установили наш индикатор диаметром чуть более 2100 дюймов, чтобы установить нагрузку на датчик. Затем мы установили наш микрометр на 2,1000 дюйма и поместили его в защищенные тиски, чтобы удерживать его на месте, пока мы устанавливаем циферблатный индикатор на ноль (0) при этой спецификации 2,100 дюйма.
Лучше всего использовать тот же микрометр, который использовался для считывания показаний цапф, чтобы установить нулевой зазор на индикаторе круглого сечения.После этого мы поместили стандартный набор шатунных подшипников в шатун и затянули болты до требуемого значения растяжения шатуна (от 0,0055 до 0,0060 дюйма). После того, как оба болта были вытянуты, мы помещаем стрелочный индикатор в отверстие для измерения вертикального масляного зазора прямо на уровне стержня. Важно всегда измерять масляный зазор в истинно вертикальной плоскости, поскольку все подшипники имеют эксцентриситет, обеспечивающий дополнительный зазор на линии разъема подшипников.Это сделано для компенсации нагрузки, поскольку стороны корпуса подшипника будут защемлены внутрь на линии разъема при высокой нагрузке.
Наше первое измерение с использованием стандартного подшипника для этого приложения показало, что зазор составляет всего 0,0010 дюйма. Мы установили наш циферблатный индикатор на 2,100 дюйма, поэтому, поскольку размер шейки стержня номер один был 2,0994 дюйма, мы добавили 0,0006 дюйма к внутреннему диаметру подшипника, указанному на индикаторе отверстия с круговой шкалой. Это обеспечило истинный зазор подшипника 0,0016 дюйма, что меньше нашего минимального значения 0.0021. Это может быть связано с проблемой накопления допусков, которая является очень распространенной. Вот почему мы измеряем зазор подшипника.
Всегда измеряйте зазор подшипника в вертикальном положении. Все подшипники имеют встроенный эксцентриситет, который создает больший зазор на линии разъема. Рекомендуется измерить этот эксцентриситет примерно на 15-20 градусов от линии разъема, чтобы вы знали, что зазор достаточен, но опубликованный зазор будет по вертикали.К счастью, все производители высокопроизводительных подшипников, такие как Federal-Mogul (Speed-Pro), Mahle-Clevite, King и другие, предлагают вкладыши подшипников в различных размерах больше и меньше, чтобы производитель двигателей мог настроить свои зазоры.В нашем случае Clevite предлагает подшипник 1X, который увеличивает зазор на 0,001 дюйма. Есть несколько методов, которые вы можете использовать, чтобы установить зазоры именно там, где вы хотите.
Например, добавление полного комплекта подшипников 1X теоретически добавит 0,001 дюйма, увеличивая зазор до 0,0026 дюйма. На этом двигателе мы решили установить зазоры в подшипниках шатуна прямо в соответствии со спецификацией шейки 0,001 дюйма на дюйм, что может быть достигнуто путем добавления только одной из двух половин вкладыша подшипника. Это приемлемая процедура, если вы никогда не смешиваете половинки скорлупы более 0.001 дюйм разница. Так, например, никогда не объединяйте половину 1X (+0,001 дюйма) с половиной -1 (0,001 дюйма), потому что толщина корпуса будет несовместимой.
При измерении зазора в коренном подшипнике в двигателях, таких как Chevys с малым и большим блоком, масляный насос установлен на задней главной крышке, всегда устанавливайте или моделируйте напряжение крутящего момента насоса на месте. Эта нагрузка обычно увеличивает зазор, особенно для литых главных крышек на складе. Необязательно монтировать насос целиком, подойдет только крепление.При смешивании половинок гильзы более толстая половина гильзы должна быть помещена в нагруженную сторону отверстия в корпусе. Таким образом, в случае коренного подшипника более толстая половина вкладыша будет помещена в основную крышку, а в шатуне более толстая половина будет помещена в верхнее положение со штоком. Это создает ситуацию, когда под нагрузкой масляный зазор уменьшается на нагруженной стороне, поэтому более тонкая половина кожуха дает больше места для масла, поступающего в зону подшипника и поддерживающего смазку.
Всегда проверяйте зазор на обоих концах широких основных крышек, таких как этот упорный подшипник. Однажды мы измерили большой блок Chevy, у которого была коническая крышка, которая изменила зазор между передней и задней частью почти на 0,001 дюйма!После измерения всех восьми зазоров в подшипниках штока и использования половин корпуса для установки зазоров, очень часто бывает, что разброс зазора между штангами составляет от 0,0004 до 0,0005 дюйма. Допустим, наш самый свободный подшипник стержня имел размер 0,0028 дюйма, а самый плотный стержень — 0 мм.0023 дюйма — расширение 0,0005 дюйма. Мы обнаружили, что переключение самых тугих и слабых опор иногда может сблизить разброс. Для нашего двигателя мы измерили разброс всего 0,0003 дюйма.
Установка зазора подшипника не представляет особой сложности, если вы работаете осторожно и дважды проверяете правильность всех цифр. Но как только вы это сделаете, вы просто убедитесь, что у двигателя есть большие шансы на получение мощности в течение очень долгого времени.
Стальные кривошипы Performance, такие как кривошипы K1, используют большие радиусы галтелей на шейках шатунов, для которых требуются зауженные подшипники.Эти подшипники обычно имеют фаску, которая требует, чтобы подшипник был правильно установлен в штоке, при этом фаска подшипника должна совпадать с фаской на штоке. По этой причине подшипники обычно маркируются как «верхний» и «нижний».Коленчатый вал — x-engineer.org
Коленчатый вал — подвижная часть двигателя внутреннего сгорания (ДВС). Его основная функция — преобразовывать поступательное движение поршня во вращательное движение. Поршни соединены с коленчатым валом через шатуны.Коленчатый вал установлен внутри блока цилиндров.
Изображение: Кривошипный механизм двигателя (источник: Rheinmetall)
- Поршни
- Шатуны
- Маховик
- Коленчатый вал
Поршни, шатуны и коленчатый вал вместе образуют кривошипно-шатунный механизм .
Вторичная функция коленчатого вала заключается в передаче мощности другим системам двигателя:
- фазы газораспределения
- масляный насос
- охлаждающий (водяной) насос
- компрессор кондиционера
- генератор переменного тока и т. Д.
Изображение: Коленчатый вал ДВС с коваными противовесами
Коленчатый вал вставляется в блок двигателя через его основные шейки. Шатуны закреплены на шатунных шейках коленчатого вала. На противоположных сторонах шейки шатуна коленчатый вал имеет противовесы, которые компенсируют внешние моменты, сводят к минимуму внутренние моменты и, таким образом, уменьшают амплитуды вибрации и напряжения в подшипниках. На одном конце коленчатого вала соединен маховик, а на другом конце — зубчатая передача.
Изображение: Описание коленчатого вала двигателя (источник: Rheinmetall)
- Сторона управления или сторона привода
- Противовесы
- Коренная шейка подшипника
- Шатун
- Сторона маховика / передача усилия
- Масляный канал
Количество Цапфы и шатунные шейки зависят от количества цилиндров и типа двигателя (V-образный, прямой и т. д.). Как на главной шейке, так и на шатунных шейках коленчатый вал имеет отверстия для смазки (масляное отверстие), через которые масло течет при работающем двигателе.
Изображение: Коленчатый вал ДВС с привинченными болтами противовесами
Крутящий момент двигателя не является непрерывным, поскольку он создается только тогда, когда каждый поршень находится в цикле расширения. За счет этого на коленчатый вал устанавливается маховик для сглаживания крутящего момента двигателя и уменьшения вибраций.
На V-образном двигателе на одинаковых шатунных шейках установлены два шатуна. Благодаря такому расположению V-образный двигатель с таким же количеством цилиндров более компактен, чем прямой двигатель.Длина двигателя V6 короче, чем длина прямого 6-цилиндрового двигателя (L6).
Изображение: Анимация кривошипного механизма ДВС (щелкните по нему)
Между коленчатым валом и блоком двигателя, на основных шейках, установлены подшипники коленчатого вала. Их роль заключается в уменьшении трения за счет слоя антифрикционного материала, который контактирует с опорами блока цилиндров.
Коленчатый вал выпускается двух типов: литой и кованый . Противовесы можно также наделать непосредственно на коленчатый вал или прикрутить (закрепить болтами с резьбой).
Все поршни двигателя внутреннего сгорания передают свои силы на коленчатый вал. С механической точки зрения коленчатый вал должен выдерживать высокие скручивающие силы, изгибающие усилия, давления и вибрации.
Для любых вопросов или замечаний относительно этого руководства, пожалуйста, используйте форму комментариев ниже.
Не забывайте ставить лайки, делиться и подписываться!
Как измерить зазор в подшипниках двигателя »Блог NAPA Know How
При восстановлении двигателя нет ничего более важного, чем получение правильного зазора в подшипнике.У каждого двигателя свои характеристики зазора в подшипниках, но процедура измерения не меняется. Для проверки зазора подшипника используются два основных метода — Plastigage® или манометры.
Plastigage®
Plastigage® имеет свое место, поскольку служит для поддержки и проверки зазоров в подшипниках. Plastigage® — это специальный пластик, который при сжатии расширяется в определенной степени. Plastigage®, продаваемый в виде гильз с резьбой для определенных диапазонов толщины, действительно хорошо работает в ситуациях, когда компоненты снимаются не полностью, например, при замене подшипников в двигателе и других применениях, не связанных с автомобилем.Plastigage®, впервые поступивший в продажу в 1948 году, является довольно точным и предпочтительным методом для многих энтузиастов DIY.
Plastigage® весьма полезен, поэтому не выбрасывайте его автоматически. Это хороший способ проверить ваши измерения.На самом деле, правильный способ проверить зазоры подшипников — это использовать подходящие инструменты. Чтобы проверить зазоры для стержня и коренных подшипников, вам понадобится набор микрометров и индикатор для измерения внутреннего диаметра. Они легко доступны по бюджетным ценам, но если вы собираетесь использовать их много, рекомендуется использовать инструменты более высокого качества.
Микрометр
Это похоже на подкову с круглой ручкой, прикрепленной к одной ноге. Микрометры обычно регулируются только на 1 дюйм, поэтому для выполнения работы вам потребуется несколько размеров. Набор от 1 до 6 дюймов обычно имеет размеры, необходимые для большинства работ.
Это полный набор микрометров, который подойдет практически для всего, что вам может понадобиться для работы в автомобиле.Циферблатный индикатор
В этом инструменте используется индикатор с круговой шкалой на стойке с небольшим измерительным прибором на колесах. Они регулируются с помощью градуированных удлинителей стоек, которые увеличивают диаметр измерительного круга.
Циферблатный калибр для измерения внутреннего диаметра круглых отверстий, таких как цапфы подшипников. Этот инструмент может измерять отверстия диаметром от 2 до 6 дюймов.Оба инструмента необходимы для проверки внутренних и внешних размеров коленчатого вала, шатунов и шейки блока цилиндров, а также толщины самих подшипников. Сделать все это может быть непросто, поэтому вот несколько советов, которые помогут вам пройти через этот процесс.
Использование микрометра означает выполнение нескольких правил.Ключ к микрометру — не затягивать его слишком сильно. Есть две ручки — большая ручка, а затем меньшая. Меньшая ручка щелкает, когда микрометр находится в контакте с деталью. НЕ используйте ручку большего размера для затягивания микрофона на детали, так как это может повредить инструмент.
Показания микрометра могут сбивать с толку, они градуированы иначе, чем линейки. На внутреннем цилиндре нанесены отметки 0,100 дюйма (большой) и 0,025 дюйма (маленький). Как только вы достигнете этих отметок, шкала на наперстке (большая вращающаяся ручка) вступит в игру для получения конечных размеров.Наперсток имеет шкалу 0,001 деления от 0,000 до 0,025 ”.
Хеш-метки показывают, как вы читаете микрометры. Это требует некоторой практики, и, если вы не будете использовать их ежедневно, со временем вы забудете. Просто будьте терпеливы.Измерение внешнего диаметра
Это довольно просто, просто выберите микрометр, который охватывает необходимый диапазон, и произведите измерение. Рекомендуется проверить деталь в трех разных местах, держась подальше от смазочных отверстий, поскольку они могут нарушить измерения из-за фаски.
Измерительные подшипники
Несмотря на то, что подшипники достаточно плоские, их невозможно точно измерить штангенциркулем, вместо этого вам понадобится микрометр. Существуют специальные микрометры для измерения круглых внутренних поверхностей, но вам не обязательно иметь один из них. Вместо этого вы можете использовать стержень сверла (хорошего качества и использовать гладкую часть, а не рифленую). Поместите сверло на внутреннюю кривую, а затем измерьте подшипник. Вычтите толщину сверла (измерьте, а не предполагайте), и вы получите толщину подшипника.
Трубчатый микрофон полезен для измерения подшипников и деталей, изогнутых внутрь. В крайнем случае вы можете использовать сверло или толкатель и внешний микрофон. Так измеряются подшипники. НЕ ИСПОЛЬЗУЙТЕ штангенциркули, вы можете легко поцарапать баббитовый материал и испортить подшипник, к тому же они недостаточно точны.Использование прибора с круговой шкалой
Для настройки прибора с круговой шкалой необходимо использовать микрометр. Вам нужен базовый размер отверстия, достаточно грубого. Установите калибр чуть больше диаметра, используя правильные удлинители.Установите микрометр на нужный размер отверстия, затем поместите датчик между внутренней частью микрофона и покачивайте датчиком вперед-назад и из стороны в сторону. Отметьте минимальное показание и обнулите манометр до этого показания.
Для настройки индикатора внутреннего диаметра используются как датчик внутреннего диаметра, так и микрометр. Убедитесь, что измерительные концы имеют квадратную форму внутри упоров микрометра (не как показано).Измерения внутреннего диаметра
Установив калибр с круговой шкалой на правильный размер, поместите калибр внутрь цапфы или стержня и покачивайте калибр вперед и назад. и бок о бок, как в процессе установки.Обратите внимание на наименьший диаметр, то есть размер журнала. Как и при внешних измерениях, снимайте показания в трех разных местах. Одно замечание — отверстие должно быть таким, как оно используется, поэтому затяните колпачки до их правильных характеристик, и они должны быть чистыми, без масла вообще.
Поместите калибр внутрь журнала и медленно перемещайте его, пока не найдете наибольшее измерение. Снимите показания в трех местах.Интерпретация чисел
К настоящему времени у вас есть спецификации на шатуны и шатуны коленчатого вала, шейки обоих и спецификации на подшипники.Вычтите спецификацию кривошипа из спецификации шейки, а затем вычтите спецификацию подшипника из этого результата. Эта цифра и есть зазор. Зазор подшипника зависит от двигателя и предполагаемого использования. Стандартные уличные двигатели обычно имеют более узкие зазоры в подшипниках, в то время как двигатели с высокими рабочими характеристиками работают немного свободно. С помощью этих методов вы сможете настроить свой двигатель на нужные характеристики.
Ознакомьтесь со всеми деталями двигателя, доступными на NAPA Online, или доверьтесь одному из наших 17 000 пунктов обслуживания NAPA AutoCare для текущего обслуживания и ремонта.Для получения дополнительной информации о том, как измерить зазор подшипника двигателя, поговорите со знающим экспертом в местном магазине NAPA AUTO PARTS.
Способ и установка для чистовой обработки отверстия под подшипник коленчатого вала
Настоящая заявка испрашивает приоритет заявки на патент Германии № 10 2011 079 900.1, поданной 27 июля 2011 г., которая полностью включена в настоящий документ посредством ссылки.
Изобретение относится к способу чистовой обработки отверстия под подшипник коленчатого вала в картере цилиндра двигателя внутреннего сгорания.Изобретение также относится к установке для механической обработки, пригодной для реализации этого способа.
Картер цилиндра, который часто также называют просто «картером» или «блоком двигателя», является неотъемлемой частью двигателей внутреннего сгорания или двигателей внутреннего сгорания, которые используются, например, в легковых или грузовых автомобилях, самолетах, кораблях. или стационарные установки. Наиболее распространенной является конструкция многоцилиндровых двигателей, поршни которых соединены посредством шатунов с вращающимся коленчатым валом, который передает мощность, вырабатываемую двигателем, на колеса, гребные винты, генераторы и т.п.
Коленчатый вал находится под цилиндрами в рядных или V-образных двигателях и между цилиндрами в двигателях с оппозитными цилиндрами и опирается на картер цилиндра в точках опоры отверстия подшипника коленчатого вала. Опорные точки обычно имеют форму подшипников скольжения, иногда также подшипников качения. Чтобы обеспечить высокую степень соосности коленчатого вала и, следовательно, свести к минимуму нежелательные эффекты износа и вибрации во время работы, коленчатый вал должен соответствовать высоким требованиям допусков на размеры.Точки опоры также имеют жесткие допуски по размеру и положению в картере цилиндра.
Относительно небольшие допуски важных деталей двигателя внутреннего сгорания и картера цилиндра являются результатом сложных функций этих деталей. Таким образом, форма, размер и топография поверхности цилиндра решающим образом определяют степень износа, трение, расход масла и выбросы двигателя внутреннего сгорания, а также, как результат трения, мощность и эффективность.Сжатый объем камеры сгорания в первую очередь определяет степень сжатия двигателя. Это влияет на мощность и, в зависимости от последовательности сгорания, также влияет на уровень выбросов и шум двигателя.
Среди прочего, точное положение коленчатого вала относительно поршней или отверстий цилиндров важно для уменьшения износа деталей двигателя, которые подвергаются высоким нагрузкам. Это, в частности, поршни / поршневые пальцы, шатуны и подшипники шатуна на коленчатом валу, а также крепление коленчатого вала в картере цилиндра.Что касается положения оси отверстия, то здесь играет роль не только абсолютное пространственное положение, но также его угловое положение или ориентация. Например, в случае механических коробок передач со сцеплением коленчатый вал и входной вал трансмиссии вращаются друг с другом. Следовательно, соосность двух валов имеет решающее значение для длительного срока службы.
Что касается крепления коленчатого вала, то также важна соосность точек подшипника относительно друг друга.Точки подшипников должны располагаться на одной линии как можно лучше, чтобы коленчатый вал мог вращаться концентрически и опирался практически равномерно на все точки подшипника.
Область заготовки вокруг отверстия под подшипник коленчатого вала обычно состоит из двух отдельных частей. Чаще всего это несущие перемычки картера цилиндра, с одной стороны, и накрученные на них крышки подшипников, с другой стороны. В качестве альтернативы отверстие под подшипник коленчатого вала может также располагаться на стыке двух половин картера цилиндра, как, например, в случае двигателя с оппозитными цилиндрами.Отдельные детали обычно подвергаются предварительной механической обработке в несобранном состоянии, при этом на опорных перемычках картера цилиндра и на крышках подшипников соответственно образуются полукруглые участки поверхности. На следующем этапе процесса отдельные части привинчиваются друг к другу, так что по существу цилиндрическая часть отверстия соответственно получается из полукруглых частей поверхности в области опорной точки. Ряд участков отверстия, расположенных последовательно друг за другом, образует общий канал подшипника коленчатого вала.
Подготовленное таким образом отверстие затем подвергается многоступенчатой чистовой обработке. Чтобы обеспечить соблюдение допусков при производстве картеров цилиндров, в настоящее время обычно используется комбинация одной или нескольких операций сверления и / или операций трения и одной или нескольких последующих операций хонингования. Обеспечивается множество операций, поскольку неровности, например, вызванные литьем картера цилиндра, требуют удаления относительно большого количества материала, в несколько десятых миллиметра или более, но в то же время размерных и позиционные допуски могут находиться в нижнем микрометровом диапазоне и, следовательно, требовать высокоточной обработки.
Этапы обработки с помощью инструментов с геометрически заданными режущими кромками (сверлильные инструменты или фрикционные инструменты) в этом случае имеют две основные задачи. Одна из задач состоит в том, чтобы установить положение всего отверстия подшипника коленчатого вала относительно системы координат, которая зафиксирована относительно обрабатываемой детали, например относительно соответствующей контрольной поверхности на картере цилиндра. Таким образом, посредством чистовой обработки с геометрически заданными режущими кромками достигается желаемое положение оси отверстия, которое предписано для заготовки.Другой задачей чистовой обработки с помощью инструментов с геометрически заданными режущими кромками является установка отдельных точек опоры относительно друг друга, что среди специалистов в данной области техники также называется «соосностью» отверстия подшипника коленчатого вала. . Общее количество снимаемого материала по отношению к диаметру отверстия в случае этих операций обычно находится в диапазоне нескольких десятых миллиметра, иногда также одного миллиметра или более.
За чистовой обработкой с помощью инструментов с геометрически заданными режущими кромками следует хонингование отверстия подшипника коленчатого вала, то есть чистовая обработка инструментом или несколькими инструментами с геометрически неопределенными режущими кромками.Хонингование, в частности, обеспечивает требуемое окончательное качество в отношении допуска диаметра, цилиндрической формы и шероховатости поверхности, так что допуски в отношении предписываемого желаемого размера и предписываемой желаемой структуры внутренней поверхности отверстия могут быть сохранены.
Предполагается, что положение и соосность отверстия подшипника коленчатого вала не должны изменяться во время хонингования, поскольку они уже были установлены предыдущими операциями. Следовательно, для хонингования предусмотрено шарнирное или податливое соединение между хонинговальным инструментом и хонинговальным шпинделем, чтобы хонинговальный инструмент мог следовать за отверстием, которое уже было предписано относительно его положения, без активного изменения его положения.Количество снимаемого материала по отношению к диаметру отверстия при операции хонингования обычно находится в диапазоне значительно ниже 100 мкм. В ЕР №
0 968 069 В2 описан сверлильный станок, который можно использовать при массовом производстве картеров цилиндров для сверления отверстий подшипников коленчатого вала. В DE 196 34 415 B4 №
раскрыт хонинговальный инструмент, который можно использовать, например, при хонинговании отверстий подшипников коленчатого вала или других отверстий, которые разделены на части и имеют участки отверстия, расположенные последовательно в линию.Хонинговальный инструмент имеет по меньшей мере одну зону хонингования, которую можно настроить в соответствии с желаемым размером перед началом обработки, и имеет зону резания и зону калибровки, каждая с, по меньшей мере, одним режущим покрытием, и направляющую зону резания, по меньшей мере, с одним резанием покрытие, при этом направляющая режущая область расширяется в радиальном направлении.
Изобретение направлено на решение проблемы обеспечения способа чистовой обработки отверстий подшипников коленчатого вала в картерах цилиндров и устройства, подходящего для выполнения этого способа, с помощью которого можно обрабатывать отверстия подшипников коленчатого вала с меньшими затратами, чем ранее, при сохранении самых высоких требований к точность обработки, начиная с относительно грубой предварительной обработки.
В конфигурации согласно заявленному изобретению операции многоступенчатой чистовой обработки могут работать вместе лучше, чем раньше. Оптимизировано взаимодействие между различными методами обработки стружкообразованием — с одной стороны, с геометрически определенной режущей кромкой (например, прецизионное сверление и / или развертывание), с другой стороны, с геометрически неопределенными режущими кромками (хонингование). Следующее — среди соображений, на которых это основано.
Термин «хонингование» в данной заявке относится к процессу обработки с геометрически неопределенными режущими кромками, в котором хонинговальный инструмент с множеством режущих кромок выполняет движение обработки, состоящее из двух компонентов, что приводит к характерной структуре поверхности обработанной внутренней поверхности. , который обычно, но не обязательно, имеет пересекающиеся следы обработки.Механическое движение, передаваемое от хонинговального шпинделя хонинговального станка к хонинговальному инструменту, обычно включает возвратно-поступательное движение, перемещающееся в осевом направлении вперед и назад, и наложенное на него вращательное движение.
По сравнению с инструментами, которые работают с геометрически заданными режущими кромками (например, сверлильные инструменты), хонинговальные инструменты имеют значительно более длительный срок службы, поэтому можно обрабатывать большее количество деталей без смены инструмента. В то время как в случае сверлильных инструментов и инструментов для развальцовки износ режущих кромок с геометрической формой может привести к постепенному изменению условий зацепления и, как следствие, к ухудшению качества поверхности и точности размеров, производительность хонинговального инструмента остается практически постоянной во время работы. весь срок службы за счет эффекта самозатачивания режущих групп, снабженных связанными абразивными зернами, так что в значительной степени постоянное качество формы и микроструктуры поверхности может быть достигнуто даже в случае большого количества обрабатываемых деталей и относительно высокой скорости съема материала на одно отверстие.
Перенос части задачи обработки с прецизионного сверления и / или развертывания на хонингование может, следовательно, повысить производительность всего процесса без потери качества.
Изобретение позволяет значительно сократить технологическую цепочку с возможностью гораздо более рентабельной чистовой обработки.
Обработка с помощью геометрически определенных режущих кромок может работать более приблизительно, но при этом более эффективно, чем раньше.В некоторых случаях можно полностью отказаться от отдельных этапов обработки с помощью геометрически определенных режущих кромок. Например, в случае некоторых вариантов способа можно обойтись без так называемого чистового прецизионного сверления, которое в качестве заключительной операции механической обработки многоступенчатого прецизионного процесса сверления с типичными количествами съема материала 40 мкм и 50 мкм (по отношению к диаметру отверстия) были традиционно разработаны для обработки отверстия с такой точностью, что при последующем хонинговании требовалось удалить только очень небольшие количества (обычно от 40 мкм до 60 мкм), чтобы установить допуск диаметра, цилиндрический форма и структура поверхности.
Поскольку при хонинговании можно добиться относительно большого съема материала, менее важно, чем в случае традиционных методов, поддерживать определенный конечный размер в пределах жестких допусков за счет обработки с помощью геометрически определенных режущих кромок. Последующая операция хонингования в этом отношении «более терпима». Таким образом, отпадает необходимость в измерении, обычном для обычных методов, после завершения окончательной чистовой обработки с помощью геометрически определенных режущих кромок или перед началом хонингования, а после окончательной чистовой обработки заготовку можно отшлифовать. работа с геометрически определенной режущей кромкой без предварительного измерения.Также можно обойтись без соответствующей измерительной станции, и, соответственно, она отсутствует в предпочтительных вариантах выполнения обрабатывающих установок, так что в этих вариантах реализации никакая отдельная измерительная станция не расположена в потоке деталей между станком для обработки с геометрически заданным режущая кромка и хонинговальный станок.
В случае заявленного изобретения не только производственный процесс «хонингования» используется для задания допуска диаметра, цилиндрической формы и структуры поверхности, но в то же время хонингование может привести к улучшению соосности отверстия. везде, где требуется.Этому способствует, с одной стороны, перемещение хонинговального инструмента вперед и назад соосно оси отверстия и, с другой стороны, относительно высокий объем съема материала по сравнению с традиционными методами.
Заготовка обычно удерживается в положении заготовки, и хонинговальный инструмент вводится в отверстие соосно по отношению к желаемому положению оси отверстия и перемещается внутри отверстия. Заготовка обычно защищена, по крайней мере, от ее снятия с держателя заготовки.В случае некоторых вариантов способа могут быть разрешены степени свободы движения вокруг вертикальной оси, чтобы не возникали нежелательные сдерживающие силы и выравнивать заготовку на хонинговальном инструменте. В других вариантах заготовка фиксируется для хонингования в положении заготовки, например, с помощью индексирующих устройств, и, таким образом, имеет положение заготовки, которое не изменяется даже под действием сил обработки.
Для того, чтобы положение оси отверстия не было изменено хонингованием, когда оно уже было правильно установлено предыдущими операциями, и для того, чтобы, возможно, даже из-за удаления материала, который неравномерно распределен в осевом направлении и / или в в направлении по окружности положение все еще может быть скорректировано, и, в частности, соосность может быть дополнительно улучшена, в некоторых вариантах осуществления обеспечивается точное фиксирование положения оси инструмента (относительно пространственного положения и углового положения или ориентации) во время хонингование.Это может быть достигнуто радиальным направлением хонинговального инструмента. Конструктивно это может быть достигнуто с помощью различных радиальных направляющих устройств.
Хонинговальный инструмент предпочтительно жестко соединен посредством соединительной конструкции со стороны шпинделя с хонинговальным шпинделем или с приводной штангой, которая жестко соединена с хонинговальным шпинделем и направляется по крайней мере одной точкой подшипника, расположенной на осевом расстоянии от соединительная конструкция, по меньшей мере, одна режущая группа хонинговального инструмента расположена между соединительной конструкцией и точкой опоры.Следовательно, радиальные силы, действующие на эту режущую группу, могут восприниматься с обеих сторон режущей группы, в результате чего положение оси инструмента в области режущей группы остается стабильным даже при высоких поперечных силах. В частности, в случае продольных в осевом направлении отверстий, например, с отношением длины к диаметру более 3 или более 4, или более 5 или более 6, этот тип жесткого направления осевого движения оказался успешным.
В некоторых вариантах осуществления концевая часть хонинговального инструмента, удаленная от шпинделя, установлена с возможностью вращения на выходной стороне, удаленной от входной стороны отверстия, в контродержателе.Этот вариант возможен для всех заготовок со сплошным отверстием. Контродержатель может перемещаться вместе с хонинговальным инструментом при наличии осевого возвратно-поступательного движения хонинговального инструмента, а именно пассивно (без собственного привода перемещения) или активно (посредством привода перемещения). В случае контрдержателя, который перемещается вместе с инструментом, длина зажима хонинговального инструмента между соединительной структурой со стороны шпинделя и контрдержателем остается постоянной во время возвратно-поступательного движения, что может иметь положительное влияние на качество обработки.Также возможно, что контрдержатель закреплен в положении, фиксированном по отношению к станку, так что хонинговальный инструмент перемещается относительно контрдержателя во время возвратно-поступательных движений. Такие варианты конструктивно особенно просты, так как можно отказаться от линейных направляющих и, возможно, привода контрдержателя.
Возможны также варианты с направляющими точками впереди и сзади отверстия (передние и задние направляющие) и / или варианты с внутренними направляющими.
Отверстие подшипника коленчатого вала является примером отверстия, которое относительно длинное в осевом направлении и имеет ряд участков отверстия, расположенных на одной линии друг с другом и последовательно на расстоянии друг от друга. В случае таких заготовок возможно, чтобы по меньшей мере одна опора для хонинговального инструмента находилась между двумя соседними участками отверстия. В некоторых вариантах осуществления такая «внутренняя направляющая», то есть устройство для направления инструмента внутри заготовки, обеспечивается между двумя соседними частями отверстия и, следовательно, между входом в канал и выходом из канала.Таким образом, осевое расстояние между точками опоры для хонинговального инструмента может быть коротким, за счет чего может быть достигнута установка или направление, которые особенно стабильны по отношению к поперечным силам, и изгиб хонинговального инструмента между точками опоры может быть предотвращен или уменьшен.
В случае варианта, который подходит для внутренней направляющей, крепление инструмента, которое служит направляющим устройством, имеет несущий элемент, который может быть закреплен по отношению к машине, и на котором или в котором направляющий элемент, который свободно вращается с По отношению к этому несущий элемент установлен с возможностью вращения, во время работы вращается вместе с проходным, вращающимся хонинговальным инструментом и направляющими и поддерживает последний против радиальных сил.Поворотный направляющий элемент может иметь по меньшей мере один приводной элемент, который предназначен для (блокирования по окружности) зацепления в выемке, предусмотренной на корпусе инструмента хонинговального инструмента, так что направляющий элемент может иметь простую и прочную форму, как пассивный элемент (без собственного привода). На внутренней окружности направляющего элемента могут быть предусмотрены непрерывные в осевом направлении зазоры, через которые режущие элементы (например, хонинговальные стержни), прикрепленные к хонинговальному инструменту, могут проходить без какого-либо физического контакта.
Внутренняя направляющая также может быть рекомендована в сочетании с групповым инструментом, в случае которого несколько режущих групп, расположенных на осевом расстоянии друг от друга, расположены на корпусе инструмента для одновременного хонингования нескольких участков отверстия. расположены на осевом расстоянии друг от друга, причем количество режущих групп предпочтительно соответствует количеству участков отверстия, которые должны обрабатываться одновременно. Например, групповой инструмент для четырехцилиндрового рядного блока цилиндров может иметь пять режущих групп для пяти точек опоры.Тогда внутреннее крепление инструмента может воздействовать на корпус инструмента между двумя режущими группами. Могут быть предусмотрены две или более внутренних опоры инструмента, например, по одной на каждое промежуточное пространство между режущими группами.
В качестве альтернативы радиальному ведению хонинговального инструмента с помощью внешних радиальных направляющих устройств в некоторых случаях может быть также достаточно жестко соединить хонинговальный инструмент с хонинговальным шпинделем или соответственно жестким приводным стержнем и достаточно жестко спроектировать всю конструкцию что, самое большее, может быть очень небольшое боковое отклонение.
Что касается методов хонингования, различают классическое хонингование и так называемое хонингование на оправке. При классическом хонинговании используются хонинговальные инструменты с режущими группами, которые можно регулировать в радиальном направлении во время хонингования, чтобы постепенно получить желаемый размер отверстия, который требуется, с помощью большого количества ходов. С другой стороны, при хонинговании на оправке используется инструмент для хонингования оправки, предварительно установленный на желаемый размер (конечный размер), обычно имеющий коническую зону резания и, примыкающую к ней, цилиндрическую калибровочную зону, которая также выполняет резку.В случае хонингования оправки вся операция удаления материала обычно требует всего одного или нескольких двойных ходов, например максимум трех. Оба метода хонингования могут использоваться в рамках настоящего изобретения, альтернативно или в комбинации.
Характерной чертой хонингования является большой съем материала по сравнению с обычным хонингованием, что, возможно, также позволяет скорректировать или улучшить соосность. Удаление материала, фактически необходимого для участков расточки отверстия подшипника коленчатого вала, зависит от подготовки и может варьироваться от участка отверстия к участку отверстия детали и от детали к детали серии.Часто производится удаление по меньшей мере 100 мкм, по меньшей мере, на одном или нескольких участках отверстия и / или заготовках в серии, также возможно, в частности, чтобы количество удаляемого материала составляло от 200 мкм до 500 мкм. В случае заготовок или частей заготовок, которые были особенно хорошо подготовлены с помощью геометрически определенных режущих кромок, количество снимаемого материала также может быть менее 200 мкм или менее 100 мкм.
Чтобы сделать экономичную чистовую обработку за короткое время цикла, в случае некоторых вариантов метода, материал удаляется во время мощного хонингования, по крайней мере, поэтапно, с помощью геометрически неопределенных режущих кромок с материалом. скорость съема Q W = V / t, что намного больше, чем при обычном хонинговании.Здесь V — это объем заготовки, отрезанной при механической обработке, а t — необходимое для этого время обработки, в результате чего размер [ 3 / с] является размером. Объем V определяется приближением V≈ (π (D 2 −d 2 ) L) / 4, где d — (меньший) диаметр отверстия перед удалением, D — (больший) диаметр после удаления, а L — длина обработанного отверстия или участка отверстия, диаметр которого был увеличен.
Чтобы числовые значения были сопоставимы, в этом приложении скорость съема материала относится к времени обработки t = 20 с (соответствует типичному времени хонингования) и длине L = 20 мм (соответствует типичной ширине перемычки одноподшипниковая перемычка расточки под подшипник коленчатого вала двигателя легкового автомобиля).Нормализованная таким образом скорость съема материала в данной заявке называется «удельной» скоростью съема материала и для краткости Q W S .
Если теперь рассматривать типовые отверстия с номинальным диаметром от 40 мм до 70 мм, удельная скорость съема материала предпочтительно составляет более 13 мм 3 / с (для 40 мм) и более 22 мм 3 / с (для 70 мм). Эти типичные нижние пределы обычно намного превышаются. В случае номинального диаметра 40 мм может быть, например, что Q W S > 30 мм 3 / с, иногда также Q W S > 50 мм 3 / с или даже Q W S > 100 мм 3 / с.В случае номинального диаметра 70 мм может быть, например, что Q W S > 50 мм 3 / с, иногда также Q W S > 100 мм 3 / с или даже Q W S > 150 мм 3 / с.
Среди факторов, способствующих высокой производительности съема материала, есть необычно высокие скорости резания, которые, в свою очередь, зависят от скорости вращения (количества оборотов) и / или скорости возвратно-поступательного движения хонинговального инструмента.
В случае некоторых вариантов способа хонинговальный инструмент вращают во время хонингования с большой мощностью, по меньшей мере, поэтапно, с числом оборотов более 400 об / мин, причем число оборотов предпочтительно, по крайней мере, поэтапно, более 1000 об / мин, в частности более 1500 об / мин. Часто количество оборотов лежит в диапазоне от 1500 до 2500 об / мин.
В качестве альтернативы или в дополнение, хонинговальный инструмент может в случае классического хонингования (с расширяемым хонинговальным инструментом) перемещаться во время мощного хонингования, по крайней мере, поэтапно, с максимальной возвратно-поступательной скоростью более 20 м / мин. максимальная скорость возвратно-поступательного движения предпочтительно лежит, по крайней мере, по фазам, между 30 м / мин и 50 м / мин или даже более 50 м / мин.В случае хонингования оправки (с помощью предварительно настроенного инструмента) может быть достигнута максимальная скорость возвратно-поступательного движения более 12 м / мин, в частности более 20 м / мин.
Привод шпинделя хонинговального станка соответственно рассчитывается с учетом максимального числа оборотов, максимальной скорости возвратно-поступательного движения и мощности привода.
Специальная конструкция режущего средства может помочь достичь высоких скоростей съема материала и других критериев обработки. Например, может оказаться целесообразным использовать относительно длинные режущие палки.В некоторых вариантах осуществления используется хонинговальный инструмент, который имеет несколько режущих стержней, распределенных вокруг корпуса инструмента, причем длина режущих стержней составляет более 60%, в частности более 80% длины осевого отверстия. В качестве альтернативы или в дополнение, длина режущих стержней может превышать эффективный диаметр хонинговального инструмента в три, четыре или пять раз. Для обработки типичных отверстий подшипников коленчатого вала, например, диаметром в диапазоне от 40 мм до 70 мм, длина режущего стержня может составлять, например, 200 мм или более, например, между 300 мм и 400 мм.При использовании относительно длинных режущих стержней можно одновременно обрабатывать большие участки отверстия при использовании хонинговальных инструментов с радиально регулируемыми режущими стержнями. При использовании конических режущих стержней (хонингование на оправке) можно добиться значительного изменения диаметра за один рабочий ход. Относительно длинные режущие стержни обычно также благоприятны с точки зрения прямолинейности производимого отверстия.
При хонинговании используются предпочтительно относительно крупнозернистые режущие средства, в частности, с очень твердыми режущими зернами, например, с алмазными режущими зернами.Часто средний размер зерна в диапазоне от примерно 50 мкм до примерно 150 мкм (в случае алмазных стержней, например, от D54 до D151) будет выгодным для достижения хорошего компромисса между высокой скоростью удаления и в то же время достаточно мелкая структура обработанных внутренних поверхностей после завершения хонингования.
Хонингование предпочтительно проводить в одну стадию. Таким образом, в технологической цепочке выполняется только одна операция хонингования, завершающая чистовую обработку.Это позволяет сократить общее время обработки. Хотя многоступенчатое хонингование возможно, обычно оно не требуется.
Заключительная операция чистовой обработки, которая непосредственно предшествует операции хонингования и при которой используется инструмент с одной или несколькими геометрически заданными режущими кромками, может принимать различные формы в зависимости от процесса в целом и от заготовки.
В некоторых вариантах способа развёртывание с помощью инструмента для развёртывания выполняется как заключительная чистовая операция с геометрически заданной режущей кромкой.Термин «развертывание» относится здесь к способу чистовой обработки стружкообразованием, при котором существующее отверстие, имеющее так называемый припуск на расширение, высверливается с помощью инструмента для развертывания. Припуск на развертывание обычно рассчитывается таким образом, чтобы, с одной стороны, была минимальная толщина стружки, но, с другой стороны, не было чрезмерного удаления стружки, которое могло бы привести к перегрузке инструмента для развертывания и / или заготовки. . Поскольку при развёртывании выполняется только один проход для удаления стружки, припуск на развёртывание соответствует толщине стружки или глубине резания.Обычно он относительно невелик и, например, в случае вариантов способа может, например, составлять от 0,4 мм до 0,8 мм, в зависимости от материала и диаметра отверстия. В отдельных случаях количество удаляемого материала также может быть меньше, например всего 0,2 мм или более.
Операция развертывания также отличается тем, что инструмент для развертывания направляется точно в уже обработанное отверстие. Для этого на расширителе предусмотрены один или несколько направляющих элементов или направляющих частей.Инструмент для развёртывания может быть сконфигурирован как однолезвийный инструмент для развёртывания, только с одной геометрически заданной режущей кромкой, или как многогранный инструмент для развёртывания, с двумя или более геометрически заданными режущими кромками.
Особенно предпочтительными обычно являются инструменты для развертывания, на которых предусмотрены различные элементы для удаления материала, то есть для функции механической обработки, и для функции направления в отверстии. Например, в дополнение к одной или нескольким режущим кромкам инструмента могут быть предусмотрены одна или несколько не режущих направляющих полос.Такое разделение между задачами обработки и направлением позволяет легко заменять режущие кромки этих инструментов и / или точно настраивать их по мере необходимости.
В качестве альтернативы операции развертывания, операция точного сверления с помощью инструмента для точного сверления может быть предусмотрена как окончательная операция чистовой обработки с геометрически заданной режущей кромкой. Величина снятия материала в этом случае предпочтительно равна величине снятия материала при обычных операциях получистовой обработки, то есть, например, примерно между 0.4 мм и около 0,5 мм. В отдельных случаях количество удаляемого материала также может быть меньше, например всего 0,2 мм или более в диаметре.
Заключительная операция чистовой обработки с геометрически определенной режущей кромкой может быть выполнена как односторонняя обработка, при которой обрабатывающий инструмент вводится только с одной стороны обрабатываемого отверстия подшипника коленчатого вала.
В случае других вариантов метода, с другой стороны, окончательная чистовая операция с геометрически заданной режущей кромкой выполняется как двусторонняя обработка, короткий инструмент, длина обработки которого короче длины отверстия под подшипник коленчатого вала, вводимого с каждого конца отверстия под подшипник коленчатого вала.Короткий инструмент, как правило, жестко соединен с обрабатывающим шпинделем связанного с ним станка и, в результате его небольшого выступа, очень устойчив по отношению к поперечным силам, действующим поперек оси вращения из-за его компактной длины, и поэтому никакого внешнего руководства не требуется.
Короткий инструмент предпочтительно имеет длину обработки, которая составляет от 50% до 80% длины отверстия подшипника коленчатого вала. Как правило, не все части отверстия обрабатываются коротким инструментом, но, по меньшей мере, половина частей отверстия.Например, в случае блока цилиндров с четырьмя цилиндрами с пятью перемычками подшипника или участками отверстий только три из пяти или четыре из пяти перемычек подшипника могут быть обработаны в каждом случае. В случае блока цилиндров для трехцилиндрового двигателя, например, две или три из четырех перемычек подшипника могут быть обработаны во время обработки с помощью короткого инструмента, вводимого с одной стороны.
Когда короткий инструмент зажимается точно соосно по отношению к обрабатывающему шпинделю и ось вращения обрабатывающего шпинделя лежит соосно по отношению к желаемому положению оси отверстия, то, по крайней мере, концевые перемычки лежат на соответствующих входных отверстиях. обычно производятся с точным положением, лежащим в пределах допусков, путем двусторонней обработки.Отклонения от точного положения отверстия, выходящего за пределы допусков, могут возникать, если вообще возникают, в случае участков отверстия, которые лежат дальше внутрь. Хотя эти отклонения способствуют ухудшению соосности, их можно надежно исправить с помощью последующей операции хонингования.
Двусторонняя обработка может выполняться различными способами. Например, можно снабдить два станка обращенными друг к другу обрабатывающими шпинделями, оси вращения которых проходят соосно.Отверстие подшипника коленчатого вала детали, расположенной между обрабатывающими шпинделями, может затем обрабатываться одновременно с обеих сторон.
В случае других вариантов, которые могут быть выгодными по причинам, в том числе по стоимости, при двусторонней обработке детали она поворачивается на 180 ° между первой обработкой (от первого конца отверстия) и второй обработкой. (с противоположного, второго конца канала ствола). В этом случае достаточно одного обрабатывающего шпинделя, расположенного с одной стороны, при этом две операции обработки выполняются на заготовке одна за другой.
В некоторых вариантах способа двусторонняя обработка выполняется как прецизионное сверление, а в качестве короткого инструмента используется прецизионный сверлильный инструмент.
В случае других вариантов способа двусторонняя обработка спроектирована как операция развёртывания, при этом инструмент для развёртывания используется как короткий инструмент.
Поскольку, по крайней мере, положения концевых перемычек, лежащих на отверстии, обычно могут быть определены точно в пределах допусков в случае двусторонней механической обработки, в частности, в случае этого варианта способа положение отверстия подшипника коленчатого вала может быть обеспечено чистовой операцией с геометрически определенной режущей кромкой.Последующее хонингование в этом случае не должно быть предназначено для изменения положения или коррекции положения, но может быть оптимизировано для улучшения соосности участка отверстия и поддержания допусков на диаметр и качества поверхности.
В качестве альтернативы двухсторонней обработке в некоторых вариантах метода предусмотрено, что окончательная чистовая операция с геометрически заданной режущей кромкой выполняется с помощью группового инструмента, на котором выполняется несколько операций резания. группы, расположенные на осевом расстоянии друг от друга, расположены на корпусе инструмента для одновременной обработки ряда участков отверстия подшипника коленчатого вала, которые расположены на осевом расстоянии друг от друга.Обычно количество режущих групп в этом случае соответствует количеству участков отверстия, которые должны обрабатываться одновременно.
Каждая режущая группа может иметь одну или несколько геометрически определенных режущих кромок. Могут быть предусмотрены фиксированные и / или регулируемые и / или регулируемые режущие кромки.
Поскольку, чтобы соответствовать относительно большой длине отверстия подшипника коленчатого вала, групповой инструмент имеет относительно большую длину инструмента по отношению к его диаметру, существует риск бокового отклонения группового инструмента.Таким образом, в случае предпочтительных вариантов осуществления предусмотрено, что концевая часть группового инструмента, удаленная от шпинделя, закреплена с возможностью вращения в контрдержателе на выходной стороне, удаленной от входной стороны отверстия подшипника коленчатого вала, контр-держателе. держатель предпочтительно перемещается вместе с групповым инструментом, когда происходит осевое возвратно-поступательное движение группового инструмента.
В частности, при использовании группового инструмента, установленного напротив друг друга, можно использовать чистовую обработку с помощью геометрически определенных режущих кромок, возможно, за одну операцию механической обработки, чтобы обработать подготовленное отверстие подшипника коленчатого вала до такой степени, чтобы, с одной стороны, , обычно необходимое выравнивание после сборки детали и, с другой стороны, чистовая обработка до припуска, подходящего для хонинговального удаления, может выполняться за одну операцию обработки.
Чтобы гарантировать, что после обработки групповым инструментом после завершения прецизионного сверления каждая из частей отверстия имеет заниженный размер, который может быть надежно удален последующей операцией хонингования, при использовании группового инструмента предпочтительно имеется после операции измерения, в которой каждая часть отверстия проверяется отдельно для поддержания начальных параметров, применимых к последующей операции хонингования (в частности, диаметра). Таким образом можно избежать ситуации, в которой, например, при разрыве инструмента в одной из режущих групп остается участок отверстия слишком малого диаметра, что может привести к хонинговальному инструменту и / или заготовка повреждается при вводе хонинговального инструмента.Достаточно простой проверки того, что он просверлен.
Изобретение также относится к обрабатывающей установке, пригодной для реализации способа чистовой обработки отверстия под подшипник коленчатого вала в картере цилиндра двигателя внутреннего сгорания, по меньшей мере, одним станком с обрабатывающим шпинделем, на котором выполняется чистовая обработка. инструмент с геометрически определенной режущей кромкой соединен или может быть соединен, а также с хонинговальным станком с хонинговальным шпинделем, который может приводиться в движение от привода шпинделя и к которому хонинговальный инструмент присоединен или может быть соединен.Установка для механической обработки сконфигурирована для выполнения метода, описанного в этой заявке.
Хонинговальный инструмент предпочтительно соединен или может быть жестко соединен с хонинговальным шпинделем напрямую или путем размещения жесткого приводного стержня, а подшипниковое устройство предназначено для воздействия на хонинговальный инструмент в точке опоры, расположенной на осевом расстоянии от шпинделя. боковая соединительная конструкция хонинговального инструмента таким образом, что по меньшей мере одна режущая группа или часть режущей группы хонинговального инструмента расположена между соединительной структурой и точкой опоры.Может быть предусмотрена передняя направляющая, и / или задняя, и / или внутренняя направляющая.
Этот метод также может быть выполнен на обрабатывающем центре соответствующей конструкции.
Вышеупомянутые и другие признаки вытекают не только из формулы изобретения, но также из описания и чертежей, где отдельные признаки могут быть реализованы в каждом случае сами по себе или как множество в форме подкомбинаций в варианте осуществления изобретения и в других областях и составляют выгодные варианты осуществления.Формулировки всех пунктов формулы изобретения вносятся в содержание описания путем ссылки. Предпочтительные варианты осуществления поясняются на основе прилагаемых чертежей.
РИС. 1 изображает схематический вид сверху части варианта выполнения установки для механической обработки для чистовой обработки отверстий под подшипники коленчатого вала в картерах цилиндров двигателей внутреннего сгорания;
РИС. 2А — схематический вид сбоку горизонтального хонинговального станка для хонингования отверстий подшипников коленчатого вала;
РИС.2B-2D — различные виды блока цилиндров двигателя с отверстием для подшипника коленчатого вала;
РИС. 3 — схематический вид сбоку обработки отверстия подшипника коленчатого вала с помощью хонинговального инструмента для оправки, установленного в противоположную сторону на конце и имеющего коническую режущую область;
РИС. 4 — схематический вид сбоку устройства с хонинговальным инструментом, установленным в передней направляющей и задней направляющей и прикрепленным к хонинговальному шпинделю с помощью приводного стержня;
РИС. 5A и 5B — схематический вид сбоку и сверху устройства с хонинговальным инструментом, который жестко соединен непосредственно с хонинговальным шпинделем, снабжен непрерывными режущими стержнями и установлен с возможностью вращения внутри заготовки между соседними несущими пластинами с помощью внутренней направляющей. ; и
фиг.6 показан пример двустороннего прецизионного сверления непосредственно перед операцией хонингования.
На фиг. 1 показан схематический вид сверху части варианта выполнения установки для механической обработки 100 для чистовой обработки отверстий под подшипники коленчатого вала в картерах цилиндров двигателей внутреннего сгорания. Вся установка для механической обработки, только часть которой здесь представлена, предназначена для полной чистовой обработки отверстия под подшипник коленчатого вала непосредственно после сборки отдельных частей блока цилиндров, образующих отверстие под подшипник коленчатого вала.
В данном примере обрабатываемая деталь 150 представляет собой картер цилиндра для рядного четырехцилиндрового двигателя. На показанной детали производственной линии для полной обработки этих деталей показан станок, сконструированный как прецизионный сверлильный станок, с устройством для прецизионного сверления 120 и хонинговальный станок, следующий в направлении потока материала 182 , с хонинговальное устройство 140 . Устройство для точного сверления , 120 и устройство для хонингования , 140, размещены здесь на отдельных станинах станка, но они также могут быть размещены на общей станине станка.Передаточное устройство 180 служит для перемещения заготовок в направлении движения материала 182 .
Устройство прецизионного сверления 120 содержит шпиндель прецизионного сверления 122 , ось шпинделя с жесткой направляемостью которого выровнена по существу горизонтально. Шпиндель прецизионного сверления может перемещаться горизонтально и вращаться вокруг оси шпинделя с помощью привода шпинделя 124 . К свободному концу шпинделя для точного сверления жестко прикреплен инструмент для точного сверления 128 , по окружности которого прикреплена режущая пластина 129 , состоящая из твердого металла, которая служит наконечником сверла или режущей кромкой.
Осевое перемещение и вращательное движение шпинделя точного сверления, а также регулировка режущей кромки контролируются с помощью блока управления точным сверлением 126 . В типичных операциях точного бурения работа выполняется с числом оборотов от примерно 1000 до примерно 3000 об / мин и скоростью продвижения от примерно 200 до примерно 1400 м / мин. Типичная глубина резания (снятие материала) по отношению к диаметру обычно составляет от 0,3 мм до 1 мм.В исключительных случаях возможны отклонения от этих типовых диапазонов параметров.
С помощью регулировочного устройства можно отрегулировать радиальное положение режущей кромки, и тем самым можно, среди прочего, зафиксировать диаметр отверстия, которое требуется прецизионно просверлить. Таким образом, инструмент для точного сверления имеет одну или несколько регулируемых режущих кромок. Регулирующее устройство может, например, иметь конус, который расположен внутри прецизионного сверлильного инструмента и может перемещаться в осевом направлении с помощью регулировочного стержня, направляемого шпинделем прецизионного сверления , 122, .Наклонная боковая поверхность конуса воздействует на наклонные внутренние стороны держателей инструмента, которые радиально перемещаются в корпусе прецизионного сверлильного инструмента и, соответственно, несут сменную режущую пластину. Благодаря такой компоновке радиальное положение режущей кромки 129 , а вместе с ним и эффективный диаметр прецизионного сверлильного инструмента, можно изменять непрерывно или поэтапно во время работы устройства прецизионного сверления в качестве реакции на управляющие сигналы станка для точного сверления. Блок управления точным сверлением 126 .При износе инструмента режущую пластину можно отрегулировать заново, чтобы не было значительного ухудшения качества отверстия, в частности диаметра отверстия, несмотря на износ инструмента (компенсация износа).
Шпиндель прецизионного сверления блока прецизионного сверления 120 и закрепленный на нем инструмент прецизионного сверления предназначены для выполнения получистовой обработки с определением положения и угла. Типичное количество снимаемого материала превышает 0,4 мм (относительно диаметра).В отдельных случаях возможно также удаление меньшего количества материала, например от 0,2 мм. Показанное устройство для точного сверления является последней станцией для точного сверления в технологической цепочке непосредственно перед передачей заготовок на хонинговальное устройство 140 . Следовательно, окончательная обработка стружкообразованием с геометрически определенной режущей кромкой выполняется на устройстве для точного сверления 120 .
В потоке деталей перед этим устройством для точного сверления имеется только один дополнительный блок для точного сверления, то есть блок для грубого сверления (не показан), который предназначен для грубой обработки (типичное количество съема материала составляет от 2 мм). и 8 мм).Процесс может быть спроектирован таким образом, что после завершения окончательного прецизионного сверления отверстие имеет меньший размер в диапазоне 100-400 мкм, предпочтительно в диапазоне 0,2 мм +/- 0,05 мм в диаметре.
Одношпиндельное хонинговальное устройство 140 имеет хонинговальный блок 141 . Он имеет горизонтальный хонинговальный шпиндель 142 , который приводится в движение с помощью привода шпинделя 144 , так что во время хонингования хонинговальный шпиндель совершает горизонтально колеблющиеся рабочие движения, на которых совершается вращательное движение вокруг горизонтальной оси вращения. накладывается.Блок управления хонингом 146 управляет рабочими движениями хонинговального шпинделя.
Жестко соединенный со свободным концом хонинговального шпинделя 142 хонинговальный инструмент 148 , с помощью которого операция хонингования на прецизионно просверленном отверстии подшипника коленчатого вала может быть выполнена сразу после окончательной операции прецизионного сверления после переноса. заготовки от устройства для точного сверления до хонинговального устройства.
При таком хонинговании после переноса достигается относительно высокий съем материала.Что касается диаметра отверстия, в типичных процессах удаляется припуск не менее 80 мкм, при этом при хонинговании удаляется припуск, который часто превышает 100 мкм. Во многих случаях припуск, удаляемый хонингованием, составляет от примерно 80 мкм до примерно 110 мкм, возможно, также до 200 мкм, редко больше.
Между заключительным этапом обработки с геометрически заданными режущими кромками и началом хонингования не выполняется шаг измерения, заготовка передается непосредственно на хонинговальный станок.
Далее сначала описываются различные примеры конструктивных и связанных с методами вариантов хонингования.
На фиг. 2А показан схематический вид сбоку варианта осуществления горизонтального хонинговального станка 200 , который может использоваться в механической установке для хонингования отверстий подшипников коленчатого вала.
Хонинговальный станок спроектирован таким образом, что с помощью производственного процесса хонингования могут быть выполнены допуски по диаметру, цилиндрической форме и структуре поверхности точек опоры.Кроме того, если и когда требуется, соосность частей отверстия, которые совпадают друг с другом, может быть улучшена.
Установленный на станине станка 202 хонинговального станка 200 представляет собой горизонтально перемещаемый суппорт шпинделя 204 , который несет переднюю бабку 206 , в которой с возможностью вращения установлен хонинговальный шпиндель 210 хонинговального станка с горизонтальной осью шпинделя 211 . Электропривод 207 вращения шпинделя установлен на передней бабке.Возвратно-поступательный привод 205 , необходимый для возвратно-поступательного движения параллельно оси шпинделя 211 , установлен в станине станка и приводит в движение горизонтально выровненный шпиндель с резьбой, на котором движется гайка, соединенная с ползуном шпинделя 204 .
Возвратно-поступательный привод рассчитан на максимальную скорость возвратно-поступательного движения в диапазоне от 40 м / мин или 50 м / мин или более, поворотный привод для максимального числа оборотов приблизительно от 2500 до 3000 об / мин.Доступная мощность привода для возвратно-поступательного движения и вращения составляет более 10 кВт.
В случае примера обрабатываемая деталь 150 представляет собой картер цилиндра для рядного четырехцилиндрового двигателя (см. Фиг. 2B — фиг. 2D). Заготовка неподвижно закреплена на держателе заготовки 240 , который закреплен на верхней стороне станины станка. С помощью регулировочного привода, который может приводиться в действие станком или вручную, держатель заготовки может перемещаться горизонтально в горизонтальном направлении (направление X), проходя перпендикулярно оси шпинделя 211 (ось Z).Заготовка лежит своей плоской соединительной поверхностью с масляным поддоном 156 на держателе заготовки и точно позиционируется с помощью установочных штифтов 242 , так что точное положение заготовки относительно оси шпинделя 211 может фиксироваться за счет положения держателя заготовки 240 .
Поверхность соединения маслосборника 156 в случае этой установки служит в качестве производственной опорной поверхности для фиксации системы координат, которая фиксируется по отношению к заготовке по отношению к системе координат, которая фиксируется по отношению к машина.В случае других вариантов способа уже предварительно обработанная противоположная верхняя поверхность 154 (соединительная поверхность для головки блока цилиндров) служит в качестве производственной контрольной поверхности.
На стороне держателя заготовки, удаленной от шпинделя, на станине станка закреплено горизонтальное линейное направляющее устройство 230 , которое проходит параллельно оси шпинделя 211 и на котором движется салазок 232 , на котором установлен опорный элемент 234 для поворотного патрона 235 , который установлен в опорном элементе с возможностью вращения вокруг горизонтальной оси, проходящей соосно оси 211 шпинделя.Горизонтально перемещаемый вращающийся патрон 235 предусмотрен в качестве контрдержателя для конца хонинговального инструмента, удаленного от шпинделя. В данном примере ползун 232 механически принудительно соединен с ползуном 204 возвратно-поступательного привода. Также возможно, что движение пассивного суппорта 232 производится исключительно с помощью перемещаемого инструмента. В другом варианте контрдержатель имеет собственный привод, синхронизированный с возвратно-поступательным приводом хонинговального шпинделя.
Хонинговальный инструмент 270 жестко соединен с хонинговальным шпинделем 210 с помощью жесткого на изгиб приводного стержня 220 . С этой целью разъемная соединительная конструкция 225 между приводным стержнем и хонинговальным шпинделем выполнена в виде жесткой на изгиб жесткой соединительной конструкции для совместного вращения, например, в виде винтового соединения или простого фланцевого соединения. Разъемное соединение между приводным стержнем 220 и хонинговальным инструментом 270 также является жестким на изгиб и допускает совместное вращение.Для этой цели соединительная конструкция , 272, на стороне шпинделя хонинговального инструмента может быть сформирована, например, в виде винтовой резьбы, которая взаимодействует с соответствующей встречной резьбой на конце приводного стержня со стороны инструмента.
В других вариантах осуществления соединительная конструкция со стороны шпинделя хонинговального инструмента прикреплена непосредственно к концу хонинговального шпинделя со стороны инструмента, так что работа происходит без вставленного приводного стержня (см. Фиг. 5B).
Хонинговальный инструмент 270 имеет удлиненно-цилиндрический корпус инструмента 274 , на котором со стороны шпинделя сформирована соединительная конструкция со стороны шпинделя 272 , а с удаленной стороны — цилиндрический направляющий хвостовик 276 . от шпинделя.Ось инструмента 275 , проходящая по центру в корпусе инструмента, соосна оси шпинделя 211 в результате жесткого соединения. Установленные в радиальном направлении несущие полосы, на которых расположены удлиненные в осевом направлении режущие стержни 278 с алмазным режущим покрытием, установлены в радиальных отверстиях корпуса инструмента. Радиальная регулировка режущих стержней этого расширяемого хонинговального инструмента выполняется с помощью системы блокировки блокировки, которая не представлена более конкретно, приводится в действие электродвигателем или гидравлически и содержит регулирующий стержень с осевым смещением, который проходит через хонинговальный шпиндель и приводной стержень в хонинговальный инструмент, на конце которого расположен расширяющийся конус, который имеет одну или несколько опор и взаимодействует с коническими контрповерхностями на внутренних сторонах несущих полос, чтобы обеспечить осевое смещение регулировочного стержня радиальная регулировка режущих стержней без перекоса режущих стержней.
Длина режущих стержней, измеренная параллельно оси инструмента, предпочтительно составляет более 60%, возможно, даже более 70%, а в случае примера даже несколько более 80% длины отверстия подшипника коленчатого вала, которое должно быть обрабатывается хонинговальным инструментом, который, с одной стороны, обеспечивает высокую скорость съема материала, а с другой стороны, оказывает благоприятное влияние на прямолинейность отверстия или соосность опорных пластин.
В конфигурации обработки представленного хонинговального станка конец направляющего хвостовика 276 , удаленный от шпинделя, зажат во вращающемся патроне 235 .В результате одна режущая группа хонинговального инструмента, которая образована режущими стержнями , 276, , расположена между двумя точками опоры, стабилизируя положение оси инструмента. Одна из точек опоры образована установкой хонинговального шпинделя 210 в передней бабке 206 , противоположная точка опоры за счет патрона 235 , который установлен на ползуне 232 , может перемещаться в осевом направлении с инструмент для хонингования и служит контрподшипником.
Некоторые особенности детали 150 поясняются на основе фиг. 2B-D, 2 B, показывающий продольный разрез, фиг. 2С, показывающий вид сверху, параллельный оси отверстия отверстия подшипника коленчатого вала, а фиг. 2D, показывающий вид сверху, параллельный осям отверстий цилиндров. В некоторых отношениях к блокам двигателя и функциональным поверхностям и отверстиям, выполненным на них, применяются очень жесткие допуски, это должно гарантировать надежную работу. Отверстия цилиндра 151 обычно имеют допуск по цилиндрической форме и диаметру отверстия цилиндра в диапазоне нескольких микрометров, особое внимание также уделяется топографии поверхности.Допуски в диапазоне 100 мкм обычно применяются к расстоянию ZA между осями 150 отверстий цилиндров, так называемого калибра.
Точки опоры коленчатого вала в области отверстия под подшипник коленчатого вала 160 имеют несколько больший допуск по размерам, чем в случае отверстий цилиндров. Отверстие подшипника коленчатого вала является относительно длинным по сравнению с отверстием цилиндра (типичное отношение длины к диаметру не более 2,5), обычно с отношением длины к диаметру LDV, которое намного больше 2.5 или 3, а в примере — приблизительно 6. В случае четырехцилиндрового рядного двигателя отверстие подшипника коленчатого вала имеет пять участков отверстия от 161 до 165 , которые расположены на одной линии с одним. еще один последовательно на осевом расстоянии друг от друга. Отверстия образуют опоры коленчатого вала. Соосность этих точек опоры относительно друг друга особенно важна при установке коленчатого вала. Подшипники должны располагаться на одной линии как можно лучше, чтобы коленчатый вал мог вращаться концентрически и равномерно опираться на все точки подшипника.Соосность отдельных точек опоры не должна превышать 15 мкм или ненамного. Для определения «соосности» сделана ссылка на DIN ISO 1101, содержание которого до такой степени является содержанием настоящего описания.
Еще одним важным критерием в отношении отверстия под подшипник коленчатого вала является положение оси его отверстия 166 , которая определяет положение оси коленчатого вала во время работы двигателя. Термин «положение оси канала ствола» здесь предназначен для обозначения как абсолютного пространственного положения этой оси, так и ее углового положения, т.е.е. ориентация в пространстве. Вертикальное положение может быть определено, например, расстоянием ADA оси канала ствола от верхней поверхности 154 блока цилиндров на входе в канал или на выходе из канала (или соответствующим расстоянием AO от присоединения масляного поддона. поверхность 156 ). Расстояние между коленчатым валом и верхней поверхностью — один из критериев компрессии двигателя. Хотя здесь обычно не требуются допуски в диапазоне микрометров, желательны допуски в диапазоне нескольких сотых миллиметра.Точное положение коленчатого вала или оси отверстия подшипника коленчатого вала относительно отверстий цилиндра также важно для уменьшения износа компонентов, которые подвергаются высокой нагрузке, включая не только поршневые / поршневые пальцы, шатуны и соединительные детали. стержневые подшипники на коленчатом валу, а также крепления коленчатого вала в картере цилиндра. Угловое положение оси 166 отверстия, то есть ее ориентация по отношению к системе отсчета, которая закреплена по отношению к заготовке, также играет здесь роль.Положение оси канала 166 по отношению к общей длине канала BL обычно должно изменяться не более чем на 0,05 мм, причем это значение применяется как в вертикальном направлении (направление верхней поверхности), так и в поперечном направлении (горизонтальное направление на фиг. 2Б).
С помощью хонинговального станка 100 можно в случае блока цилиндров обработать отверстие под подшипник коленчатого вала 160 посредством хонингования сразу после окончательной обработки, выполняемой с помощью инструмента с геометрически заданной формой. режущей кромкой, например, после операции прецизионного сверления или операции развертывания, таким образом, что могут быть достигнуты все допуски в отношении соосности оси отверстия, а также в отношении требуемого качества поверхности точек опоры.Для этого можно выполнить следующую процедуру.
Во-первых, без промежуточного измерения, картер цилиндра 150 , перенесенный из устройства для точного сверления, зажимается на правильно установленном держателе заготовки 140 , который имеет очень жесткую на кручение конфигурацию, с помощью установочных штифтов. 142 , таким образом, чтобы ось шпинделя 111 хонинговального шпинделя была соосна желаемому положению оси отверстия отверстия подшипника коленчатого вала, которое требуется.Это осевое положение обычно будет лежать не по центру, а эксцентрично, по меньшей мере, относительно некоторых частей отверстия, подлежащих механической обработке. Более того, что касается желаемого диаметра, части отверстия имеют меньший размер, который необходимо удалить хонингованием. В зависимости от качества препарата размер меньше, например, может составлять не менее 0,1 мм.
После надежного зажима заготовки хонинговальный инструмент вводится в отверстие под подшипник коленчатого вала со стороны впуска по направлению к шпинделю до такой степени, что удаленная от шпинделя концевая часть направляющего стержня 176 может быть введен в патрон 135 и надежно там закреплен.На этом подготовительном этапе режущие стержни находятся в отведенном положении, так что хонинговальный инструмент, жестко соединенный с хонинговальным шпинделем и приводной штангой, может быть частично введен в отверстие подшипника коленчатого вала, не касаясь внутренних сторон точек подшипника в отверстие под подшипник коленчатого вала.
После этого включается возвратно-поступательный привод, поворотный привод и привод системы регулировки расширения режущей группы. Для достижения возможно значительного удаления материала за относительно короткое время цикла, максимальные скорости возвратно-поступательного движения и максимальное количество оборотов обычно значительно превышают соответствующие значения для обычного хонингования, как это принято, например, при обработке отверстий цилиндров.Максимальная скорость возвратно-поступательного движения может составлять более 20 м / мин или более 30 м / мин, например, до приблизительно 40 м / мин; максимальное число оборотов, по крайней мере, во время фазы хонингования, обычно превышает 1000 об / мин или больше, редко требуется более 2500 об / мин.
На продвинутой стадии расширения (увеличения диаметра) хонинговального инструмента наиболее лежащие внутрь части точек опоры затем обрабатываются сначала быстро вращающимся и быстро колеблющимся в осевом направлении хонинговальным инструментом с помощью многолезвийных режущих стержней.В случае участков отверстия, которые не полностью отцентрированы (например, внутренние лежащие несущие перемычки), сначала может быть односторонний частичный разрез, который постепенно становится полным вырезом по всей окружности участка отверстия. Таким образом, все части отверстия постепенно приобретают цилиндрическую форму с центром относительно оси инструмента 175 , так что соосность точек опоры улучшается.
Скорость резания может находиться в диапазоне 250 м / мин или более, например более 300 м / мин, или более 350 м / мин, или более 400 м / мин.Достижимый объем стружки при чистовой обработке, по крайней мере, на конечной стадии, когда материал удаляется на всех участках отверстия, может быть здесь намного больше, чем в случае обычных операций хонингования, например, в диапазоне более 200 мм 3 / с или даже более 500 мм 3 / с или более.
В этом приложении удельный объем стружки Q W S = V / t [мм 3 / с] берется за основу для определения объема стружки, где V — объем обрабатываемой детали. удаляется механической обработкой, и t — время обработки, необходимое для этого.Объем V определяется приближением V≈ (π (D 2 −d 2 ) L) / 4, где d — (меньший) диаметр отверстия перед удалением, D — (больший) диаметр после удаления, а L — длина обработанного отверстия или участка отверстия, диаметр которого был увеличен. Удельный объем стружки здесь отнесен или нормирован к времени обработки t = 20 с (соответствует типичному времени хонингования) и длине L = 20 мм (соответствует типичной ширине перемычки отдельной перемычки подшипника отверстия под подшипник коленчатого вала). двигатель легкового автомобиля).Значения объема стружки, указанные в таблице A (см. Конец описания), указаны для типичных номинальных диаметров отверстий от 40 до 70 мм. В тех столбцах, в которых количество перемычек равно 1, значения соответствуют удельному объему стружки для четырех различных диаметров.
Для типичного отверстия подшипника коленчатого вала рядного четырехцилиндрового двигателя диаметром 60 мм и 5 перемычек подшипника (участков отверстия), каждая длиной 20 мм, существует, например, значение объема стружки около 47 мм 3 / с (соответствует количеству снятия материала 0.1 мм в диаметре), а значение 236 мм 3 / с соответствует величине снятия материала 0,5 мм.
Часто достигаемые (общие) объемы стружки при обработке отверстий подшипников коленчатого вала с типичными диаметрами отверстий от примерно 40 мм до примерно 70 мм лежат в диапазоне примерно 60 мм от 3 / с до примерно 110 мм 3 / с в корпус из 5 несущих пластин и количество съема материала около 0,2 мм. Это значительное увеличение по сравнению с обычными методами хонингования.
Высокая мощность привода вместе с необычно большим числом оборотов и возвратно-поступательной скоростью позволяют значительно увеличить скорость резания по сравнению с обычным хонингованием.Это позволяет достичь требуемого количества съема материала по диаметру за обычное время хонингования, например, от 20 до 25 с, что соответствует объему стружки значительно более 200 мм 3 / с или даже более 500 мм 3 / с. Следовательно, параметры процесса хонингования могут быть установлены так, чтобы время хонингования для хонингования находилось в диапазоне времени хонингования при обычном хонинге отверстия подшипника коленчатого вала, то есть в диапазоне максимум от 20 до 25 секунд. Однако, поскольку хонингование позволяет отказаться от ранее необходимой операции сверления, более быстрая и, следовательно, более экономичная чистовая обработка отверстий подшипников коленчатого вала возможна с качеством, которое, по крайней мере, остается прежним.
Регулярное хонингование позволяет достичь коаксиальности менее 30 мкм или даже менее 15 мкм. В случае деталей, которые не были подготовлены достаточно хорошо, если, например, только точность положения оси отверстия, значительно превышающая ± 20 мкм, могла быть достигнута посредством обработки, выполняемой с определенными режущими кромками, активное изменение положения ось отверстия подшипника коленчатого вала может быть даже выполнена, что, однако, обычно не является необходимым.
Чтобы иметь возможность, например, корректировать соосность по мере необходимости, на хонинговальном станке реализована жесткая и точная концепция станка. Например, что касается хонинговального шпинделя, точные и жесткие узлы, которые имеют мало общего с соответствующими узлами традиционных хонинговальных станков, предоставляются посредством направления скольжения шпинделя до приемки заготовки. Например, хонинговальный шпиндель на обычных хонинговальных станках обычно устанавливается с простыми радиально-упорными шарикоподшипниками, а не с радиально-упорными шарикоподшипниками.Напротив, установка внутри передней бабки 106 обеспечивает более сложную опору, которая может подвергаться предварительному напряжению, то есть предварительно напряженный радиальный / осевой подшипник.
Кроме того, работа выполняется с помощью сравнительно длинных и тонких хонинговальных инструментов, которые во время обработки эксцентрично лежащих частей отверстия могут подвергаться высоким односторонним отклоняющим силам. Даже в этих тяжелых условиях положение оси инструмента остается стабильным соосно с желаемым положением оси отверстия, так как на стороне шпинделя хонинговальный инструмент жестко соединен с хонинговальным шпинделем, а на стороне, удаленной от шпинделя, он устанавливается на контрдержателе 135 .
В примерном варианте осуществления по фиг. На фиг.2А предусмотрена параллельная противовесная опора, перемещаемая за счет хода ползуна шпинделя и поэтому не требующая собственного привода (контрподшипник с пассивным приводом). Ход контрмонтажа может, например, находиться в диапазоне 500 мм. В качестве альтернативы также может быть предусмотрена фиксированная контрустановка, например, в виде подшипникового блока, который жестко установлен на станине станка и в котором имеется цилиндрическое отверстие для подшипника, расположенное коаксиально по отношению к оси шпинделя. 211 , через который цилиндрический направляющий стержень 207 и 276 может проходить без люфта и с небольшим трением в результате гидродинамической смазки.Также возможна комбинация переднего направления на входной стороне и заднего направления на выходной стороне (см. Фиг. 4).
Хонинговальный станок 200 сконструирован как горизонтальный станок, поэтому интеграция в автоматизированные производственные линии особенно проста. Горизонтальная конструкция также является благоприятной для доступа к компонентам машины и в отношении требования относительно длинной конструкции в осевом направлении в результате встречного монтажа. Конструкция как вертикальная машина, т.е.е. с вертикально выровненной осью шпинделя, однако в принципе возможно.
Хонингование, как правило, можно проводить за один этап обработки с помощью просто расширенного хонинговального инструмента. В результате требуемых высоких скоростей съема материала предпочтительны режущие стержни с алмазными режущими зернами, но, возможно, также могут использоваться другие твердые материалы с режущими зернами, такие как нитрид бора. Если работа выполняется со средним размером зерна в диапазоне от примерно 50 мкм до примерно 100 мкм до 150 мкм, может быть достигнут хороший компромисс между относительно высокой скоростью удаления и достаточно низкой шероховатостью обработанных внутренних поверхностей, для которой часто только остаточная шероховатость менее 15 мкм R z (средняя глубина шероховатости).
В частности, если желательна низкая остаточная шероховатость, работа также может выполняться на двух последовательных стадиях хонингования, причем вторая стадия работает с более мелким размером зерна.
В варианте осуществления, показанном на фиг. 3, хонинговальный инструмент 370 , предварительно установленный на желаемый размер (конечный размер), используется для хонингования отверстия подшипника коленчатого вала и жестко закреплен непосредственно на хонинговальном шпинделе 310 без вставки жесткого приводного стержня. Подобно варианту осуществления, показанному на фиг.2A, цилиндрический направляющий штифт 376 , который находится на удалении от шпинделя, зажат во вращающемся патроне контрдержателя 335 , который может пассивно перемещаться вместе с хонинговальным инструментом, чтобы действовать против отклоняющих сил, которые могут действовать от с одной стороны во время хонингования и для сохранения положения оси инструмента 375 всегда в желаемом положении оси отверстия, которое требуется. Хонинговальный инструмент 370 имеет относительно длинную коническую режущую область 377 и, непосредственно примыкающую к ней со стороны шпинделя, по существу цилиндрическую режущую область 378 , внешний диаметр которой соответствует желаемому окончательному размеру участков отверстия. .Диаметр конической области резания непрерывно увеличивается от переднего конца, удаленного от шпинделя, к концу по направлению к шпинделю с углом конуса в несколько градусов.
Хотя режущие стержни в конической области резания и в области калибровки можно настроить вручную перед установкой в хонинговальный станок, регулировка во время операции хонингования не предусмотрена и также не требуется, поэтому можно обойтись без структурные затраты на систему корректировки.Поскольку хонинговальный инструмент точно направляется относительно его осевого движения за счет жесткой связи с хонинговальным шпинделем и противодействующей фиксации на стороне, удаленной от шпинделя за пределами отверстия, хонинговальный инструмент не требует возможно расширяемых направляющих полос для поддержки внутри отверстие, так что хонинговальный инструмент может иметь относительно простую конструкцию.
В то время как в случае обычного хонингования с помощью расширяемых хонинговальных инструментов требуется много двойных ходов в сочетании с постепенным расширением хонинговального инструмента, общая операция по удалению материала при использовании таких хонинговальных инструментов на оправке обычно требует только одного двойного хода или несколько двойных ударов.Осевое возвратно-поступательное движение обычно в 5-10 раз меньше, чем в случае соответствующих методов хонингования с расширяемыми хонинговальными инструментами. Скорость осевого возвратно-поступательного движения в случае высокопроизводительного хонингования может, например, находиться в диапазоне 12 м / мин или более. В результате большого числа оборотов шпинделя, которое в случае этого варианта обработки может составлять до 2500 об / мин или даже до 3000 об / мин, в сочетании с небольшой возвратно-поступательной скоростью по отношению к этому, участки отверстия постепенно приводятся в одно положение. один за другим до готового размера, и в то же время, возможно, скорректированный в отношении их положения, когда хонинговальный инструмент проталкивается, так что после завершения одного или двух двойных ходов фактическое положение всех частей отверстия совпадает с желаемым положением, заданным осью инструмента 375 , а внутренние поверхности участков отверстия имеют желаемую цилиндрическую форму и структуру поверхности.
РИС. 4 и 5 показаны дополнительные возможности направления хонинговального инструмента, который является относительно длинным по сравнению с его диаметром и имеет длинную зону режущего стержня, надежно и устойчиво противодействуя поперечным силам в длинном отверстии, то есть отверстии коленчатого вала. В варианте осуществления, показанном на фиг. 4 удлиненный хонинговальный инструмент 470 соединен с хонинговальным шпинделем 410 посредством ограниченно гибкого приводного стержня 420 . На сторонах режущих стержней 478 рядом со шпинделем и на удалении от шпинделя по существу цилиндрический корпус инструмента образует цилиндрические направляющие стержни, то есть направляющий стержень 476 , удаленный от шпинделя, и направляющий стержень 477 рядом со шпинделем, на свободном конце которого установлена соединительная конструкция для соединения с приводной штангой.Направляющий хвостовик, удаленный от шпинделя, перемещается в осевом направлении в задней направляющей втулке 431 , которая удалена от шпинделя и расположена на выходной стороне заготовки. Направляющий стержень 477 по направлению к шпинделю перемещается в осевом направлении с возможностью скольжения на входной стороне заготовки в передней направляющей втулке 432 соответствующей конструкции. Центральные оси направляющих втулок фиксируют положение и ориентацию оси инструмента, а следовательно, и положение и ориентацию готового отверстия подшипника коленчатого вала.Контродержатель на торцевой стороне здесь не требуется.
В варианте, показанном на фиг. 5, хонинговальный инструмент 570 , оснащенный непрерывными длинными режущими стержнями 578 , направляется радиально неподвижно и с возможностью вращения вокруг оси инструмента внутри заготовки между двумя смежными в осевом направлении перемычками подшипника с помощью приспособления для крепления инструмента 590 . «Внутреннее» крепление инструмента 590 , показанное на фиг. 5A в осевом разрезе и на фиг. 5В на виде сверху имеет пластинчатый несущий элемент 591 , который прикреплен к верхней стороне станины машины.В цилиндрическом отверстии опорного элемента расположен по существу кольцевой направляющий элемент 592 , который установлен с неограниченным поворотом с помощью подшипника качения относительно опорного элемента 591 , который закреплен относительно машина. Направляющий элемент 592 имеет непрерывное в осевом направлении направляющее отверстие 593 , адаптированное к внешнему диаметру хонинговального инструмента, для прохода через хонинговальный инструмент. По окружности направляющего элемента на его внутренней стороне имеется ряд радиальных выемок 594 , которые равномерно распределены по окружности, количество которых соответствует количеству режущих стержней и которые имеют такие размеры, что даже при максимальном расширении хонинговального инструмента режущие стержни входят в выемки, не касаясь направляющего элемента.К кольцевому направляющему элементу 592 прикреплен приводной элемент 595 , который выступает внутрь по внутренней окружности кольцевой части направляющего элемента в проходное отверстие 593 , в остальном в основном круглое. Выступающая внутрь часть имеет такие размеры, что она входит, по существу, без люфта в окружном направлении, в продольную канавку 579 , которая предусмотрена на корпусе инструмента 574 хонинговального инструмента и проходит параллельно оси инструмента над по всей длине корпуса инструмента по центру между двумя смежными по окружности режущими стержнями.
Перед началом хонингования хонинговальный инструмент 570 , жестко закрепленный непосредственно на хонинговальном шпинделе 510 , проталкивается со стороны входа в отверстие подшипника коленчатого вала и, таким образом, сначала проходит своим направляющим хвостовиком 576 вдали от шпиндель через направляющее отверстие 593 внутреннего держателя инструмента 590 . Относительное положение вращения хонинговального инструмента и вращающегося направляющего элемента 592 выбирается таким образом, чтобы выступающая внутрь часть приводного элемента 595 уже была ввинчена в продольную канавку 579 в основном без люфта в области направляющий хвостовик удален от шпинделя.В результате для дальнейшего введения хонинговального инструмента обеспечивается то, что режущие стержни 578 могут проходить через направляющее кольцо 592 , не касаясь его. После того, как хонинговальный инструмент введен достаточно глубоко, свободный конец направляющего стержня 576 зажимается в контрдержателе 535 . Во время хонингования хонинговальный инструмент перемещается вперед и назад в соответствии с осевым возвратно-поступательным движением в направляющем отверстии 593 , в то же время кольцевой направляющий элемент поворачивается внутри опорного элемента за счет вращения хонинговального инструмента. посредством приводного элемента 595 .Это обеспечивает надежную опору хонинговального инструмента в заготовке, так что изгиб длинного хонинговального инструмента максимально предотвращается даже при сильных радиальных силах. Поскольку поворотный направляющий элемент 592 является пассивным, то есть не имеет собственного привода, а перемещается за счет движения хонинговального инструмента, такое решение является относительно недорогим и в то же время очень прочным и надежным в эксплуатации. .
Такая «внутренняя направляющая», которая может быть расположена в промежуточном пространстве между аксиально смежными частями отверстия, также может быть реализована в других примерных вариантах осуществления, например варианте осуществления, показанном на фиг.2А. Также могут быть предусмотрены две или более внутренних направляющих. Возможно, можно будет отказаться от встречного монтажа на торцевой стороне, в частности, если внутренняя направляющая предусмотрена в последнем промежуточном пространстве на торцевой стороне между несущими пластинами.
В случае варианта метода в качестве особой особенности предусмотрено, что одно или несколько индексирующих отверстий завершаются на заготовке, зажатой на хонинговальном станке для операции хонингования и закрепленной в правильном положении с этой стороны. который предназначен для последующего крепления трансмиссии (сторона трансмиссии) и / или на противоположной торцевой стороне (сторона управления).В дополнение к хонинговальному шпинделю на хонинговальном станке для этой цели могут быть предусмотрены, например, два отдельных обрабатывающих шпинделя, с которыми, соответственно, может быть жестко соединен расширительный инструмент. Установочные отверстия для позиционно-правильного соединения трансмиссии или соединения других компонентов обычно производятся после завершения точного сверления и перед хонингованием на станке, предназначенном для точного сверления. Для этого уже имеющиеся на заготовке грубо обработанные отверстия обрабатываются с небольшим позиционным допуском (обычно ± 5/100 мм) по отношению к оси отверстия отверстия подшипника коленчатого вала, например, посредством операции развертывания.Затем эту операцию обработки можно перенести на сторону хонингования, чтобы выполнить чистовую обработку индексирующих отверстий и хонингование параллельно в одной и той же установке, либо в одно и то же время (параллельно) или одно за другим. Следовательно, делительные отверстия могут быть обработаны с особенно высокой точностью в отношении совмещения отверстия подшипника коленчатого вала, поскольку больше не нужно повторно зажимать заготовку между окончательной операцией механической обработки с удалением материала на отверстии подшипника коленчатого вала (хонингованием) и чистовая обработка индексных отверстий.
Отверстие подшипника коленчатого вала является типичным примером относительно длинного отверстия, то есть отверстия с осевой длиной, которая относительно велика по сравнению с диаметром отверстия. «Длинные отверстия» в смысле этой заявки обычно имеют отношение длины к диаметру LDV намного больше, чем 2,5 или 3, при этом LDV может быть, например, более 4, или более 6, или более 8. В отличие от этого, « короткие отверстия », такие как, например, отверстия цилиндров в двигателях внутреннего сгорания, имеют типичное отношение длины к диаметру LDV не более 2.5. Устройства и методы, описанные в этой заявке, оптимизированы, в частности, для обработки длинных отверстий, но в принципе могут использоваться и в случае коротких отверстий.
Далее описаны некоторые примеры предпочтительных вариантов операций обработки с помощью инструментов с геометрически заданными режущими кромками.
РИС. На фиг.6 показан картер цилиндра 150 , который зажат на держателе 640 заготовки, который можно неограниченно вращать вокруг вертикальной оси вращения держателя заготовки 642 для окончательной чистовой операции с геометрически заданной режущей кромкой.Заготовка фиксируется в заданном положении на держателе заготовки с помощью индексирующих устройств. Держатель заготовки является частью устройства для точного сверления, которое имеет шпиндель прецизионного сверления 622 , ось вращения которого 623 проходит горизонтально и перпендикулярно оси вращения держателя инструмента 642 . Шпиндель точного сверления может перемещаться горизонтально и вращаться вокруг оси шпинделя 623 с помощью привода шпинделя.
Инструмент для точного сверления 628 жестко соединен со свободным концом шпинделя для точного сверления 622 . Одна или несколько режущих пластин, состоящих из твердого металла, из которых представлена только одна режущая пластина 629 , расположены по окружности корпуса инструмента для прецизионного сверлильного инструмента.
Прецизионный сверлильный инструмент 628 выполнен в виде короткого инструмента, длина обработки которого AL намного меньше длины BL отверстия подшипника коленчатого вала.В данном примере длина обработки составляет от 60 до 70% длины отверстия. Благодаря жесткому соединению со шпинделем для точного сверления и небольшому выступу в этой конструкции инструмент для точного сверления очень устойчив по отношению к поперечным силам и, когда имеется продвижение параллельно оси шпинделя 623 , перемещается по существу соосно по отношению к нему, без какого-либо существенного бокового отклонения в поперечном направлении по отношению к оси вращения.
В случае показанного блока цилиндров для четырехцилиндрового рядного двигателя отверстие под подшипник коленчатого вала 160 имеет в общей сложности пять участков отверстия, которые образуют точки опоры для коленчатого вала, то есть первая часть отверстия 161 , вторая часть отверстия 162 , третья часть отверстия 163 , четвертая часть отверстия 164 и пятая часть отверстия 165 .
При двусторонней обработке, показанной в качестве примера, заготовка 150 первоначально приводится в первое показанное положение вращения, в котором конец отверстия с пятой частью отверстия 165 обращен к прецизионный сверлильный шпиндель 622 .Для обработки положение заготовки устанавливается таким образом, что ось шпинделя 623 и ось вращения прецизионного сверлильного инструмента на одной линии с ним лежат соосно с желаемым положением оси отверстия 166 . Затем прецизионный сверлильный инструмент приводится во вращение и медленно продвигается в направлении заготовки, так что один за другим сначала пятая часть отверстия 165 , затем четвертая часть отверстия 164 и, наконец, третья часть отверстия. части 162 обрабатываются посредством прецизионного сверления (представлена ситуация механической обработки).Первые две части отверстия 161 и 162 на стороне, противоположной шпинделю, остаются необработанными на этой стадии обработки.
Затем прецизионный сверлильный инструмент извлекается из отверстия, и заготовка поворачивается на 180 ° вокруг оси вращения держателя заготовки 642 .
После этого вращающийся инструмент вводится с той стороны отверстия, которое начинается с первой части отверстия 161 . В этом случае инструмент для прецизионного сверления снова продвигается соосно по отношению к оси 166 отверстия до тех пор, пока первая часть отверстия и вторая часть отверстия не будут обработаны аналогичным образом.После этого прецизионный сверлильный инструмент снова извлекается из отверстия, и операция двусторонней обработки завершается.
При этой двусторонней механической обработке, по крайней мере, положения торцевых частей отверстия, то есть первой части отверстия 161 и пятой части отверстия 165 , правильно позиционируются с большой точностью. относительно желаемого положения оси отверстия 166 . Что касается других расположенных внутрь участков отверстия, небольшие отклонения могут быть вызваны тем, что инструмент для точного сверления несколько отклоняется в сторону в ходе осевого продвижения.
Поскольку «положение оси отверстия» определяется положением точек подшипника на стороне впуска и на стороне выпуска, положение оси отверстия при двусторонней обработке может быть точно установлено с большой надежностью. Соосность также может выходить за пределы допусков, поскольку внутренние лежащие перемычки еще не находятся в своем точном положении.
Соосность может быть исправлена последующей операцией хонингования и, следовательно, приведена в диапазон допуска.
В случае примера, показанного на фиг.6, операция окончательной чистовой обработки с геометрическими режущими кромками выполнена в виде получистовой обработки с типичными объемами снятия материала от 0,4 мм до 0,5 мм. Остальная часть полного удаления выполняется хонингованием.
Также при использовании расширительного инструмента для окончательной чистовой операции с геометрически заданными режущими кромками может быть выгодна соответствующая двусторонняя обработка, при этом короткий инструмент может быть выполнен как расширительный инструмент, который направляется в радиальном направлении внутри участка отверстия, имеющего уже обработаны развёртыванием с помощью направляющих элементов со стороны инструмента.
В некоторых вариантах осуществления соответствующая двусторонняя обработка с большим съемом материала также предусмотрена в случае операции выравнивания, предшествующей операции окончательной чистовой обработки, с геометрически заданными режущими кромками, при которой отверстие подшипника коленчатого вала обрабатывается с относительно большим объемом удаления материала с помощью геометрически определенных режущих кромок сразу после установки крышки подшипника, то есть после подготовки отверстия под подшипник коленчатого вала, чтобы уменьшить возможные неровности, возникающие в результате сборки.Типичные максимальные количества съема материала при операции выравнивания в предпочтительных вариантах осуществления находятся в диапазоне от примерно 1 мм до примерно 2 мм по отношению к диаметру.
Различные операции чистовой обработки, упомянутые здесь в качестве примера, могут быть объединены для образования различных технологических цепочек. В случае одного из вариантов сначала выполняется двусторонняя операция выравнивания с помощью подходящего сильно удаляемого инструмента для точного сверления. В качестве заключительной чистовой операции с геометрически заданными режущими кромками перед переносом заготовки на хонинговальное устройство за ней следует двусторонний получистовой пропил, поясняемый на основе фиг.6. В одном из вариантов этого метода вместо инструмента для точного сверления, который используется для получистовой обработки, используется инструмент для развёртывания с направляющей. В обоих вариантах за перемещением следует операция хонингования, которая предпочтительно выполняется как операция хонингования оправки (см. Фиг. 3 и соответствующее описание).
В случае другого варианта метода операция правки выполняется на отдельном станке. Например, в зависимости от продолжительности цикла этап выравнивания может выполняться на отдельной станции, с установленными на противоположной стороне буровыми штангами или в сочетании с операцией получистовой обработки с использованием буровой штанги, установленной на противоположной стороне.Если этап выравнивания выполняется на отдельном станке, за ним, также как и на отдельном станке, может следовать операция получистового точного сверления с установленным напротив него групповым инструментом для точного сверления, в котором предусмотрены для каждой части отверстия. обрабатывать собственную режущую группу с одной или несколькими геометрически заданными режущими кромками. Здесь также за переходом на хонинговальное устройство следует операция хонингования, которая предпочтительно выполняется как операция хонингования оправки.
Метод чистовой обработки и используемые для него устройства позволяют значительно сократить технологическую цепочку при чистовой обработке отверстий подшипников коленчатого вала.
ТАБЛИЦА A | |||||||||||||||||||
Объем стружки Qw [мм {циркумфлекс над ()} 3 / с] | |||||||||||||||||||
Диаметр [мм] | |||||||||||||||||||
60 | 70 | ||||||||||||||||||
Количество полотен | |||||||||||||||||||
1 | 3 | 4 | 5 | 7 | 1 | 000400040004 31 | 3 | 4 | 5 | 7 | 1 | 3 | 4 | 5 | 7 | ||||
Удаление8 | 5 | 15 | 20 | 25 | 35 | 6 | 19 | 25 | 31 | 44 | 8 | 23 | 38 | 26 | 35 | 44 | 62 | ||
из | 0,1 | 6 | 19 | 25 | 31 | 44 | 8 | 24 | 0009 | 28 | 38 | 47 | 66 | 11 | 33 | 44 | 55 | 77 | |
материал | 0.2 | 13 | 38 | 50 | 63 | 88 | 16 | 47 | 63 | 79 | 110 | 19 | 57 | 94 | 000594 | 000566 | 88 | 110 | 154 |
диаметр | 0,5 | 31 | 94 | 126 | 157 | 220 | 39 | 0005118 | 118 | 47 | 141 | 188 | 236 | 330 | 55 | 165 | 220 | 275 | 385 |
[мм] | 1286 920128
Ссылка на: Поршневой цилиндр Апплет площади поверхности Получение модели кривошипа Объем поршневого цилиндра можно определить как функцию угол поворота кривошипа от степени сжатия, хода, диаметра и соединения длина стержня.Геометрические параметры поршневого цилиндра представлены. на рисунке 1.
Верхняя мертвая точка относится к положению коленчатого вала на кривошипе. угол 0 o .Это положение также известно как зазор. объем, В c . В нижней мертвой точке угол поворота коленчатого вала 180 o . В этом положении объем цилиндра максимальный, V 1 . Разница между максимальной и минимальной громкостью, V 1 — V o , определяется как рабочий объем V d . Смещение объем также может быть представлен как функция диаметра ствола и хода: (1)
Окончательная форма модели Slider-Crank дана как безразмерная отношения, разделив обе части уравнения (6) на V d .
Расчет площади поверхности поршневого цилиндра Чтобы изучить влияние теплопередачи в поршневом цилиндре, необходимо оценить площадь поверхности цилиндра. |