Из какого пластика делают бампера: Виды автомобильных пластиков – 403 — Доступ запрещён
Виды автомобильных пластиков

В состав современных автомобилей входит около 120 килограмм деталей, сделанных из различных видов пластика.
Термин пластики (пластмассы) описывает группу химических соединений называемых полимерами. Пластик получается нагреванием углеводородов. Используется катализатор, чтобы разбить большие молекулы на маленькие. Этот процесс называется крэкинг. Маленькие молекулы, такие как этилен, пропилен, бутан и другие называются мономерами. Большинство пластиков сделано из углеводородов, взятых из природных ископаемых (газа, нефти и других). Осуществляется химическое соединение мономеров и создание полимеров. Размер и структура молекул полимеров определяют свойства пластиков.
Существует два базовых типа пластика, которые применяются в автомобилестроении – термопластики и термореактивные пластики. Термопластики плавятся от воздействия высокой температуры, а при остывании снова затвердевают.
Термопластики
Термопластики – это название пластиков, состоящих из разделённых разветвлённых макромолекул, которые, однако, не связаны друг с другом.
Из-за своих многочисленных положительных свойств, термопластики являются наиболее часто используемыми пластиками в автомобильной индустрии.
Термопластики могут быть расплавлены и использованы снова много раз. Это важный аспект экологичности. Термопластики являются идеальным материалом для переработки. Новые детали могут быть сделаны из старых.
Термореактивные пластики (реактопласты)
При изготовлении изделий из термореактивных пластиков происходит необратимая реакция.
Эти пластики нельзя сваривать, растворять или растягивать, как эластомеры.
Термореактивные материалы очень прочные и стойкие к высокой температуре. Они, к примеру, используются в подкапотном пространстве, рядом с двигателем.
Смеси пластиков (сплавы)
Смеси (например, такие как PP+EPDM) чаще всего используются в дополнение к чистым формам. Смешиваются два разных типа пластика. При смешивании двух типов пластика, их свойства объединяются, и получается новый тип пластика. Этот процесс похож на смешивание металлов и получение сплавов с новыми свойствами. Кроме того, многие пластиковые детали при изготовлении усиливаются стекловолокном.
Как определить тип пластика?
Определение типа пластика необходимо для выбора способа ремонта и видов материалов, необходимых для этого.
- Тип пластика можно определить по буквенному обозначению на обратной стороне пластиковой детали. Это самый надёжный и точный способ. С обратной стороны есть несколько латинских букв — сокращение от названия пластика. Иногда дополнительные буквенные и цифровые обозначения показывают наличие различных добавок к пластику. Могут также отмечаться дополнительные свойства базового пластика (например HD-High Density, высокая плотность), а также смеси пластиков (знаком «+» тип пластика после него). Ниже в статье будут перечислены наиболее часто встречающиеся сокращения и их расшифровка. Если по каким-то причинам нет возможности определить тип пластика по коду, то можно это сделать, проделав тест.
- Тест с водой. Отрежьте маленькую полоску снизу бампера. Очистите её от загрязнений и краски, чтобы получить «голый» пластик. Поместите его в ёмкость с водой. Если пластик не тонет, то это PE, PP, PP + EPDM (термопластики). Из этих пластиков сделано 80% бамперов. 15% — это реактопласты (PUR/TPUR), которые потонут в воде. Остальные 5% — xenoy/polycarbonate. Такой пластик можно найти на некоторых Мерседесах и старых Фордах. Он очень жёсткий и при погружении в воду он потонет. Стоит сделать замечание, что некоторые смеси пластиков могут потонуть, хотя являются термопластиками, но в основном этот тест работает.
- Тест огнём определяет принадлежность к тому или другому типу пластика по размеру пламени, его цвету и типу дыма. Ввиду того, что в состав современных пластиковых деталей автомобиля входят различные добавки, этот тест не всегда помогает определить тип пластика правильно, поэтому мы его рассматривать не будем.
В то время как несколько видов пластика может использоваться в машине, три основных типа составляют 65% всего пластика, используемого в автомобиле: PP — полипропилен (32%), PU/PUR полиуретан (17%) и PVC — поливинилхлорид (16%).
Итак, рассмотрим наиболее часто используемые в автомобилях типы пластиков.
Типы автомобильных пластиков
ABS (Acrylonitrile Butadiene Styrene) — термопластик
Твёрдый, прочный и негибкий пластик. Он имеет высокую прочность благодаря компоненту бутадиену, а твёрдость и негибкость благодаря акрилонитрилу.
Этот пластик обязательно должен быть покрыт защитным покрытием, так как на него разрушительно действуют ультрафиолетовые лучи.
Применение: Корпуса зеркал заднего вида, колпаки колёс, автомобильные панели приборов, радиаторные решётки, молдинги, обрамления фар.
Совет по ремонту: Оптимальным методом ремонта является склеивание специальным клеем (к примеру, PlastiFix). Если применяется сваривание, то его можно дополнять эпоксидной смолой со стекловолокном (с обратной стороны) для повышения прочности.
ABS/MAT — реактопласт
Это пластик ABS, усиленный стекловолокном.
Применение: Пластиковые панели кузова.
EPDM (Ethylen-propylene-diene-monomer) — реактопласт
Часто используется в сплаве с полипропиленом (PP) для изготовления бамперов.
Применение: Ударопрочные вставки бампера, бампера (PP+ EPDM).
PA (Polyamide (Nylon)) — реактопласт
Умеренно жёсткий или жёсткий пластик. Хорошо шлифуется. Известен как нейлон.
Является стойким к органическим растворителям. Имеет высокую сопротивляемость к истиранию.
Применение: Пластмассовые внешние детали отделки кузова, декоративные колпаки колёс, лючки бензобака, радиаторные бачки, корпуса фар, корпус боковых зеркал, пластиковые части двигателя.
Совет по ремонту: Нагревайте пластик феном перед началом сваривания. Присадочный пруток должен смешиваться с ремонтируемым пластиком.
PC (Polycarbonate) — термопластик
У этого пластика высокая ударопрочность, даже при очень низких температурах.
Применение: Бампера, радиаторные решётки, приборная панель, корпуса фар.
Совет по ремонту: Перед сваривание пластик лучше нагреть феном.
PPO (Polyphenylene oxide) — реактопласт
Имеет хорошую стойкость к высокой температуре и высокую ударопрочность. Редко используется в чистой форме из-за сложности технологического процесса.
Применение: Хромированные пластиковые детали, решётки радиатора, обрамление фар.
PE (Polyethylene) — термопластик
Умеренно эластичный, обычно полупрозрачный пластик.
Полиэтилен имеет высокую ударопрочность и хорошо выдерживает воздействие кислот, спиртов и нефтепродуктов.
Может быть двух типов – полиэтилен низкой плотности (PE-LD) и полиэтилен высокой плотности (PE-HD).
Применение: Подкрылки, облицовка салона, расширительные бачки, бачки для «омывайки», подкрылки, бензобаки (делаются из полиэтилена высокой плотности PE- HD).
Совет по ремонту: Нужно помнить, что на это этот вид пластика имеет плохую адгезию к ремонтным материалам и краске.
PP (Polypropylene) — термопластик
Умеренно гибкий пластик, устойчивый к воздействию химически активных жидкостей. Инертен к ультрафиолетовым лучам. Полипропилен имеет относительно слабую ударопрочность.
Применение: бампера (обычно смесь с EPDM), изоляция проводки, корпуса аккумуляторов, подкрылки, уплотнители салона, облицовка салона, панель приборов.
Совет по ремонту: Перед нанесением грунтов или лакокрасочных материалов требуется предварительно применять специальный грунт для пластика для увеличения адгезии.
PU/PUR (Polyurethane) — реактопласт
Полиуретан очень износостойкий, гибкий и прочный пластик. Он может быть изготовлен твёрдым, как шар для бойлинга, а также таким мягким, как стирательный ластик.
Этот пластик представляет собой структурную пену, твёрдость и эластичность которой может варьироваться. Эластичный полиуретан может восстанавливать первоначальную форму даже после длительного физического воздействия.
Применение: Бампера, подкрылки, пластиковые накладки кузова, элементы отделки салона, панели приборов, сидения (вспененный полиуретан).
Совет по ремонту: При сваривании не нужно нагревать и пытаться расплавить ремонтируемый пластик. Расплавленный присадочный пруток нужно помещать в заранее подготовленную V‑образную канавку.
PVC (Polyvinyl chloride) — термопластик
Твёрдый, хорошо шлифуется. Это гибкий пластик, имеет хорошую сопротивляемость к растворителям. Виниловая составляющая даёт хорошую прочность на разрыв, некоторые поливинилхлоридовые пластики эластичные.
Применение: Боковые молдинги дверей, элементы облицовки салона.
Для полноты обзора пластиков, приведу сводную таблицу, имеющую также обозначения других видов пластика.
[adsp-pro‑4]
Печатать статью
Ещё интересные статьи:
виды пластмасс
виды пластмассвиды пластмасс в автомобилестроении
В данной статье я хочу рассказать про основные виды пластмасс, используемых в автомобилестроении. Сейчас производители все чаще смешивают разные пластмассы, что усложняет их подбор при сварке. Каждая пластмасса имеет свою маркировку, которая наносится с внутренней части изделия, и выглядит например так >HDPE<.
>PP< полипропилен — самая распространенная пластмасса. Из нее бывают почти любые изделия ( бампера, подкрылки, защиты, бачки и т.д ) . Бывает с маркировкой >PP-T40<, >PP-T20< (фары, корпуса воздушных фильтров) , >PP-EPDM< >PP-PE< (бампера, подкрылки) и т.д..
>PE< полиэтилен — более распространен в французских автомобилях. Делают те же изделия , что и из полипропилена. Еще почти все топливные баки.
>ABS< Акрилонитрилбутадиенстирол — наиболее хрупкая пластмасса, но хорошо держит форму. Легко плавится и хорошо поддается ремонту. Из нее обычно сделаны изделия не подверженные нагрузкам, имеющие больше эстетический характер ( решетки радиаторов, обшивки, части приборной панели и т.д.)
>PA66< Полиамид 66 — отличается более высокими прочными свойствами и деформационной теплостойкостью. Очень плохо плавится, что затрудняет его ремонт. Обычно из него сделаны изделия подверженные нагрузке, температуре, давлению ( боковины радиаторов, впускные коллектора, ручки, бачки и т.д.).
>POM< полиформальдегид — имеет высокое соотношение прочности и упругости, а также обладает хорошим сопротивлением к усталостным нагрузкам, деформации и истиранию. Легко плавится и хорошо поддается ремонту. При сварке отличается резким запахом. Делают из него обычно механизмы стеклоподъемников, части топливных насосов и т.д..
>ASA< акрилонитрил-стирол-акрилат — атмосферостойкий аналог ABS пластика. В ремонте от ABS отличается тем, что очень плохо варится сваркой.
>HDPE< Полиэтилен низкого давления — является легким эластичным термопластичным материалом. Легко плавится, но очень плохо поддается ремонту. Почти не варится и я не встречал клей, который мог бы его склеить. Делают из него в основном подкрылки, бачки омывателя, крайне редко бампера.
>PC< поликарбонат — благодаря высокой прочности и ударной вязкости (250—500 кдж/м2) применяется в качестве конструкционных материалов в различных отраслях. В автомобилях из него делают стекла задних фонарей и рассеиватели передних.
>PCPBT< Смесь поликарбонатов и полибутилентерефталата — Обладает высокой прочностью, стойкостью к ударным нагрузкам, в том числе при низких температурах, стойкостью к статическим нагрузкам и вибрациям. Хорошо поддаётся ремонту хоть и не очень хорошо плавится. Из него сделаны почти все бампера у таких марок как Mercedes, BMW и FORD примерно до 2000 года. Очень широко используется в грузовых автомобилях.
Это основные пластики, которые встречаются в автомобилях. Есть и другие, но встречаются они редко. В более новых моделях, как я писал выше, все чаще используются смешанные пластики. Например >PP-PE<, >PA-ABS< и т.д.
Если есть вопросы, пишите на форуме, постараюсь помочь.
<div><img src=»//mc.yandex.ru/watch/24565976″ alt=»» /></div>
пошаговая инструкция и полезные советы
Никто из водителей не застрахован от повреждения бампера. Если дефекты незначительны, то ремонт конструкции делают самостоятельно. Ремонт бампера из пластика своими руками получится по финансам меньше, чем покупка нового. Пошаговая инструкция починки молдинга в домашних условиях позволит сделать все правильно и качественно.
Популярные материалы для бамперов

Автомобильная промышленность изготавливает бампера из нескольких разновидностей пластмассы. Этот материал легкий, но прочный. К основным относят:
- Термопласты. Это полипропилен, поликарбонат, полиэтилен и полиамид. Главное, их отличие – это возможность становиться вязко-текучими в результате нагревания, а при остывании снова затвердевать. Благодаря этому пластмассу можно изменять по форме много раз.
- Реактопласты. Это полиуретан и стеклопластик. Их особенность – это неспособность после затвердевания возвращаться в вязкое состояние. Из-за этого возможности по обработке ограничены.
Узнать, из какого материала изготовлен молдинг легко: достаточно посмотреть на внутреннюю сторону детали. Там прописана аббревиатура на латинском.
Поэтому при ремонте пластмассового бампера важно знать, из какого материала он сделан. Если деталь произведена из термопластичного пластика, то за счет размягчения ее легко можно снова сделать единой конструкцией. Если это термореактивная пластмасса – сварку использовать нельзя.
Типы повреждений
В процессе эксплуатации автомобиль подвергается незначительным повреждениям. В момент движения от дороги отлетают мелкие камешки, песок или другие незначительные детали. Возникают небольшие царапины или вмятины. В результате наезда на препятствия или незначительных столкновений могут возникнуть трещины или проломы.
Царапина

Такие повреждения могут быть незначительным поверхностным или глубокими. В первом случае повреждают только лакокрасочное покрытие, не задевая основу. Глубокие царапины проникают в материал конструкции и со временем приводят к трещине. Для ремонта бампера используют жидкий пластик.
Вмятина и пробои
Еще одно повреждение детали – это образование вмятины или каверны. Возникает в результате механических или химических воздействий. Такая деформация сопровождается царапинами в месте повреждения. Кроме того, возможны трещины легкого, среднего или тяжелого характера. К серьезной поломке относят пробои и сколы. Это когда при столкновении с препятствием возникает сквозное отверстие или скол фрагмента.
Трещина
Это дефект, при котором происходит сквозное повреждение конструкции. Отремонтировать бампер, когда он треснул, необходимо в ближайшее время. В этом случае использовать автомобиль не рекомендуют. Ведь в процессе движения на бампер поступают вибрационные нагрузки, за счет которых трещины увеличиваются. А это делает деталь менее прочной и небезопасной при эксплуатации.
Необходимые материалы и инструменты

Для самостоятельного ремонта бампера в домашних условиях, в первую очередь, изучают хорошо теорию, а затем уже приобретают необходимый материал и инструменты. Лучше всего проводить ремонт своими руками заднего или переднего бампера профессиональными инструментами:
- газовая горелка или термопистолет;
- электрический или воздушный паяльник.
Термопистолет удобный тем, что он позволяет регулировать температуру, за счет чего плавящийся материал не будет испаряться. Если такого инструмента нет, то подойдет газовая горелка. Но она неспособна регулировать температуру, а из-за того, что огонь открытый качество пайки невысокое. Воздушный паяльник удобный и безопасный. Пайка происходит с помощью сжатого воздуха. Электрический паяльник актуален при незначительных вмятинах.
Кроме того, чтобы отремонтировать самому пластиковый бампер, понадобятся дополнительные инструменты:
- металлическая сетка;
- автомобильная грунтовка;
- шпатлевка;
- наждачная бумага;
- перчатки и тряпочный кусок;
- мебельный степлер.
В автомобильных магазинах продаются специальные наборы для ремонта пластиковых бамперов. В комплект входит наждачная бумага, наполнители и различная краска, грунтовка и шпаклевка.
Способы ремонта

Ремонт пластиковых бамперов происходит двумя способами: склейка и сварка. Второй вариант требует навыков и опыта. А вот со склеиванием можно поэкспериментировать.
Склейка
Починить своими руками бампер можно и с помощью склеивания. Для этого хорошо обрабатывают края деталей. Это позволит им хорошо стыковываться. Если кусок молдинга отсутствует, его заменяют другим аналогичным или изготавливают элемент из клея и стеклоткани. По краям каждого склеиваемого элемента делают отверстия и борозды для нити. Края стягивают между собой и обрабатывают поверхность, обезжиривают ее.
Восстановление своими руками бампера происходит в следующем порядке: сначала нарезают стеклоткань необходимых размеров. На нее наносят клей так, чтобы ткань хорошо пропиталась. Клеящейся состав наносится и на шов. На поврежденное место накладывают стеклоткань и сверху покрывают клеем. Чтобы процесс склеивания проходил быстрее, используют ультразвуковую лампу.
Сварка
Прежде чем отремонтировать бампер автомобиля из пластика своими руками, подготавливают электроды из сырья, что аналогичный материалу поврежденной конструкции. Сначала очищают место повреждения от грязи и краски. Затем края разрыва аккуратно обрабатывают феном-паяльником. Электрод подготавливают такой же, как и размер шва, при этом сечение его должно напоминать треугольник. Заточенный электрод помещают в трещину и аккуратно паяльником заваривают. Остатки убирают болгаркой и шлифуют до гладкости поверхности.
Возможные ошибки
При ремонте трещины в бампере своими руками могут возникать ошибки, которые отобразятся на качестве работы. Сначала хорошо очищают деталь. На старой конструкции остаются грязь, пыль, давняя полировка или масло. На новой детали могут остаться составы, на восковой основе, которые используют в работе с пресс-формами. Для качественной очистки используют очиститель или обезжириватель. Наносят очищающий состав одной салфеткой, а протирают и убирают остатки другой салфеткой.
Затем правильно обрабатывают деталь мелким абразивом. Если шлифовку выполнить некачественно, то на поверхности бампера новая краска может отшелушиться. Поэтому перед покраской хорошо проверяют участок, чтобы не осталось необработанных мест. Чтобы правильно восстановить бампер используют специальную шпаклевку для пластиковых конструкций. Если использовать стандартную полиэстерную шпаклевку, то возможны дефекты, так как она недостаточно пластичная для термопластиков.
На заметку!Перед покраской детали используют адгезионный грунт специально для пластиковых конструкций, чтобы избежать возможных сколов краски с бампера.
Если на поверхности осталась старая покраска, ее тщательно удаляют и на этом месте наносят адгезионный грунт. Если конструкция новая, то его наносят на всю поверхность. Спустя 15 минут после нанесения можно приступать к покраске.
Видео ремонта бампера из пластика своими руками
О том, как отремонтировать бампер, который лопнул можно подробно узнать из видео. Пошаговая инструкция предназначена для качественной и без дефектов работы. Сначала проводят подготовительные процедуры: снимают деталь, чистят ее от грязи и краски. Затем выравнивают поврежденные края, восстанавливают предыдущую форму и грунтуют. Завершающий – это покраска.
Заделать на бампере трещину своими руками – это экономно. Достаточно лишь иметь при себе перечень необходимых материалов и инструментов, а также владеть информацией о правильном пошаговом процессе. Существует два основных способа ремонта поврежденного бампера: сварка и склейка. В работе пользуются материалом, который предназначен только для пластиковых конструкций.
Какой пластик используется в автомобиле?
Подсчитано, что каждые 10% снижения веса транспортного средства приводят к снижению расхода топлива на 5-7%. Текущие экономические и экологические проблемы делают создание более экономичных автомобилей главным приоритетом в автомобильной промышленности. Использование современных материалов, таких как алюминий и углеродное волокно, полезно, но разумное применение пластмасс имеет все большее значение.
Некоторые другие преимущества высокоэффективных пластиков, используемых в транспортных средствах, включают в себя:
— минимальную коррозию, позволяющую продлить срок службы автомобиля
— существенная свобода дизайна, позволяющая продвигать творчество и инновации
— гибкость в интеграции компонентов
— безопасность, комфорт и экономия
— вторичная переработк.
Вот лучшие 13 высокопроизводительных пластмасс, используемых в автомобильной технике. В то время как все 13 могут легко использоваться в одном автомобиле, только три типа пластмасс составляют
примерно 66% от общего числа высокоэффективных пластмасс, используемых в автомобиле: полипропилен (32%), полиуретан (17%) и ПВХ (16%) ,
1) Полипропилен (PP)
Полипропилен — это термопластичный полимер, используемый в самых разных областях. Насыщенный аддитивный полимер, изготовленный из мономера пропилена, он прочный и необычайно устойчивый ко многим химическим растворителям, основаниям и кислотам.
Применение: автомобильные бамперы, химические баки, изоляция кабелей, газовые баллончики, ковровые волокна.
2) Полиуретан (PUR)
Твердый полиуретан — это эластомерный материал с исключительными физическими свойствами, включая ударную вязкость, гибкость и устойчивость к истиранию и температуре. Полиуретан имеет широкий диапазон жесткости, от ластика до твердого шара для боулинга. Другие характеристики полиуретана включают чрезвычайно высокий срок службы при изгибе, высокую несущую способность и выдающуюся стойкость к погоде, озону, радиации, маслам, бензину и большинству растворителей.
Применение: гибкие пенопластовые сидения, пенопластовые изоляционные панели, эластомерные колеса и шины, автомобильные подвесные втулки, подушки, электрические герметики, твердые пластиковые детали.
3) Поливинилхлорид (ПВХ)
ПВХ обладает хорошей эластичностью, огнестойкостью, хорошей термостойкостью, высоким глянцем и низким содержанием свинца. Поливинилхлоридные формовочные смеси можно подвергать экструзии, литью под давлением, прессованию под давлением, каландрированию и формованию раздувом для образования огромного разнообразия продуктов, либо жестких, либо гибких, в зависимости от количества и типа используемых пластификаторов.
Применение: автомобильные приборные панели, оболочка электрических кабелей, труб, дверей.
4) ABS
Акрилонитрил-бутадиен-стирол представляет собой сополимер, полученный полимеризацией стирола и акрилонитрила в присутствии полибутадиена. Стирол придает пластику блестящую непроницаемую поверхность. Бутадиен, каучуковое вещество, обеспечивает устойчивость даже при низких температурах. Различные модификаторы могут применяться для улучшения ударопрочности, ударной вязкости и термостойкости.Применение: автомобильные кузовные детали, приборные панели, колпаки колес.
5) Полиамид (PA, Нейлон 6/6, Нейлон 6)
Нейлон 6/6 — это нейлон общего назначения, который можно формовать и прессовать. Нейлон 6/6 обладает хорошими механическими свойствами и износостойкостью. Он часто используется, когда требуется низкая стоимость, высокая механическая прочность, жесткий и стабильный материал. Нейлон хорошо впитывает воду и будет набухать в водной среде.
Применение: шестерни, втулки, кулачки, подшипники, атмосферостойкие покрытия.
6) Полистирол (PC)
Естественно чистый, полистирол обладает отличной химической и электрической стойкостью. Широко доступны специальные глянцевые и ударопрочные марки. Этот простой в изготовлении пластик обладает плохой стойкостью к ультрафиолетовому излучению.
Применение: корпуса оборудования, пуговицы, автомобильная фурнитура, витрины.
7) Полиэтилен (PE)
Полиэтилен обладает высокой ударопрочностью, низкой плотностью и обладает хорошей ударной вязкостью. Он может использоваться в самых разнообразных способах обработки термопластов и особенно полезен, когда требуются влагостойкость и низкая стоимость.
Применение: автомобильные кузова (армированные стеклом), электроизоляция.
8) ПОМ (POM — полиоксиметилен)
POM обладает превосходной крепкостью, жесткостью и пределом текучести. Эти свойства стабильны при низких температурах. ПОМ также обладает высокой химической и топливостойкостью.
Применение: внутренняя и внешняя отделка, топливные системы, малая шестерня.
9) Поликарбонат (PC)
Аморфный поликарбонатный полимер предлагает уникальное сочетание жесткости, твердости и ударной вязкости. Обладает отличными атмосферными, ползучими, ударными, оптическими, электрическими и термическими свойствами. Из-за своей исключительной ударной вязкости он является материалом для автомобильных бамперов, шлемов всех видов и заменителей пуленепробиваемого стекла.
Применение: бамперы, линзы фар.
10) Акрил (PMMA)
Прозрачный термопласт, PMMA часто используется в качестве легкой или устойчивой к разрушению альтернативы стеклу. Это дешевле, чем PC, но также более подвержен царапинам и разрушениям.
Применение: окна, дисплеи, экраны.
11) PBT (полибутилентерефталат)
Термопластичный PBT используется в качестве изолятора в электротехнической и электронной промышленности. Это очень химически и термостойкий материал. Также есть огнестойкие марки.
Применение: дверные ручки, бамперы, компоненты карбюратора.
12) Полиэтилентерафталат (PET)
ПЭТ в основном используется для создания синтетических волокон и пластиковых бутылок. Вы можете узнать об этом, прочитав ярлыки одежды, там он называется «полиэстер».
Применение: корпус рычага стеклоочистителя и корпуса редуктора, фиксатор фары, крышка двигателя, корпуса разъемов.
13) ASA (акрилонитрил-стирол-акрилат)
Как и ABS, ASA обладает высокой прочностью и жесткостью, хорошей химической стойкостью и термостойкостью, отличной устойчивостью к погодным условиям, старению и пожелтению, а также высоким глянцем. Будьте осторожны, чтобы не сжечь этот материал. При горении выделяется токсичный дым.
Применение: корпуса, профили, детали интерьера и наружного применения.
как это сделать и что для этого нужно?

Бампер относится к той разновидности элементов автомобиля, которые наиболее часто получают повреждение. Это обусловлено его целевым назначением – здесь гасится большая часть энергии удара при столкновении с посторонним препятствием. Поэтому на его поверхности появляются разного рода дефекты – царапины, сколы, трещины, проломы.
В современных моделях автомобилей наиболее часто встречаются обвесы из пластика – этот материал обладает рядом преимуществ перед другими вариантами:
- невысокая стоимость;
- технологичность;
- ремонтопригодность;
- красивый внешний вид;

- небольшая масса;
- невосприимчивость к коррозии;
- устойчивость к атмосферным факторам.
Производство бамперов налажено в основном за рубежом, поэтому у нас их стоимость достаточно высока – она включает в себя расходы на доставку, таможенные пошлины и т.д. В связи с этим в последнее время всё более широкое распространение получает изготовление бамперов, выполненное из пластика своими силами.
Некоторые автомобилисты в случае необходимости делают обвес для собственного автомобиля, чтобы не переплачивать за импортный. Есть такие, которые ручным способом делают подобную продукцию не только для собственных нужд, но и на продажу – речь идёт о кустарном производстве. Ну а кто-то уже успел наладить собственный бизнес, закупив профессиональное оборудование для производства бамперов и выпуская товар целыми партиями.


Смотрите также:
Индивидуальное производство
Практика показала, что изготовление бамперов, выполненное из пластика ручным способом, можно осуществлять даже в одиночку. Для этого не нужно специальное оборудование для производства бамперов и отдельное помещение – работу можно выполнять в собственном гараже, обходясь подручными средствами. Как правило, тот, кто занимается подобной деятельностью, сочетает её с предоставлением услуг по разным видам ремонта авто.
Работа по изготовлению бампера состоит из нескольких этапов:
- Разработка проекта – на этом этапе вычерчивают эскизы, определяются с формой и габаритами будущего изделия. В идеале, если речь идёт о постоянных заказах, несколько наиболее часто повторяющихся конструкций можно выполнить в цифровых 3-D-редакторах на компьютере. Если вы не знаете, как это сделать – обратитесь к профессиональному дизайнеру, предоставив ему чертежи и аксонометрические проекции. Обсудите проект с заказчиком, выслушайте все его пожелания и внесите необходимые изменения в проект.

- Изготовление матрицы – это наиболее важная процедура, от которой будет зависеть успех всей операции. Матрица – это форма для отливки будущего изделия. Для часто повторяющихся вариантов держите постоянные многоразовые матрицы, однако для выполнения индивидуального проекта понадобится изготовить специальную матрицу. Для одноразового употребления матрицу изготавливают обычно из технического пластилина, который хорошо держит высокую температуру и не разрушается под воздействием полиэфирной смолы. Для многоразовых матриц понадобится более прочный и надёжный материал. После того, как вылеплена основа, полиэфирную смолу разводят аэросилом и наносят на пластилиновую поверхность. Потом кладут стекломат «трёхсотку», а на него «шестисотку». В результате получаете изделие со стенками, толщина которых составляет 4 мм. В качестве разделяющей прослойки используют тефлоновую полироль – она нужна, чтобы можно было легко разъять матрицу и заготовку. Доводят изделие при помощи наждачной бумаги с разным размером зерна.

Если речь идёт о сложной конфигурации обвеса, его изготавливают частями, которые потом склеивают между собой:
- После изготовления матрицы приступают к изготовлению обвеса. Сначала обработайте матрицу воском и сверху – гелькоатом, который нанесите из распылителя или при помощи кисточки. Он нужен для того, чтобы придать будущему изделию влагоустойчивость. Потом, используя кисть или валик, положите прослойку полиэфирной смолы с отвердителем, на которую уложите стеклоткань. Сверху положите конечный слой, состоящий из смолы и алюминиевой пудры – вместо неё можете использовать аэросил. Достаньте изделие и дождитесь высыхания.
- В случае необходимости отшлифуйте поверхность, чтобы убрать неровности рельефа.
- Конечным этапом идёт покраска – используйте эмали для пластиковых поверхностей. Выбор тона зависит от того, какой краской покрашен автомобиль, для которого вы делаете бампер.
Этот метод вы можете самостоятельно применить в собственном гараже – вам для этого не понадобится специальное оборудование, лишь подручные средства. При ручном методе изготовления обвеса необходимы навыки обращения с материалами, а также внимание и аккуратность. Это процедура трудозатратная, требующая большого количества времени и сил.

Смотрите также:
Изготовление бамперов с помощью профессионального оборудования
Если речь идёт не о единичном изготовлении, а о партии изделий, понадобится профессиональное оборудование для производства бамперов, специальный цех и соответствующая технология.

В качестве оборудования для производства бамперов используют термопластавтоматы, которые осуществляют литьё пластика под давлением. Предварительно готовят специальные гранулы, используя соответствующий рецепт. В смесь для их приготовления включены такие ингредиенты, как полипропилен, каучук, световые стабилизаторы, температурные стабилизаторы и т.п. Рецептура построена таким образом, чтобы конечное изделие обладало нужными характеристиками:
- прочность;
- устойчивость к воздействию ультрафиолета;
- стойкость к перепадам температур;
- надёжность, долговечность и т.п.

Перед использованием гранулы просушивают, чтобы в процессе литья избежать образования раковин и других дефектов. Потом их подают в термопластавтоматы, где формируются готовые детали. При этом материал разогревается до высокой температуры, переходит в жидкое состояние и становится пригодным для литья. Он подаётся под давлением в пресс-форму, где застывает.
Застывшие заготовки поступают в цеха, где их зачищают и шлифуют. Последним этапом в производстве бамперов идёт покраска – для этого используют специальное оборудование или выполняют операцию вручную.
После того, как изделие готово, оно проходит процедуру контроля качества и поступает на склад, откуда его везут на торговые точки. Изделия, вышедшие из заводских цехов, часто качественнее и красивее тех, которые изготавливают кустарным способом. Это объясняется высоким уровнем автоматизации и унификации всех технологических процессов, что позволяет устранить в процессе разработки все факторы, которые негативно влияют на качество продукта.


Смотрите также:
Заключение
Изготовление пластиковых обвесов – работа, которая сегодня выполняется в производственных цехах или в кустарных условиях. И в том, и в другом случае достижимо высокое качество и эстетичный внешний вид изделия. Однако применение специального профессионального оборудования и соответствующих технологий ведёт к уменьшению трудозатрат и повышению качества конечного изделия.
[democracy]
[democracy]
Автор: Баранов Виталий Петрович
Образование: среднее специальное. Специальность: автослесарь. Профессиональная диагностика, ремонт, ТО легковых авто зарубежного производства 2000-2015 г.в. Большой опыт работы с Японскими и Немецкими авто.
Комментарии запрещены.
Эволюция автомобильного бампера: от железа к пластмассе
Многие из нас еще помнят бамперы, которые чинились кувалдой или выправлялись после удара сами. Теперь их приходится менять в сборе за большие деньги… А ведь когда-то у машин вообще не было бамперов! Мы проследили всю историю.
Первоначальное предназначение автомобильного бампера — поглощение энергии, возникающей при столкновении на небольших скоростях. Если взглянуть на ранние автомобили, то у них бамперов мы не увидим — машин было мало, и ездили они очень медленно.
Как все начиналось
Впрочем, были производители, опережавшие свое время. На некоторых моделях Packard уже в 20-е годы бамперы были доступны в качестве дополнительного оборудования. Ну а одним из первых серийных автомобилей с бампером в «базе» оказался Ford Model A.
Его бамперы были выполнены из двух тонких металлических пластин, соединенных перемычками и упругими кронштейнами, которые при несильном ударе пружинили и сохраняли форму. Хотя впоследствии бамперы стали важной, неотъемлемой частью дизайна, поначалу они выглядели практически одинаково на машинах любых марок.
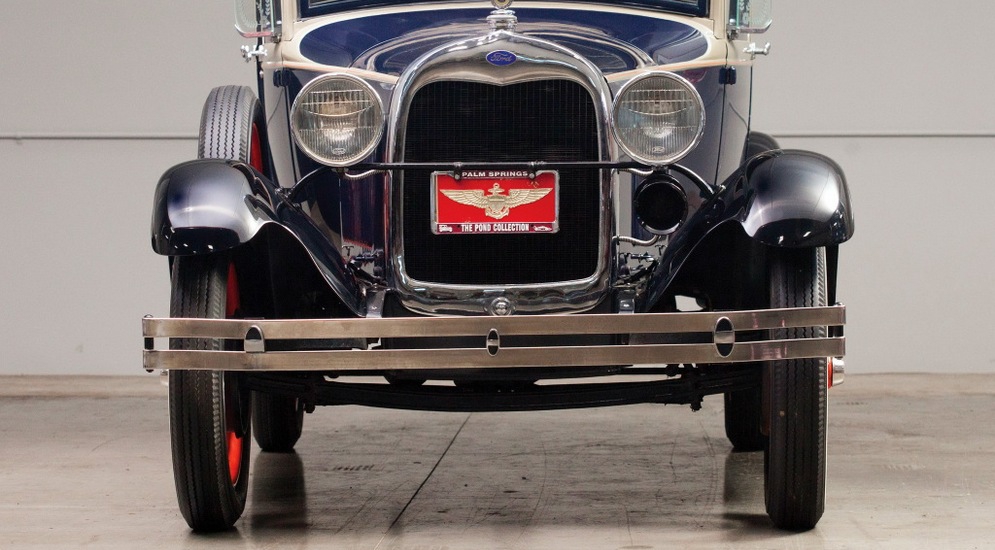
На фото: Ford Model A 1927
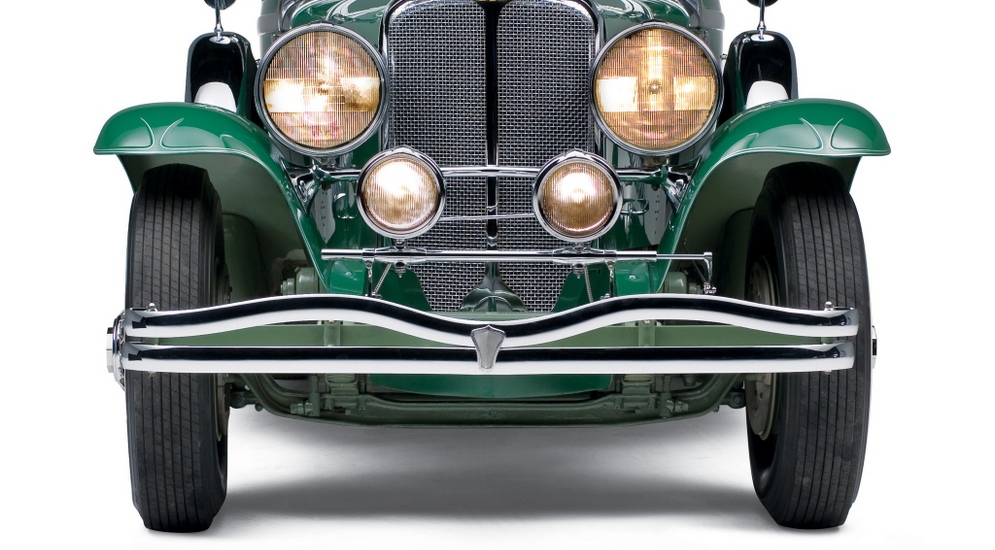
На фото: Duesenberg Model J 1929
Вскоре стало ясно, что возможностей таких бамперов недостаточно и их необходимо усилить. Тонкие полосы стали были заменены на массивные поперечные балки, и теперь при аварии поглощение энергии достигалось не за счет пружинного эффекта, а путем сминания металла.
Помимо улучшения утилитарных качеств, предпринимались шаги по изменению непритязательного вида конструкции в виде трансформации перемычек в солидные массивные хромированные «клыки» и изобретения монолитного бампера.
Золотой век дизайна бамперов
В 1940-х годах возникают закругления на бампере, заходящие на боковину кузова, и «фартуки» между кузовной панелью и брусом бампера, изолирующие кузов от грязи. Одним из примеров машин с «опоясывающим» бампером является Nash Ambassador с молдингами, идущими от бампера по всему кузову.
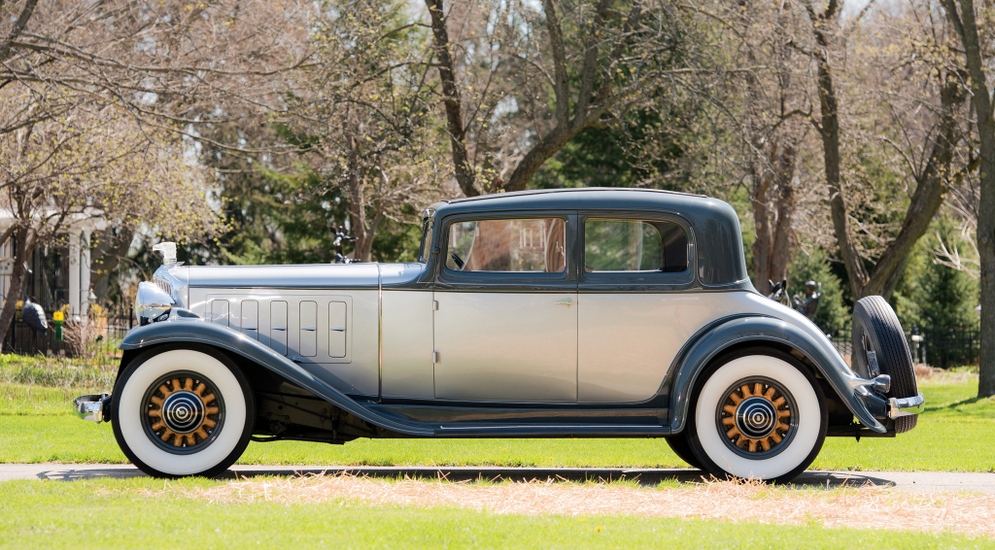
На фото: Nash Ambassador
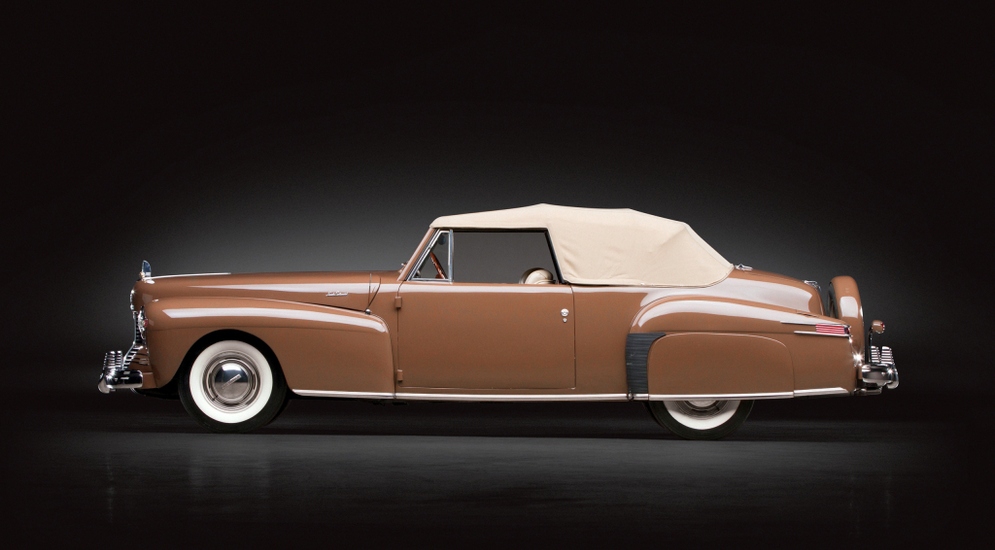
На фото: Lincoln Continental 1942
В 50–60-х годах концепции развития формы бампера в разных частях мира разошлись. Европейцы и большая часть японских компаний продолжали эксплуатировать идею узкого бампера, украшением которого служил только хром. Чтобы оберечь блестящую поверхность от царапин, были добавлены резиновые буртики. Кроме того, в бамперы иногда встраивали повторители указателей поворотов. Практически все изменения в форме бамперов диктовались соображениями большей прочности и безопасности, а также лучшей ремонтопригодности.
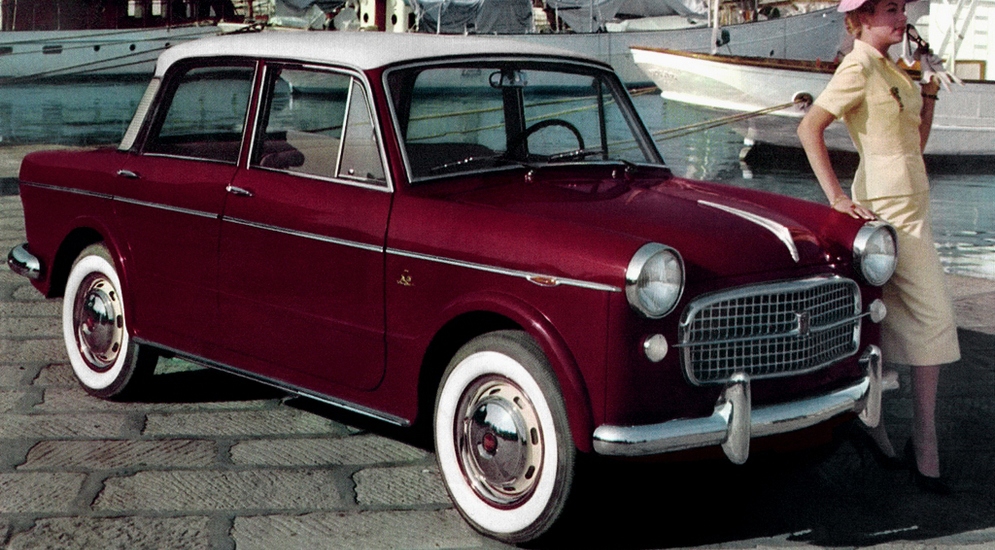
На фото: Fiat 1200 1957 г.
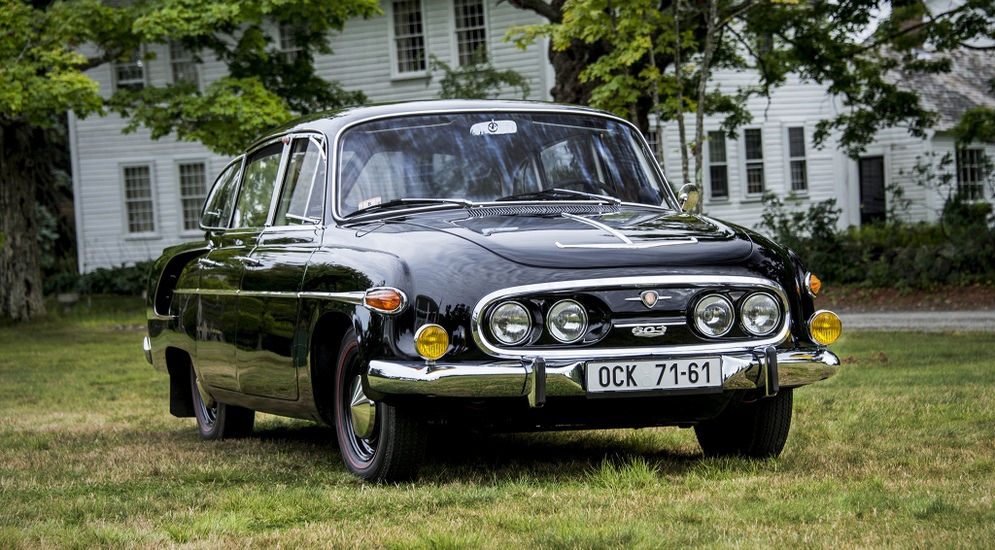
На фото: Tatra 603 II 1968 г.
Американские модели тяготели не к безопасности, а к эстетике, поэтому в 50-х годах они щеголяли сложными, многоэтажными конструкциями бампера, включающего в себя еще и функции фальшрешетки радиатора и даже передних крыльев. Так началась эпоха интегрированных бамперов, представлявших собой кузовные панели. Как и в Европе, в бамперы встраивали «поворотники» и противотуманные фары, а поскольку бампер должен был еще и давать доступ воздуху для лучшего охлаждения двигателя, добавляли многочисленные прорези.
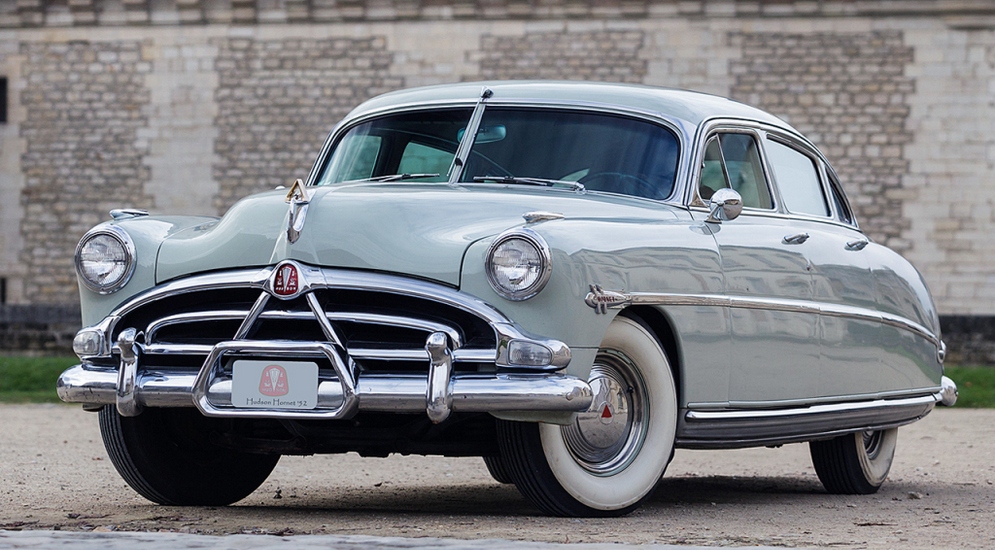
На фото: Hudson Hornet Sedan 1952 г.
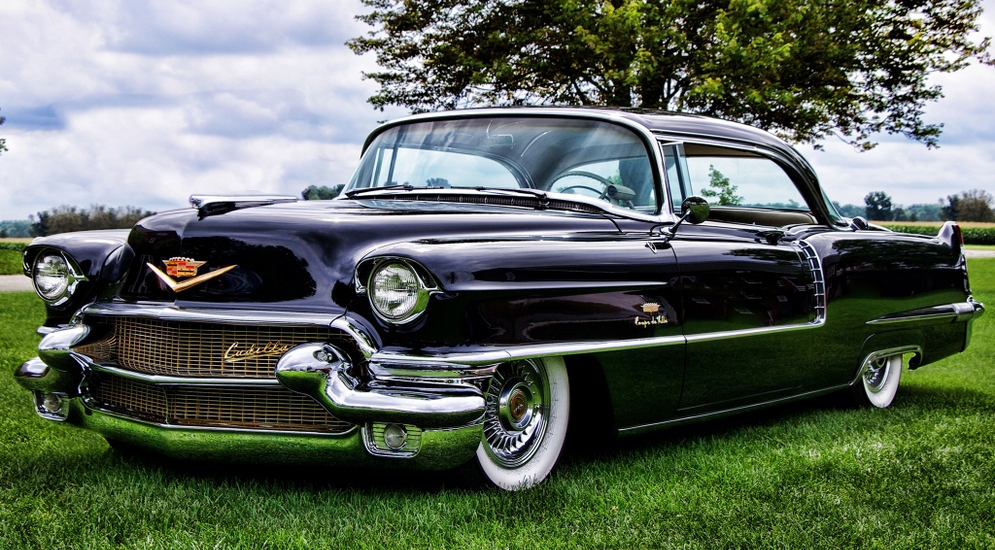
На фото: Cadillac Sixty-Two Coupe de Ville 1956 г.
Расцвет буйства форм бамперов пришелся на 50–60-е годы. В отсутствие каких-либо требований к пассивной безопасности, производители были вольны творить, что хотели. Существовали полностью интегрированные в передок бамперы, чьи концы сильно выдавались вперед, как бы довершая линии крыльев; едва заметные защитные металлические полоски бамперов на спортивных машинах, даже не выступающие за пределы габаритов; бамперы, обрамляющие решетку радиатора и фары; пластиковые интегрированные бамперы… Некоторые спортивные японские машины также использовали американскую стилистику минималистичных бамперов в своем облике.
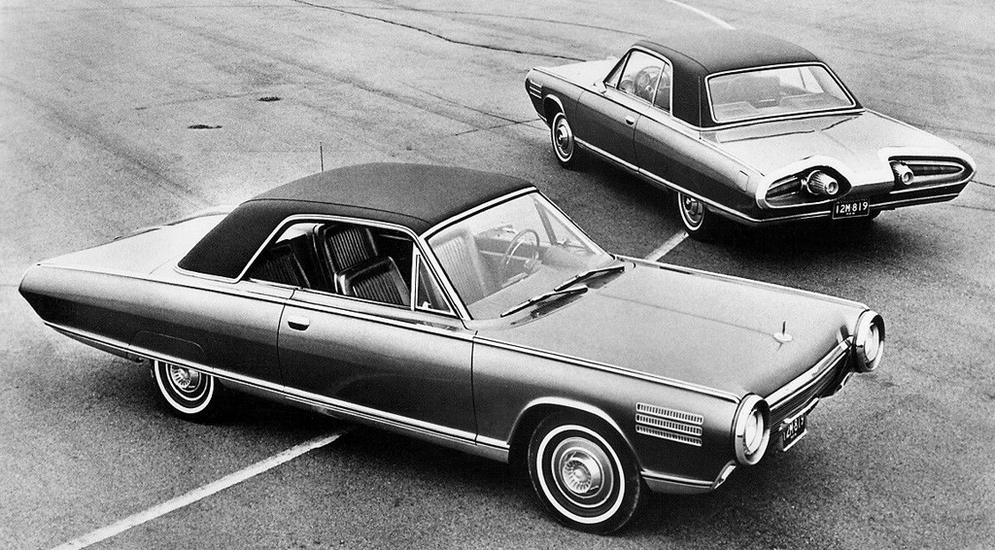
На фото: Chrysler Turbine Car 1963 г.
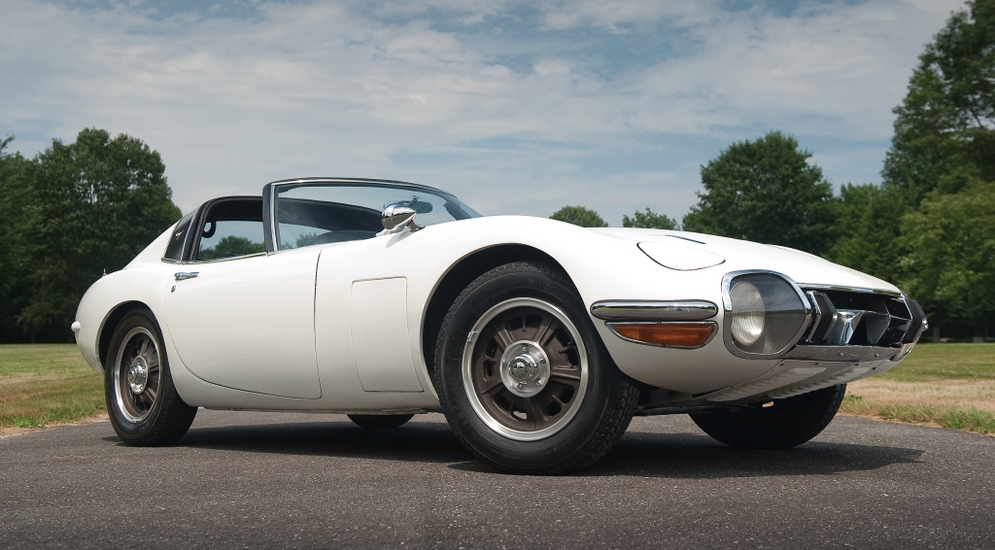
На фото: Toyota 2000GT Targa 1966 г.
Безопасность выходит на первый план
Такое разнообразие закономерно привело к тому, что бампер потерял свою первоначальную функцию и стал причиной многих неоправданных затрат после ДТП. В автомобильную индустрию вмешалось правительство США, которое постановило, чтобы с 1973 года все выпускаемые автомобили имели передний бампер, выдерживающий столкновения до 8 км/ч без последствий для фар, и задний бампер, предотвращающий разрушение фонарей и элементов топливной системы при ударах на скорости до 4 км/ч.
В 1980 году законы ужесточились, утвердив недопустимость каких-либо повреждений на скоростях до 8 км/ч более вмятины глубиной более 1 сантиметра и смещения бампера более чем на 2 сантиметра относительно штатного положения.
Новые законы были восприняты автопроизводителями неоднозначно, и в конце концов под их давлением требования для машин 1983 года выпуска смягчились: бамперы должны были выдерживать удар только на скорости до 4 км/ч.
Помимо возврата к старым нормам, вводилось ограничение высоты бампера в пределах 41-51 см над уровнем земли (любопытно, что на вэны, пикапы и SUV закон не распространялся, поскольку внедорожные способности рабочих машин могли от этого пострадать). После этого уже стали негодовать потребители и страховые компании, которым пришлось больше платить за ремонт менее прочных бамперов, но их возмущение не получило отклика. Правительство аргументировало свое решение тем, что якобы среднестатистические затраты на больший расход топлива с более массивным бампером, а также доплата за его большую себестоимость превышают затраты на стоимость ремонта при легком ДТП.
Конечно, об экзотичных вариантах бамперов теперь не было и речи. Стандарту могли соответствовать только широкие, массивные бамперы с «клыками», резиновыми накладками и демпфирующими элементами.
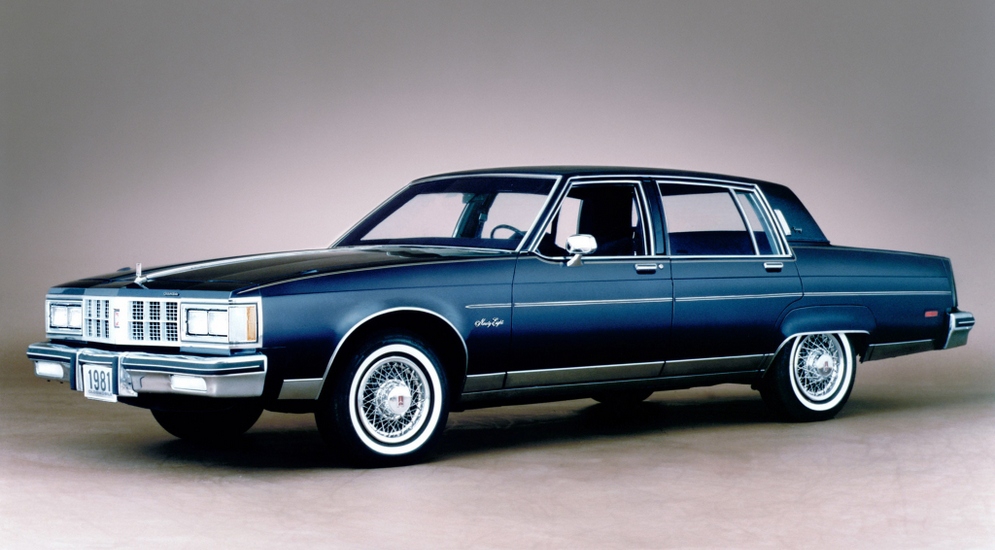
На фото: Oldsmobile 98 Regency Brougham Sedan 1981 г.
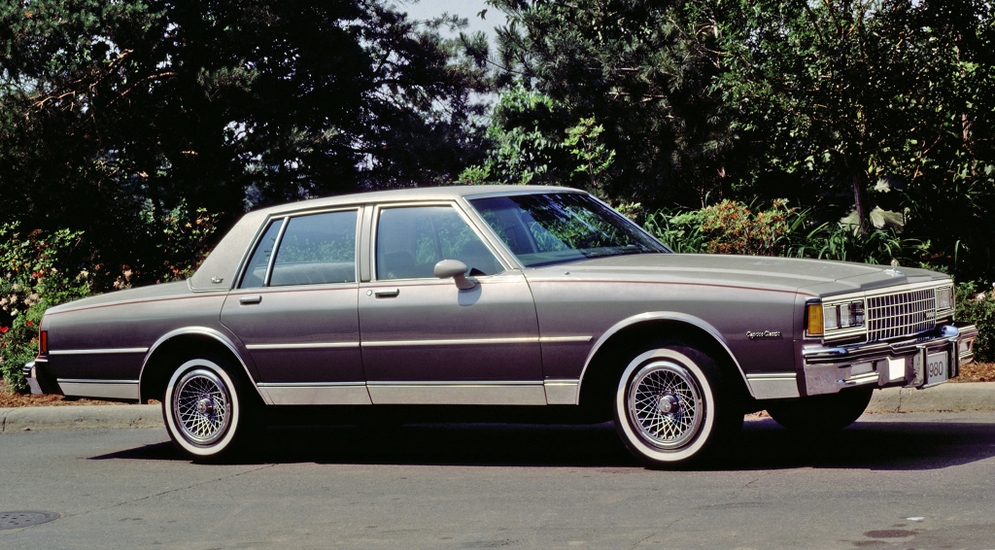
На фото: Chevrolet Caprice Classic 1980 г.
Пластик наносит ответный удар
Тем временем в Европе в 1976 году появляется автомобиль Simca 1308 с интегрированными пластиковыми бамперами контрастного цвета по отношению к кузову. Идею подхватывают многие европейские автопроизводители, устанавливая на свои модели неокрашенные черные или серые бамперы, а в конце 80-х годов их уже красят в цвет кузова.
Но здесь отдельно стоит (у)помянуть почившую недавно шведскую компанию SAAB, которая в 1971 году впервые ставит на свою модель 99 самовосстанавливающийся пластиковый бампер, который гарантированно выдерживал столкновение на скорости до 8 км/ч, проминался и восстанавливал форму снова. Подобные конструкции ставились впоследствии на многие машины, в том числе и на советские Москвич-2141 и все семейство Самара: ВАЗ-2108, 2109 и 21099. С точки зрения практичности решение было уникальным, но вот силу удара на средних и высоких скоростях такие бамперы поглощали плохо и постепенно сошли с автомобильной сцены.
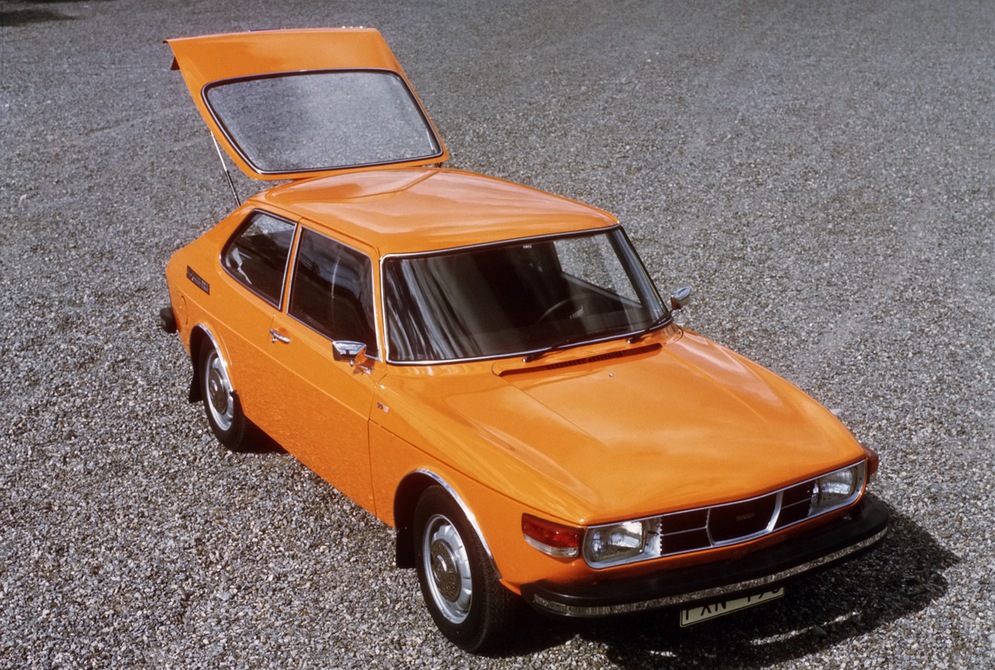
На фото: SAAB 99 1971
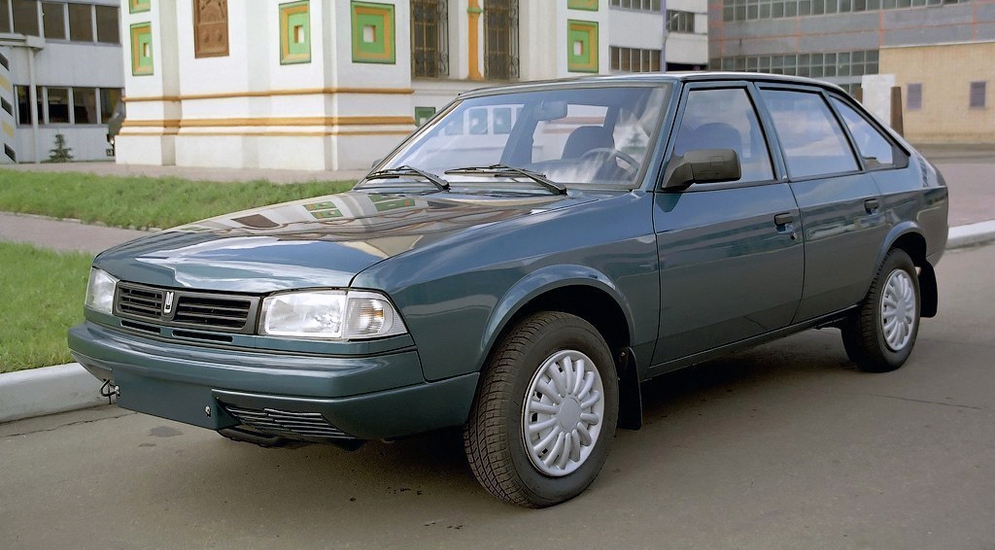
На фото: Москвич 2141 Святогор
Со временем облицовка бампера начинает играть фактически декоративную функцию, а характер деформации задают металлические усилители, скрытые внутри. По мере наводнения рынка США европейскими машинами стеклопластиковые и термопластиковые бамперы распространяются и среди американских моделей, а европейские производители вынуждены оснащать машины другими бамперами для американского рынка, «заточенными» под более жесткие требования.
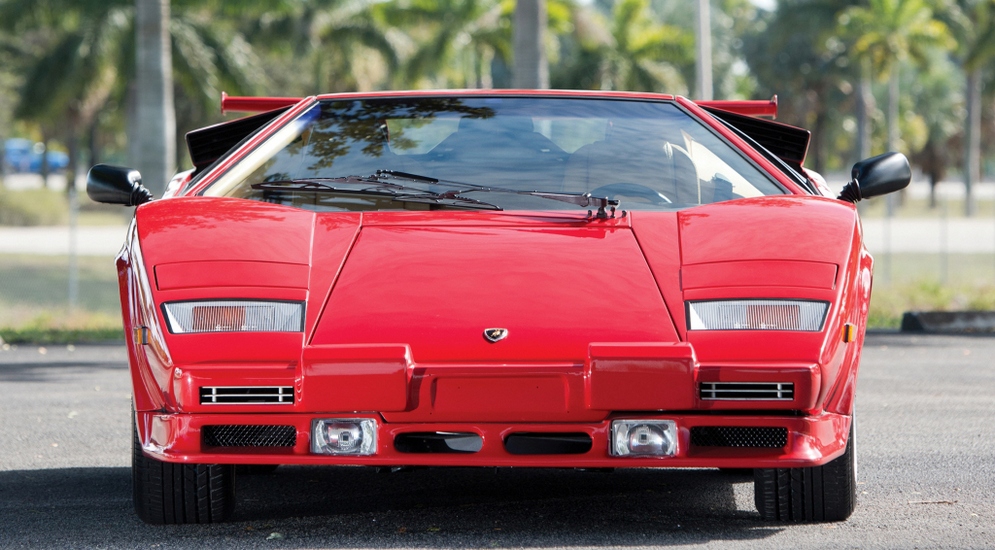
На фото: Lamborghini Countach US-spec
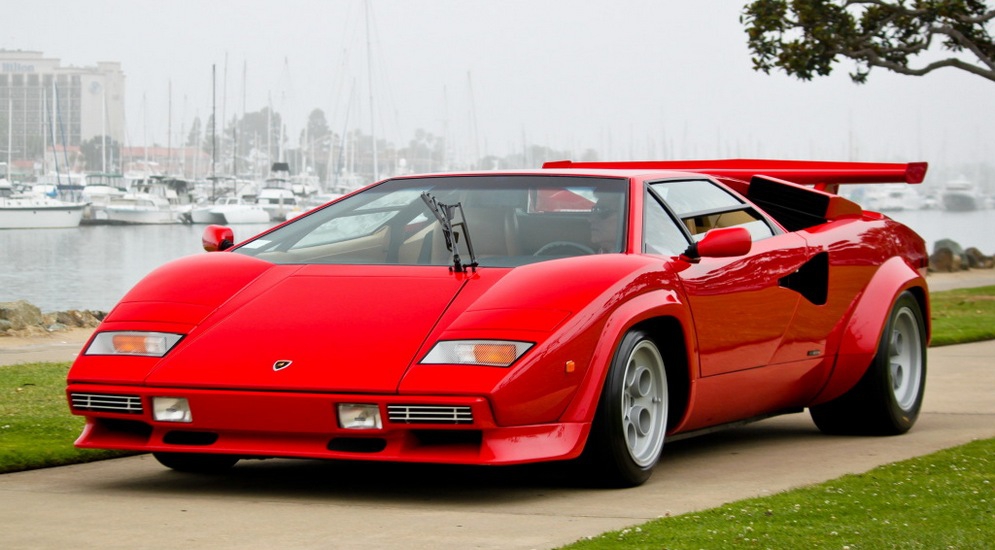
На фото: Lamborghini Countach EU-spec
А что теперь?
Сегодня наиболее распространены интегрированные бамперы, изготовленные из пластика. Обычно это цельнолитая объемная конструкция с деформируемым элементом, которая устанавливается в передней части автомобиля на двух (или большем числе) несущих кронштейнах. Объемный бампер из эластичного пластика наилучшим образом амортизирует удары, а также наносит минимальный вред ногам человека или животным при столкновении. При небольших столкновениях форма бампера на первый взгляд остается прежней, однако деформируемый элемент внутри рассыпается на части. Так что повышение пассивной безопасности оборачивается возросшей ценой восстановительного ремонта после ДТП.
Намного реже встречаются бамперы из углепластика. Обычно это прерогатива суперкаров, однако есть и сторонние компании, предлагающие заменить простой автомобильный пластиковый бампер на такой же из углеродного волокна. Карбон намного прочнее и легче любого пластика, но стоит существенно дороже.
Металлические бамперы на серийных машинах ушли в прошлое из-за особенностей дизайна современных автомобилей и новых требований к безопасности. Но что делать любителям внедорожных вылазок, если штатные крашеные пластмассовые бамперы портятся от контакта с любой веточкой?
Альтернатива — установка силового бампера. Качественные бамперы усиленного типа делаются из согнутого цельного листа металла, а крепления рассчитываются таким образом, чтобы разрушиться от сильного удара, иначе силовой бампер передаст энергию столкновения на двигатель, кузов и сидящих в нем людей. Стоит отметить, что официальный техосмотр с таким бампером пройти не удастся.
В заключение можно сказать, что современные окрашенные бамперы сложносочиненной формы не только не оберегают владельца от излишних затрат, но и прибавляют головной боли при остановке у высокого поребрика или парковке в условиях ограниченного пространства. Впрочем, способы защиты бампера всё равно есть: например, «бронирование» пленкой или даже применение малосимпатичных резиновых накладок.

Читайте также:
как и чем выполняется, техника, оборудование и материалы
Бампера новых моделей автомобилей изготавливаются из пластика. Это многоцелевой и дешевый материал, из которого делают бампера разной конструкции. К сожалению, они достаточно хрупкие.
Вы могли заметить, что даже на новых авто пластиковый бампер облеплен мелкими царапинами, будто это предусмотрено производителем.
Что уже говорить о многолетних машинах, на бамперах которых присутствуют вмятины, царапины, а иногда и дыры, которые со временем, без ремонта, становятся все больше.
Кроме таких уронов, регулярно можно встретить сколы, царапины от бордюров и ДТП. Многие владельцы автомобилей не ремонтируют бампер, а те, кто заботятся о внешнем виде автомобиля — отправляются на СТО за ремонтом или стараются отремонтировать сами.
Во многих автомобильных мастерских варят пластиковые бампера при помощи сварочного фена. Это простой способ, который быстро и качественно починит сломанное изделие.
Это можно сделать и самому, купив необходимый комплекс техники. Поговорим немного о том, как варить бампер с повреждениями. Основываясь на схему работы, можно попробовать отремонтировать своими руками.
Содержание статьиПоказать
Методика починки
Рассмотрим основные выражения. Все в основном называют бамперы пластиковыми, потому что при взгляде на них, они так и выглядят. Но в процессе производства используют не обычный пластик, а пропиленовый или полиуретановый.
Такие полимеры относят к термопластам и считаются устойчивыми к удару. Это позволяет им справляться с нагрузками из вне. Конечно, они быстро царапаются, но серьезные повреждения могут нанести только сильные нагрузки в виде столкновения.
Поняв эти тонкости, вы сможете в будущем лучше понимать методику работы со сваркой. Потому что в таком случае, варить надо не обычную пластмассу, а полимер, способный выдержать нагрузку, они все-таки немного другие, по сравнению с обычной пластмассой.
Но, в основном, их называют «бампер из пластика» или «бампер из пластмассы», имея в виду термопластовый бампер. Для удобства, мы будем применять именно такое определение.
Сварка бамперов из пластика заключается в двух стадиях: подготовка и сварка. Дальше поговорим детальнее о них.
Подготовка

Подготавливаем пластиковый бампер для варки. Для начала очищаем бампер от любых загрязнений. Если опустить этот шаг, то качество ремонта будет посредственным и потребуется его переделывать в ближайшее время.
Пластиковый бампер не обязательно демонтировать, можно производить ремонт прямо на автомобиле, но для лучшего эффекта все-таки лучше его снять.
В автомобильных мастерских пластиковый бампер устанавливают на специальный постамент для покраски, но его можно сделать самостоятельно из того, что есть под рукой.
Кроме стандартной очистки от загрязнений, необходимо подвергнуть шлифовке в том месте, где будет ремонт.
С этим неплохо справится наждачка или круг для шлифовки в комплексе с шлифовочной машиной или стандартной болгаркой. Это остановит увеличение трещины.
Дальше, если будете варить трещину, нужно обработать ее края. Лучше сделать V-образную форму. Для заделывания дыр или сколов, края обрабатывать не надо. После всех этих манипуляций бампер необходимо протереть влажной тряпочкой и обезжирить.
Материалы для работы

Для самостоятельного ремонта подготовьтесь купить комплекс приборов и инструментов. Без них невозможно починить качественно.
Для начала, вам пригодится сварочный фен или термопистолет (лучше применять профессиональный или полупрофессиональный инвертор), особые прутья для сварки при ремонте пластиковых бамперов (материал их изготовления должен быть идентичный материалу бампера), армирующая сетка из металла, тренога, стеклоткань, термореактивный полимер и замазка, предназначенная для работ с пластмассой, хомут для раскладки сетки.
Процесс сварки

Возьмем фен для сварки и термопистолет. Настраиваем необходимые градусы нагрева. Это зависит от материала, из которого изготовлен бампер и температура его плавления.
Также важно проверить, чтоб приобретенные прутья были изготовлены из того же материала, что и пластиковый бампер.
Для уверенности, что градусы выставлены правильно и прутья соответствуют материалу бампера, сделайте сварку на маленьком кусочке. Так у вас будет меньше шансов испортить всю деталь машины.
Если все соответствует, то начинайте ремонт. Мы опишем сварку трещин, потому что это основная проблема, которая встречается в работе владельцев автомобилей.
Для начала надо обварить края щели точечно. Дальше помещаем прут в щель и плавим сварочным феном, чтобы заполнить пространство. Эти действия необходимо провести с обеих сторон. Этот же метод применяется для устранения дырок.
Для лучшего соединения рекомендуют применять армирующую сетку из металла. От нее отрезают размер немного больше повреждения и накладывают на него.
Потом нагревают феном и приваривают. При отсутствии сетки, можно использовать стеклоткань, используя вместо инвертора термоактивный полимер.
После варки используют шпаклевку на место повреждения (если они были масштабными) и шлифуют его. После этого надо прогрунтовать, прокрасить изделие и покрыть защитным лаком.
Можно прокрасить только то место, которое ремонтировали, но лучше прокрасить всю деталь. Тогда не будет видна разница между ремонтируемым местом и заводским.
Заключение
Сварка бампера из пластика — не очень сложный процесс, как иногда кажется. Тут главное — обрести небольшой опыт работы с феном для сварки и варить с осторожностью.
Если вы не опытны в работе с феном, то лучше наработать опыт на куске пластика, а потом приступать к самому ремонту.
Для самостоятельного ремонта лучше купить оборудование для ремонта средней цены. Не рекомендуем приобретать дорогой фен для сварки, который не будет часто использоваться и вы не поймете всю его прелесть.
Присмотритесь к повреждениям и проконсультируйтесь с продавцом, какое оборудование лучше приобрести для их ремонта.
Не спешите покупать самый дешевый или самый дорогой аппарат, лучше купить средний. В интернете есть широкий выбор, где вы можете выбрать себе понравившийся агрегат и почитать отзывы пользователей. Обратите внимание на сборку и удобство использования.